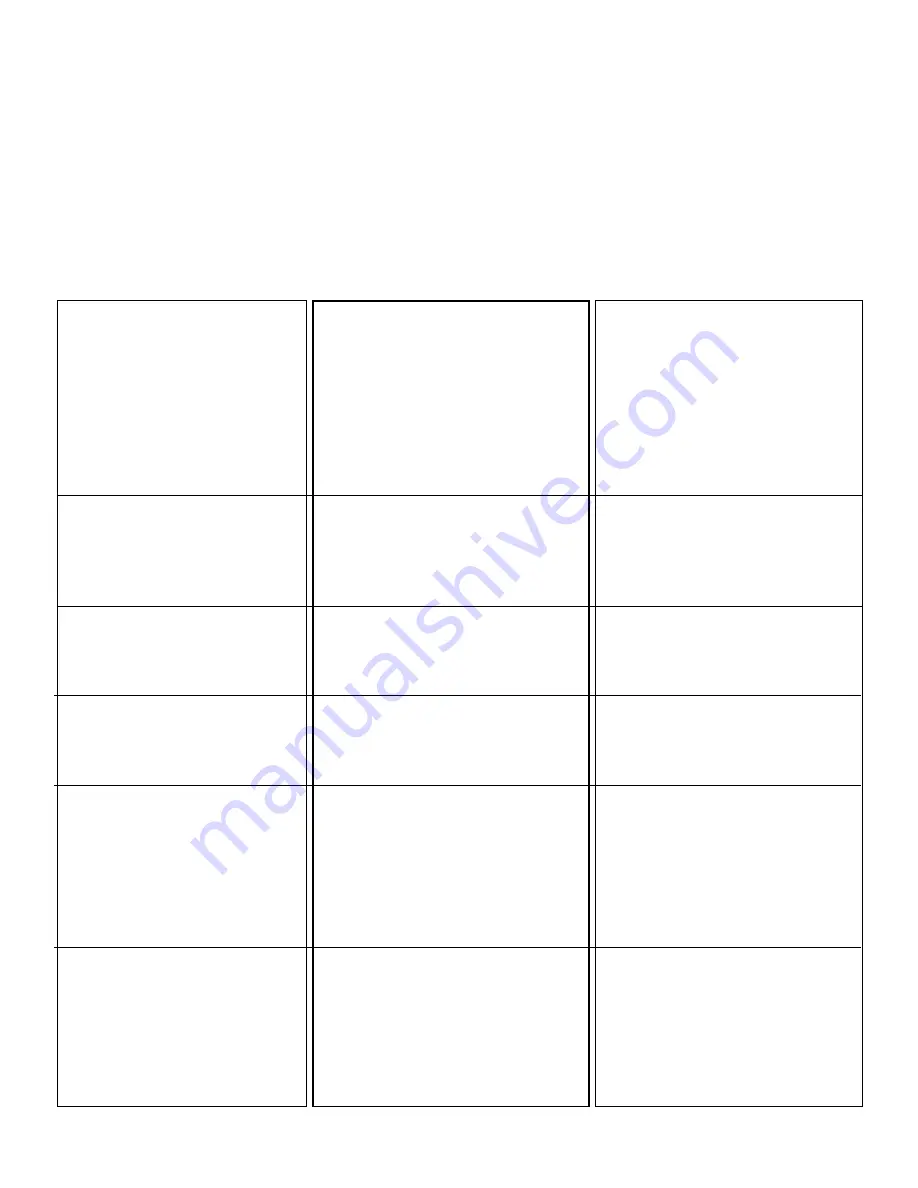
1. Pilot Burners won't light.
2. Pilot burners won't stay lit when
the pushbutton valve is released.
3. Pilot flame weak or yellow.
4. Main burners won't light, or they
go out during operations.
5. Burner(s) appear dim.
6. Burner(s) make popping or
fluttering noise and may go out.
