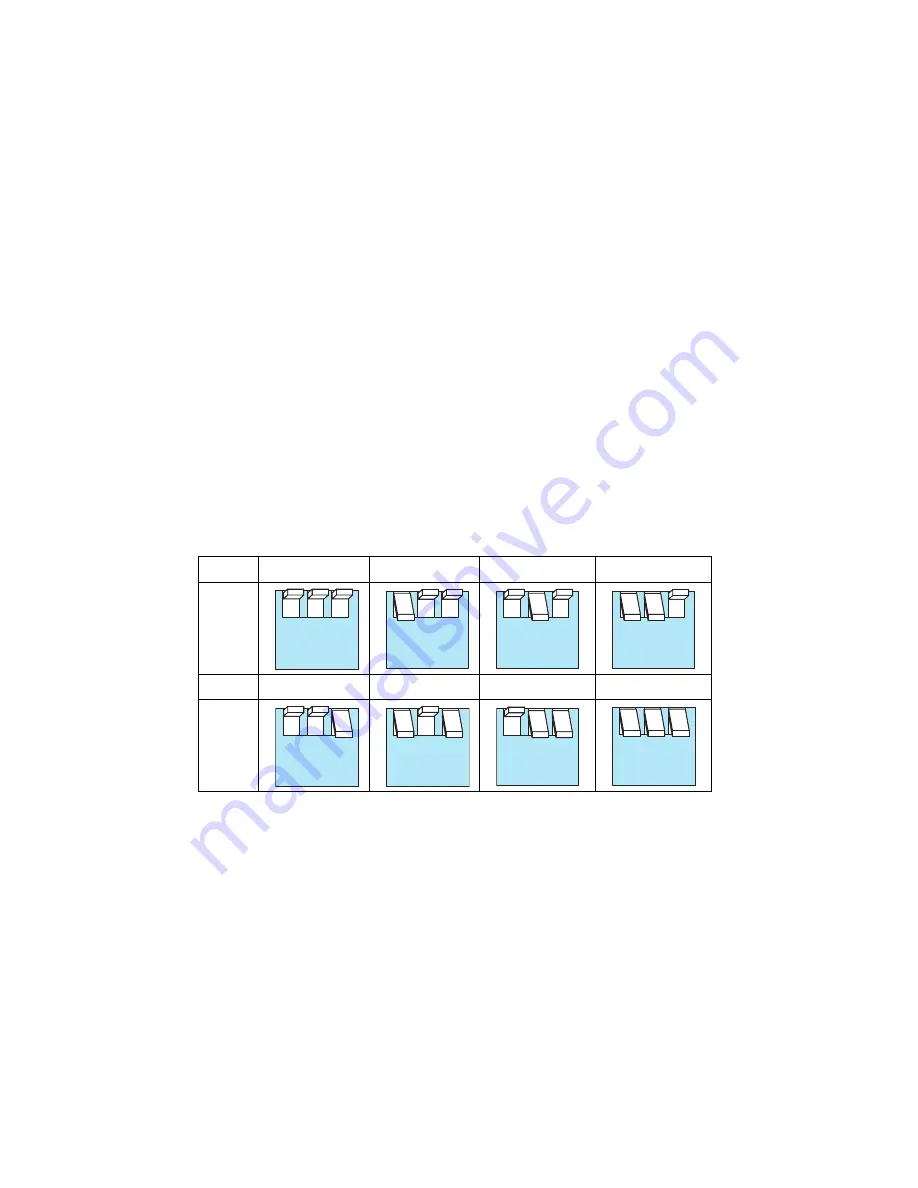
1
8
|
ni.com
|
NI SMD-7611/7612 User Manual
Step 5: Step Size
The SMD-7611/7612 requires a source of step pulses to command motion. This may be a PLC,
an indexer, a motion controller or another type of device. The only requirement is that the device
be able to produce step pulses whose frequency is in proportion to the desired motor speed, and
be able to smoothly ramp the step speed up and down to produce smooth motor acceleration and
deceleration.
Smaller step sizes result in smoother motion and more precise speed, but also require a higher
step pulse frequency to achieve maximum speed. The smallest step size of the SMD-7611/7612
is 1/20,000th of a motor turn. To command a motor speed of 50 revolutions per second
(3000 rpm) the step pulses frequency must be 50 × 20,000 = 1 MHz. Six different settings are
provided in the SMD-7611/7612 drive, as shown in Table 8. Choose the one that best matches
the capability of your system.
At lower step resolutions such as 200 steps/rev (full step) and 400 steps/rev (half step), motors
run a little rough and produce more audible noise than when they are microstepped
(2000 steps/rev and beyond). The SMD-7611/7612 drives include a feature called microstep
emulation, or step smoothing, that can provide smooth motion when using full or half steps. By
selecting 200 smooth or 400 smooth, this feature is automatically employed to provide the
smoothest possible motion when using full or half stepping.
Because a command filter is used as part of the step smoothing process, there will be a slight
delay in the motion. If this delay is unsuitable for your application, please choose the non-filtered
setting 200 or 400. The following figure shows an example of the delay that can occur from using
the step smoothing filter.
Table 8.
Configuring Step Size on Switches 5, 6, and 7
Step/rev
20000
12800
5000
2000
Switch
position
Step/rev
400 Smooth
400
200 Smooth
200
Switch
position
5 6 7
5 6 7
5 6 7
5 6 7
5 6 7
5 6 7
5 6 7
5 6 7