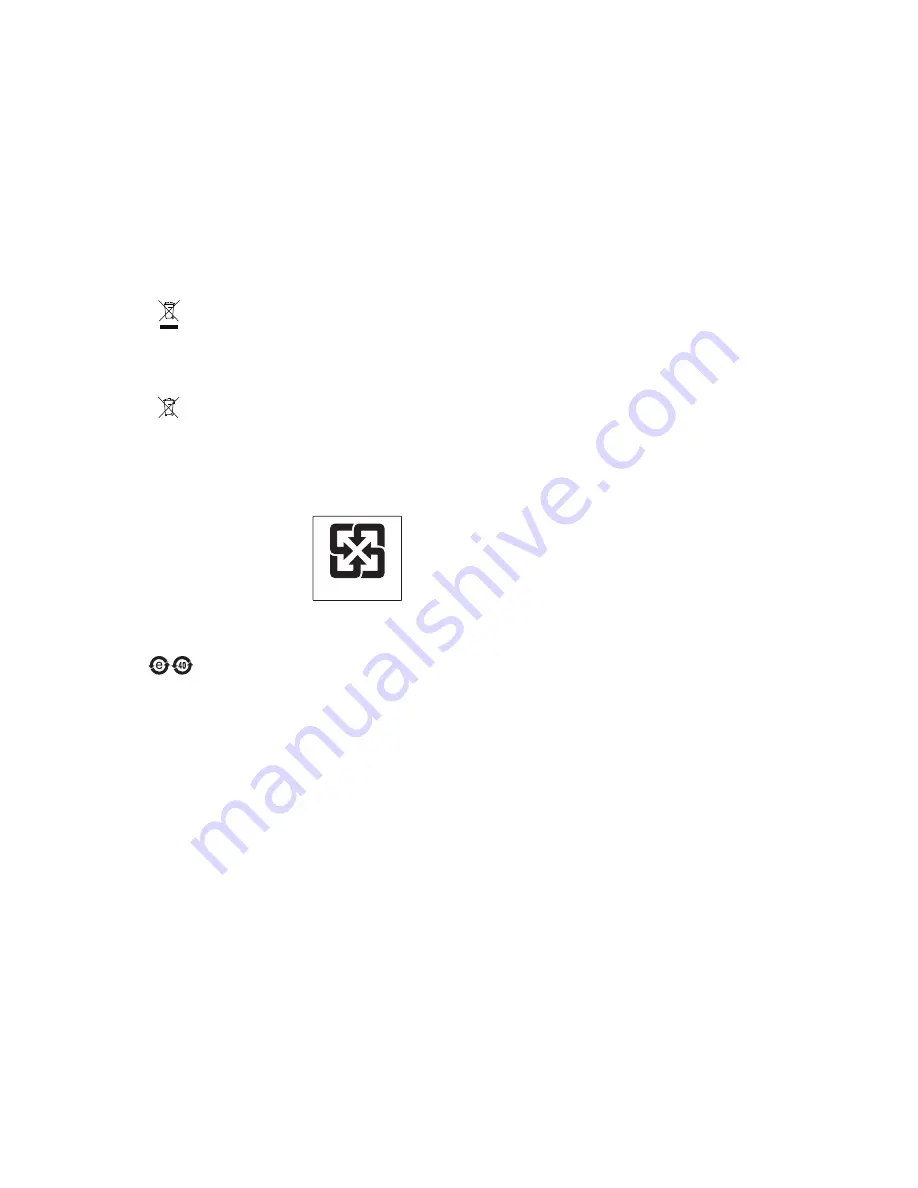
NI WSN-3214 User Guide and Specifications
52
ni.com
Environmental Management
NI is committed to designing and manufacturing products in an environmentally responsible manner.
NI recognizes that eliminating certain hazardous substances from our products is beneficial to the
environment and to NI customers.
For additional environmental information, refer to the
NI and the Environment
Web page at
ni.com/
environment
. This page contains the environmental regulations and directives with which NI
complies, as well as other environmental information not included in this document.
Waste Electrical and Electronic Equipment (WEEE)
EU Customers
At the end of the product life cycle, all products
must
be sent to a WEEE recycling
center. For more information about WEEE recycling centers, National Instruments WEEE initiatives,
and compliance with WEEE Directive 2002/96/EC on Waste and Electronic Equipment, visit
ni.com/environment/weee
.
Battery Replacement and Disposal
Battery Directive
After replacement, recycle the old battery. For information about the available
collection and recycling scheme (and your nearest National Instruments Branch Office) or on Battery
Directive compliance (Directive 2006/66/EC of the European Parliament and Council) in a particular
EU country visit
ni.com/company/citizenship/product.htm#battery
.
Taiwan R.O.C.
Cd/Hg/P
b
廢電池請回收
⬉ᄤֵᙃѻક∵ᶧࠊㅵ⧚ࡲ⊩ ˄Ё
RoHS
˅
Ёᅶ᠋
National Instruments
ヺড়Ё⬉ᄤֵᙃѻકЁ䰤ࠊՓ⫼ᶤѯ᳝ᆇ⠽䋼ᣛҸ
(RoHS)
DŽ
݇Ѣ
National Instruments
Ё
RoHS
ড়㾘ᗻֵᙃˈ䇋ⱏᔩ
ni.com/environment/rohs_china
DŽ
(For information about China RoHS compliance, go to
ni.com/environment/rohs_china
.)