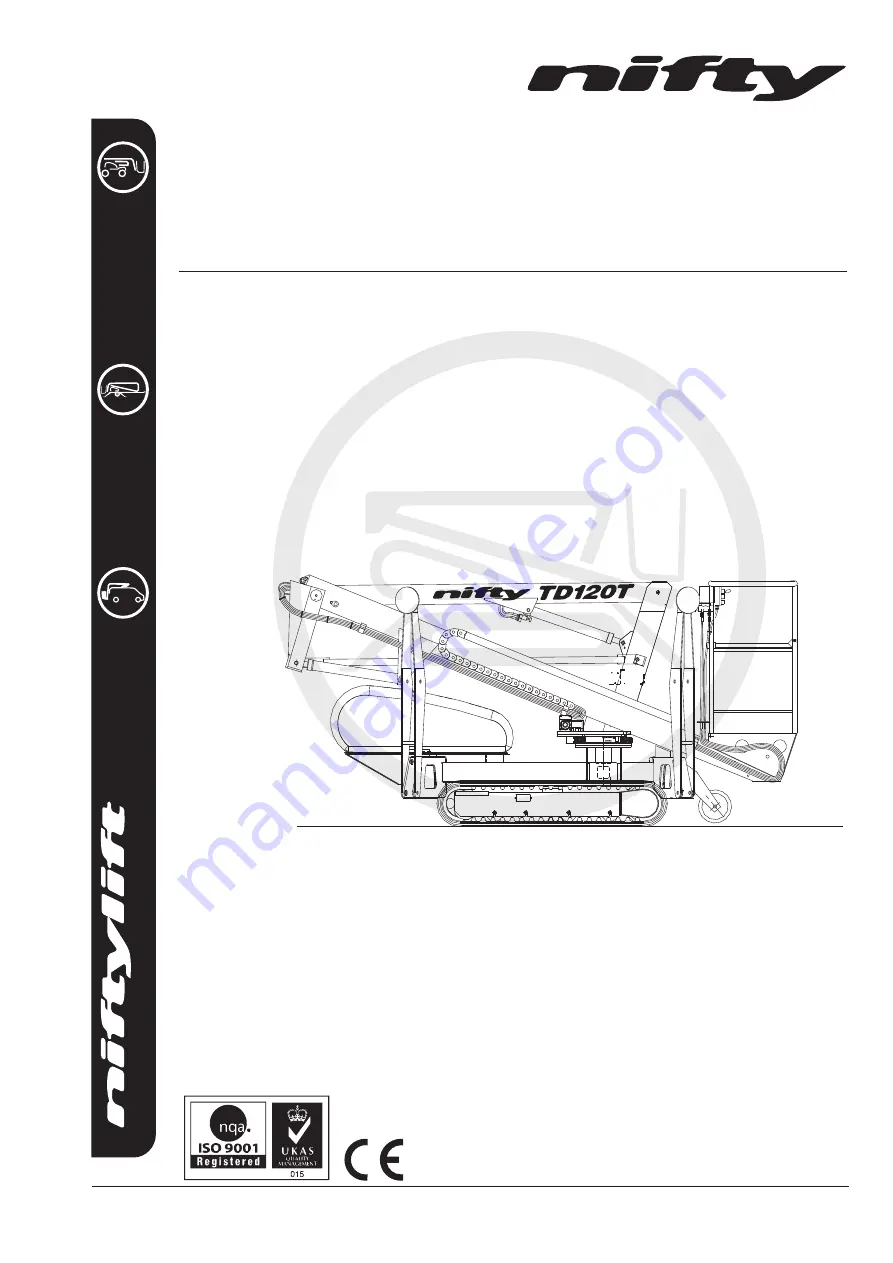
in
fo
@
n
if
ty
li
ft
.c
o
m
.com
Track
Drive
Operating & Safety Instructions
MODEL TD120T/TD34T SERIES
Manufactured by:
Niftylift Limited
Chalkdell Drive
Shenley Wood
Milton Keynes
MK5 6GF
England
www.niftylift.com
e-mail: [email protected]
Tel: +44 (0)1908 223456
Fax: +44 (0)1908 312733
M50261/0
6
Summary of Contents for TrackDrive TD120T Series
Page 2: ......
Page 19: ...TrackDrive TD Series Operating Safety Instructions English USA 02 17 17...
Page 55: ......