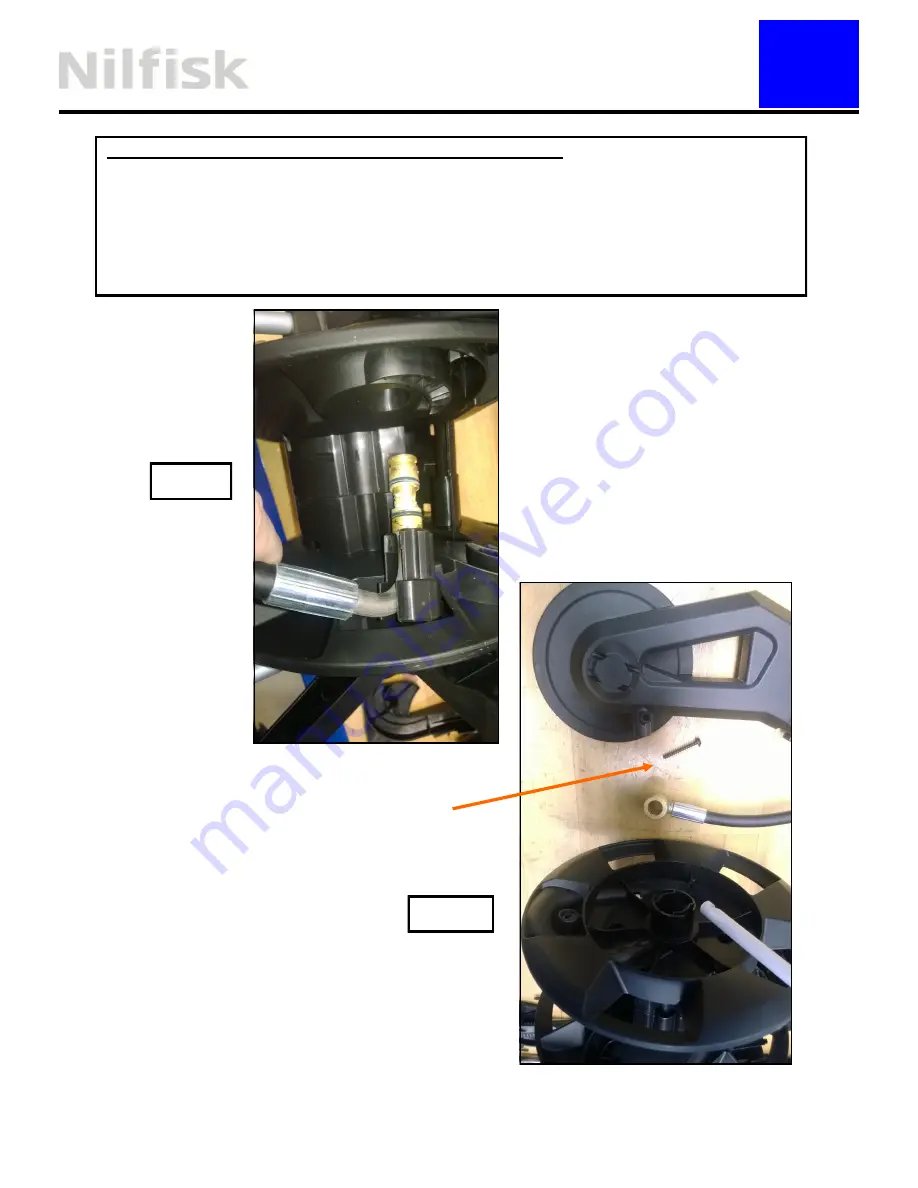
18
D
Service / Repair.
Disassembly / assembly of the hose reel - X-TRA models
1.
The hose can be removed from the internal hose (Fig 22)
2.
Dismount the 2 TORX screws (1 each side) from the aluminium hose guide (Fig 23)
Note the length of those 2 screws are longer than all other screws.
Fig. 23
Fig. 22
Summary of Contents for E130.3 X-TRA
Page 1: ...Repair Manual E130 3 E130 3 X TRA E140 3 X TRA E145 3 X TRA...
Page 5: ...5 C Structure Cabinet parts overview Max Torque for plastic screws 2 0 Nm...
Page 6: ...6 C Structure Hose reel overview...
Page 27: ...27 F Function Motor pump function of New Excellent Machine standby...