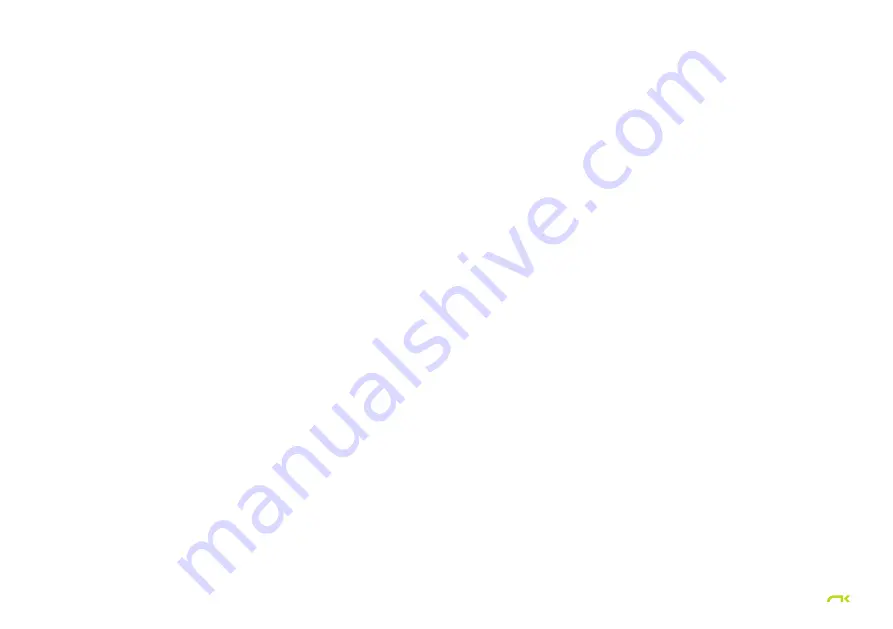
5
gliders. Furthermore it is full of small details destined to enhance the
pilots’ comfort and to improve the performance of the SLE, RAM, DRS,
TNT and 3 line profile.
The use of the SLE (Structured Leading Edge) allows reinforcement of the
leading edge preventing any deformation during turbulence. The airflow
is also vastly improved over the entire front span of the glider.
(See
http://niviuk.com/technology.asp?id=JNKPKPN4
)
The RAM AIR INTAKE technology presents an internal positioning for the
air entrance to allow an optimal maintenance of the internal pressure as
well as an improving of the laminar flow on intrados. What’s the result?
Gaining turbulent air absorption in the leading edge, more consistent at
every speed and a better performance while assuring maximum security.
(See
http://www.niviuk.com/technology.asp?id=JNKQKNP4
)
DRS.-The trailing edge has been reinforced with small ribs that make this
part flatter in order to spread the pressure out evenly. It means better
air-flow and less drag on this important part of the glider. The addition
of these ribs gives exceptional handling (better and more efficient when
turning) and more control and precision.
TNT.- It is a technical revolution. It underlines building the internal
structure of the glider with Nitinol to make the profile more uniform and
the glider lighter for better flight performance. Moreover, the Nitinol is
resistant to deformations, hot temperatures and breaks as well as more
resistant to the glider folding process.
3LT.-Its powerful profile, a detailed internal architecture structure and the
use of high-tech strength materials make possible a significant reduction
of the total length of suspension lines in order to reduce the parasite
resistance and the weight of the glider to gain efficiency.
Not a single millimeter of error is possible in the manufacturing process
from Olivier’s computer to the cutting of the fabric. An automatic process
controlled by a laser-cutting program cuts each of the sections that
compose the different parts of the wing. This program not only cuts the
pieces of fabric but it also paints the guideline marks that will aid the
assembly; it also numbers the separate pieces of material. All this is
carried out before human handling of the pieces begins. So we eliminate
possible and understandable errors that may occur during this delicate
procedure.
The lines are semi-automatically manufactured and all the sewing is
finished under the supervision of our specialists. The jigsaw puzzle of the
assembly process is made easier using this method. We minimize the
processes while making the quality control more efficient. All the different
parts of the canopy are cut and assembled under the strict conditions
induced by the automation of the whole process.
It is strongly recommended that all lines are thoroughly checked by the
pilot prior to every flight and ultimately checked by a service centre or
Niviuk dealer after every 100 hours of flight. We should not forget that we
are using materials with great performance but that they need a rigorous
check before every flight.
All NIVIUK Gliders go through an extremely thorough and efficient final
inspection.
Every single line of each glider is measured individually once the final
assembly has concluded. Each wing is then individually inflated for the
last visual revision.
Each glider is packaged following the maintenance and conservation
instructions recommended for the advanced materials. NIVIUK Gliders
are made of first class materials as demanded by the performance,
durability, and homologation requirements of the present-day market.
Information about construction materials is given on the last pages of this
manual.
Summary of Contents for IKUMA 21
Page 1: ...USER S MANUAL IKUMA...
Page 17: ...10 3 RISERS ARRANGEMENT 17...