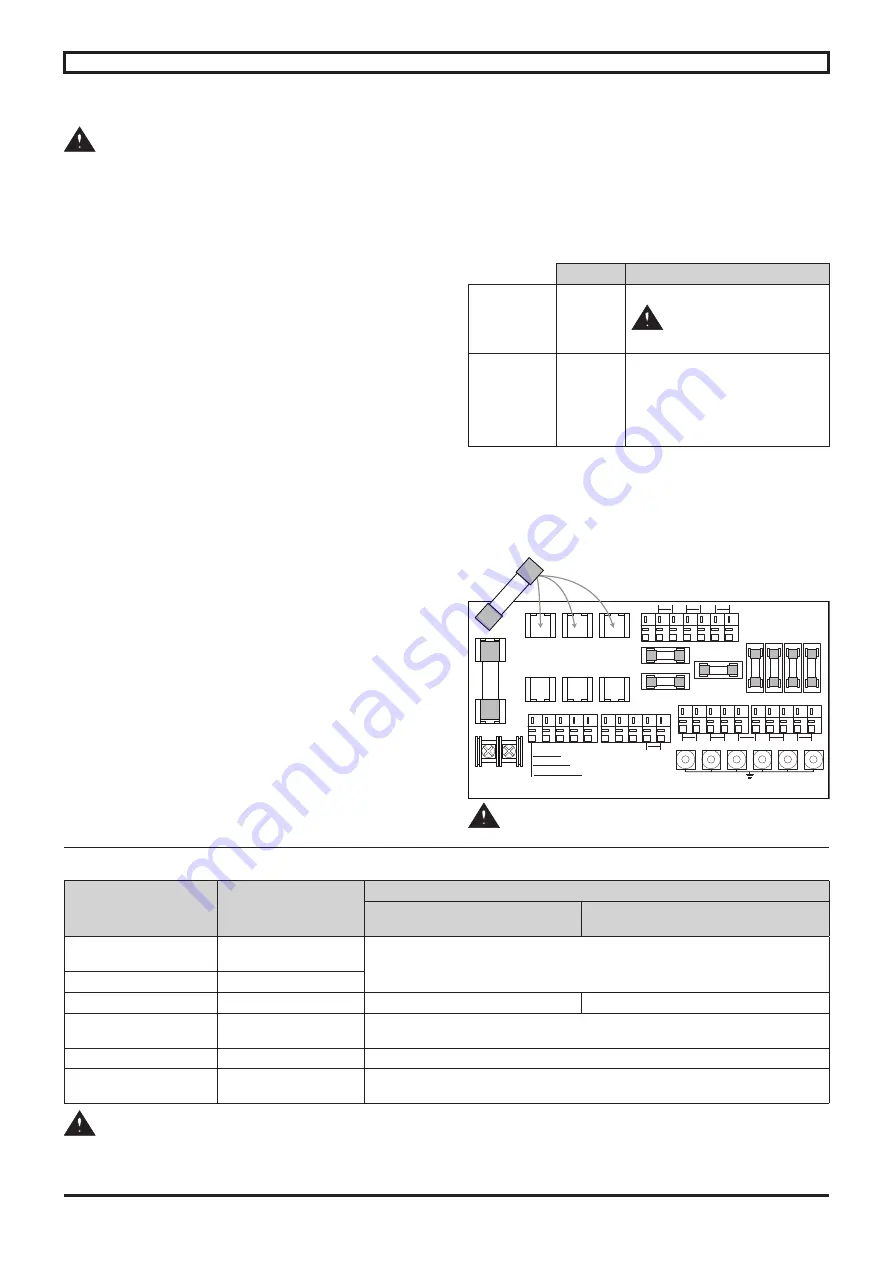
19
CONNECTIONS
Powerdrive MD2SL Installation and maintenance
5077 - 2017.12 / b
en
3 - CONNECTIONS
• All connections work must be performed by
qualified electricians in accordance with the laws in
force in the country in which the drive is installed. This
includes earthing to ensure that no directly accessible
part of the drive can be at the mains voltage or any other
voltage which may be dangerous.
• The drive must be supplied through an approved
circuit-breaking device so that it can be powered down
safely.
• The optional isolator supplied with the drive does
not isolate the drive input busbars. It must without
fail be associated with a circuit-breaking device in the
switchboard.
• The drive power supply must be protected against
overloads and short-circuits.
• Check that the voltage and current of the drive. the
motor and the mains supply are compatible.
• The voltages on the connections of the mains supply.
the motor. the braking resistor or the filter may cause
fatal electric shocks. The protective plates supplied with
the drive must always be installed correctly to protect the
user against electric shocks.
• Only one permanent magnet motor can be connected
to the drive output. It is recommended to install a circuit-
breaking device between the permanent magnet motor
and the drive output to eliminate the risk of hazardous
voltage feedback when performing maintenance work.
• See also the recommendations in section 7.
3.1 - Power Terminals
3.1.1 - Overview
Powerdrive MD2SL power connections are detailed for each
model in §3.1.4.
3.1.2 - Terminal sizes and torque settings
Functions/connections
Refs.
Type of connection and tightening torque
180T to 270T
340T to 1700T
340TH to 1800TH
Mains power supply
L1. L2. L3. or R. S. T
See §3.1.4
M10 screw bolt - 20 Nm / 15 lb.ft
Motor outputs
U. V. w
See §3.1.4
Earth
PE
See §3.1.4
M10 bolt - 20 Nm / 15 lb.ft
M8 bolts - 12 Nm / 9 lb.ft
Braking resistor (1)
BR1. BR2. PE
See §3.1.4
M8 screw bolt - 12 Nm / 9 lb.ft
EMC commoning link
P4. P5
see §4.4.3
Torx screws Ø20 - 4 Nm / 3 lb.ft
Optional external
emergency stop
X1-1. X1-2
Do not exceed the indicated maximum tightening torque.
(1) If braking transistor is fitted.
3.1.3 - Electronics and forced ventilation
power supply
The control electronics and forced ventilation units are
supplied through a single-phase transformer which primary
is connected to terminals L1-L2 of the power supply. If
necessary. this transformer can be supplied with an external
power source (PX4 terminal block on fuse board).
3.1.3.1 - Electrical characteristics:
Voltage
Maximum power
Secondary 1
(Electronics
power supply)
230 V
isolated
100 VA
The neutral of the
electronics power
supply not connected to earth
Secondary 2
(Forced
ventilation and
auxiliaries power
supply)
230 V
connected
to earth
180T to 570T : P = 200 VA
750T to 1100T : P = 400 VA
1400T to 1700T : P = 600 VA
400TH to 600TH : P = 200 VA
750TH to 1200TH : P = 400 VA
1500TH to 1800TH: P = 600 VA
3.1.3.2 - Fuse boards
Depending on the rating.
Powerdrive MD2SL
may include
one or more identical fuses board:
- 180T to 570T & 340TH to 600TH : 1 board
- 750T to 1100T & 750TH to 1200TH : 2 boards
- 1400T to 1700T 1500TH to 1800TH : 3 boards
F1
F2
F3 F4 F5 F6
F9
F7
PX4
460V(T)
600V(TH)
480V(T)
690V(TH)
400V(T)
500V(TH)
P1
F8
400V(T) / 500V(TH)
460V(T) / 600V(TH)
480V (T) / 690V (TH)
P2
P3
P4
P6
P7 P8
Interface
board
output
Power
Input S1
Power
Input S2
External
power input
Fan
Control
Fan1
Fan2
Fan3
Fan4
Fan5
Position the F8 fuse according to the mains supply
voltage