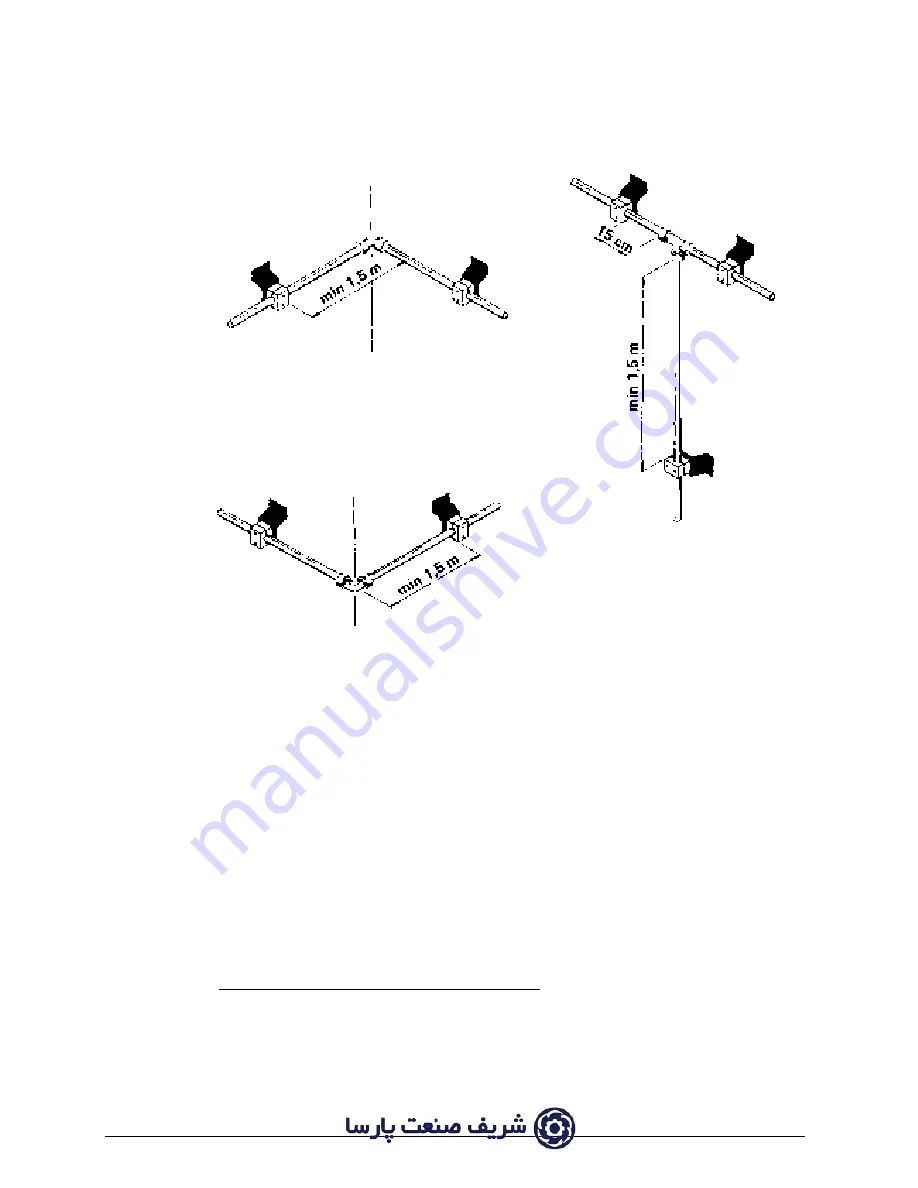
27
Original Instructions
FIXATION AT CORNERS AND TEE CONNECTORS
Standard distance between pipe brackets is some 2 m.
MOUNTING OF PIPE LINES/GENERAL INSTRUCTIONS
- Shorten the pipes by sawing off and take off burrs.
- When bending the pipe bending radii should not be smaller than those stated in the chart
under “U-bends/hose connections” and the bending should always be completed in a bend-
ing tool with rolling matrixes in order to prevent deformation of the pipe.
- Union nut and cutting ring should be greased with oil and the cutting ring should be pre-fitted
to the pipe in the screw joint or the annealed pre-mounting socket before fitting the pipe.
- Place the pipe brackets at a maximum interval of 2 m.
- Use
∅
6 hexagon-headed screw with expansion joint for wall or concrete walls when
mounting wall fittings, alternatively use a knock-type anchor for concrete walls, e.g. HILTI
type HPS 8/30.
- In systems meant for hot water, care should be taken to place the pipe brackets on a straight
line in order to prevent the lengthwise expansion of the pipe.
Summary of Contents for DELTABOOSTER
Page 5: ...5 Original Instructions...
Page 22: ...22 Original Instructions...