28
H. Troubleshooting Guide
Identify the problem in the left column, then look for probable causes and solutions in the center and right hand columns.
Probable causes are listed in the order of “most likely to happen”. This sequence should be used to isolate the problem.
Once the cause is found refer to the OPERATION or PARTS AND LOCATION sections for further explanation of function
or repair part needed.
1. Pilot burner is dirty or orifice plugged.
2. Pushbutton valve not fully depressed.
3. Main gas supply is not on or not con-
nected properly.
4. Air in pilot line
5. Electric spark is dislocated.
6. Electrical power is not on or not
plugged in.
1. Thermocouple not hot yet.
2. Weak pilot flame.
3. Thermocouple dirty or defective.
4. Blue push button unit defective.
1. Dirty pilot or venturi.
2. Dirty pilot orifice.
3. Pilot line plugged or pinched off.
4. Incoming gas pressure too low.
1. Pilot flame too small.
2. Air draft blowing pilot flame out.
3. Electrical supply interruption.
4. Pilot flame too weak.
1. Orifices dirty.
2. Gas pressure too low.
3. Main gas valve partially closed.
4. Gas line partially blocked.
5. Pressure regulator defective.
6. Burners not installed properly.
7. Burners venturi dirty.
8. Burner mesh dirty.
1. Gas pressure too high.
2. Burners mesh dirty.
3. Orifice or venturi dirty.
1. Clean pilot burner, replace orifice.
2. Repeat starting procedure.
3. Check gas supply.
4. Purge line by holding down blue
push button before igniting.
5. Position electrode so that the tip is
6mm (1/4") from the burner.
6. Plug in / Turn on.
1. Repeat starting procedure.
2. See #3 and #4.
3. Clean or call for authorized Nieco
Service.
4. Call for authorized Nieco Service.
1. Clean.
2. Clean or replace.
3. Call for authorized Nieco Service.
4. Adjust gas pressure on regulator.
1. Replace pilot orifices.
2. Check for drafts.
3. Call for authorized Nieco Service.
4. See #2 and #3 above
1. Clean or replace.
2. Adjust gas pressure on regulator.
3. Open fully.
4. Check line and clear.
5. Call for authorized Nieco Service.
6. Install in the proper location.
7. Clean, see Cleaning Instruction.
8. Clean, see Cleaning Instruction.
1. Adjust gas pressure on regulator.
2. Clean, see Cleaning Instruction.
3. Clean.
continued...
PROBLEM
PROBABLE CAUSES
SOLUTION
Summary of Contents for 624G
Page 16: ...16 G Parts and Location G 1A Models 980 880 Gas Feed End View G 1 Models 980 880 Gas...
Page 17: ...17 G 1C Models 980 880 Gas Left Side View G 1B Models 980 880 Gas Right Side View...
Page 18: ...18 G 2A Models 950 824 Gas Feed End View G 2 Models 950 824 Gas...
Page 19: ...19 G 2B Models 950 824 Gas Right Side View G 2C Models 950 824 Gas Left Side View...
Page 20: ...20 G 3A Models 930 624 Gas Feed End View G 3 Models 930 624 Gas...
Page 21: ...21 G 3C Models 930 624 Gas Left Side View G 3B Models 930 624 Gas Right Side View...
Page 22: ...22 G 4A Model 885 Gas Feed End View G 4 Model 885 Gas...
Page 23: ...23 G 4B Model 885 Gas Right Side View G 4C Model 885 Gas Left Side View...
Page 24: ...24 G 5A Model 850 Gas Feed End View G 5 Model 850 Gas...
Page 25: ...25 G 5C Model 850 Gas Left Side View G 5B Model 850 Gas Right Side View...
Page 26: ...26 G 6A Model 650 Gas Feed End View G 6 Model 650 Gas...
Page 27: ...27 G 6B Model 650 Gas Right Side View G 6C Model 650 Gas Left Side View...