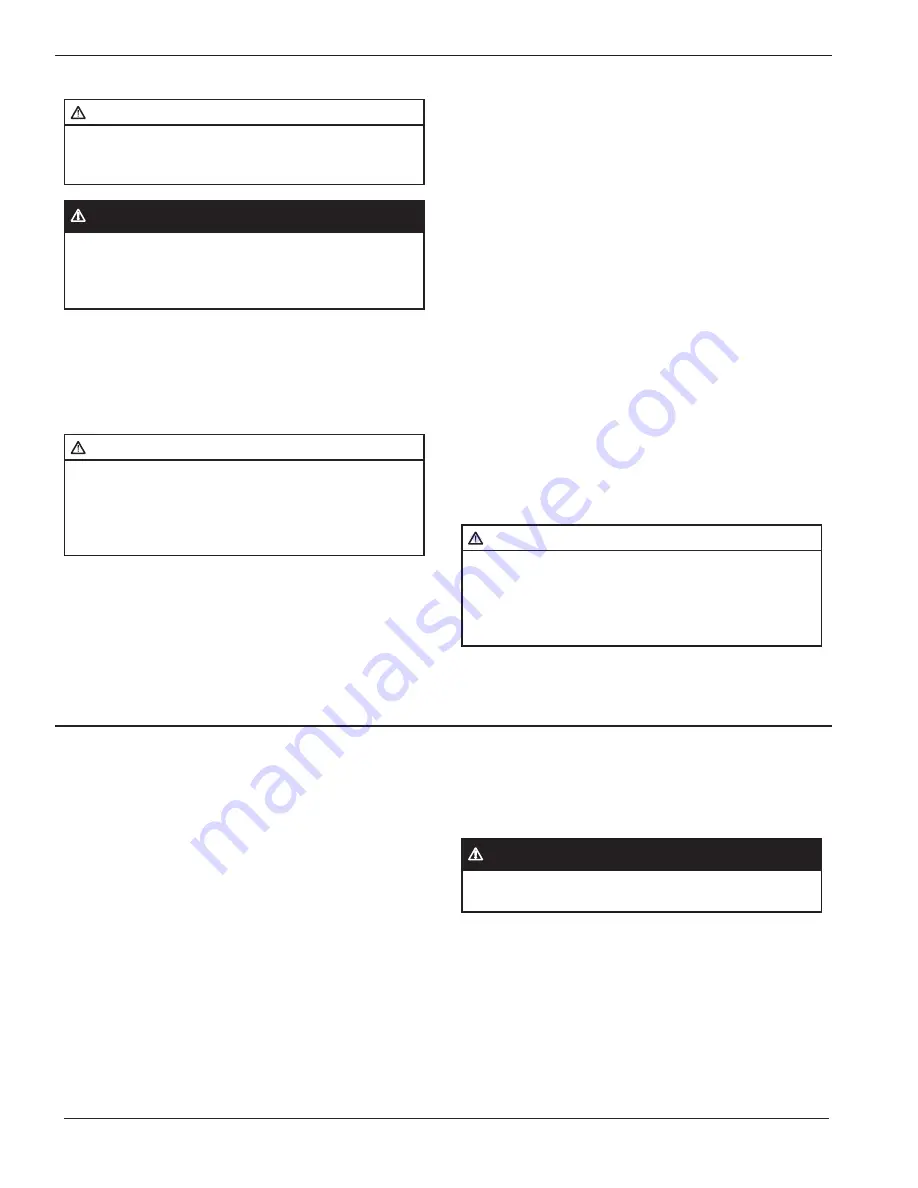
16
ingersollrandproducts.com
8.6 INITIAL START-UP
NOTICE
For water cooled models, the water valve must be
manually opened to ensure that the condenser is
full of water prior to start-up.
CAUTION
Allow 8 hours of warm-up time for the crankcase
heater prior to start up. Crankcase heater is
connected directly to the incoming power and is
energized at all times.
8.6.1 START- UP SEQUENCE
Apply power to dryer. LCD Panel will illuminate. The
Anti-Short Cycle delay will commence counting
down. Remaining time on the Crankcase heater will
also countdown.
NOTICE
After installation or a prolonged shutdown, start
the dryer with no air load (no air flow). This enables
the dryer to reach its proper operating temperature
in the shortest time possible (typically within 30
minutes for Nirvana™ Cycling dryers).
Start Dryer, using one of the following methods,
depending on Start Mode setting:
Manual Mode - Press the ON pushbutton.
Auto Restart Mode - No additional action required
Remote Automatic Mode - Close the remote contact.
•
•
For Nirvana™ Cycling dryers, the circulating pump
will be energized and will run continuously. Provided
the CHILLER TEMPERATURE is greater than the
Compressor Off Set point plus 4° F and the anti-
short cycle delay and crankcase heater delay have
timed out, the refrigeration system will energize. As
the system operates and thermal mass temperature
drops, the suction pressure will be lowered to
between 40 and 65 psig.
After the alarm delay, provided the Chiller Temperature is
greater than the HIGH TEMPERATURE ALARM set point, the
dryer will go into HIGH TEMPERATURE ALARM. The LCD panel
will indicate the alarm and the refrigeration system will
continue to operate. Pressing the SELECT DISPLAY button
will permit viewing of the available dryer parameters during
this alarm condition. Note that the alarm condition screen
will reappear after approximately 30 seconds until the alarm
condition is cleared.
The CHILLER TEMPERATURE will gradually drop as indicated
on the display. Once the temperature falls below the
HIGH TEMPERATURE ALARM set point, the alarm will reset
and the LCD panel will return to its default display. After
the refrigeration system shuts off, air flow may be slowly
introduced to the dryer.
NOTICE
If power is removed from the dryer for less than
two hours, the crackcase heater delay will be
automatically bypassed. If, however, the power is
removed from the dryer for more than two hours,
the full crankcase heater delay must be observed.
•
9.0 SCHEDULED MAINTENANCE
9.1 INTRODUCTION
Ingersoll Rand
Nirvana™ Cycling refrigerated air dryers
require little maintenance. These dryers utilize hermetically
sealed compressors which do not require any lubrication.
Fan motors require lubrication at both oil ports every
six months.
Ingersoll Rand
recommends component
inspection and service at regular intervals to obtain
maximum performance from your dryer.
9.2 REFRIgERANT CONDENSER
For standard dryers, regular inspection and cleaning of the
condenser is recommended.
Ingersoll Rand
dryers may
be equipped with an optional ambient air filter designed
to protect the condenser from dirt and debris that can
accumulate on the condenser. For proper operation with
this option, it is imperative that this filter be inspected and
cleaned on a regular basis. Annual replacement of the filter is
recommended.
For applications where excessive dirt, dust or debris is
encountered, more frequent inspection and cleaning may be
required.
9.3 PRE-FILTERS AND POST-FILTERS
WARNING
Depressurize the system before disassembling
filters. Failure to do so may result in injury or death.
Filter elements should be changed every 6 months to 1
year. Change carbon elements when hydrocarbons are first
detected downstream or every six months, whichever comes
first.
Certain filters contain multiple elements. When replacing
filter elements, all elements should be replaced
simultaneously. Mixing new and old elements can result in
reduced air quality.
8.0 INSTALLATION AND INITIAL START-UP
120.26A D4290NCHPW400F Installation Operation and Maintenance Manual