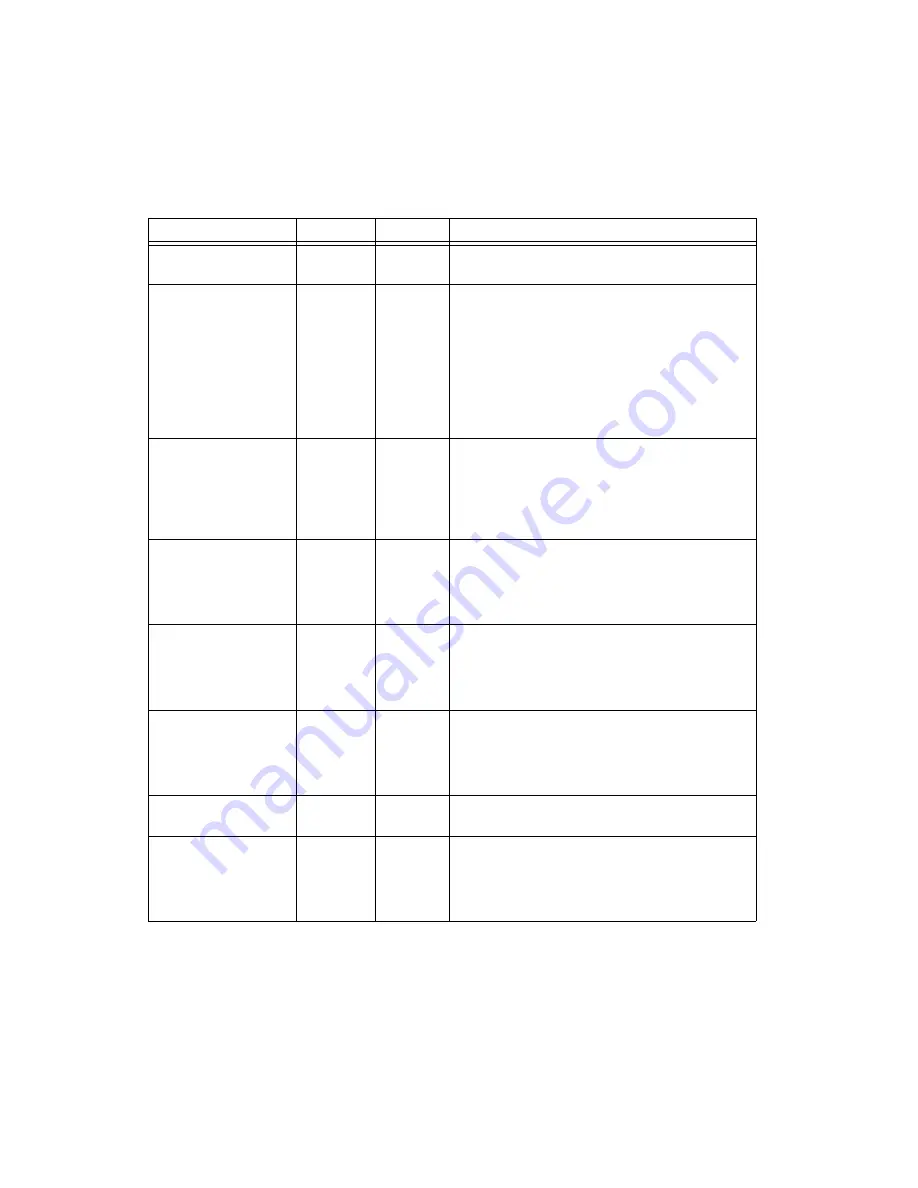
Chapter 3
Connecting the Signals
DAQPad-MIO-16XE-50 User Manual
3-4
ni.com
EXTSTROBE*
DGND
Output
External Strobe—This output can be toggled under software
control to latch signals or trigger events on external devices.
PF10/TRIG1
DGND
Input
Output
PF10/Trigger1—As an input, this is one of the
Programmable Function Inputs (PFIs). PFI signals are
explained in the
section later in this
chapter.
As an output, this is the TRIG1 signal. In posttrigger DAQ
sequences, a low-to-high transition indicates the initiation
of the acquisition sequence. In pretrigger applications, a
low-to-high transition indicates the initiation of the
pretrigger conversions.
PFI1/TRIG2
DGND
Input
Output
PFI1/Trigger2—As an input, this is one of the PFIs.
As an output, this is the TRIG2 signal. In pretrigger
applications, a low-to-high transition indicates the initiation
of the posttrigger conversions. TRIG2 is not used in
posttrigger applications.
PFI2/CONVERT*
DGND
Input
Output
PFI2/Convert—As an input, this is one of the PFIs.
As an output, this is the CONVERT* signal. A high-to-low
edge on CONVERT* indicates that an A/D conversion is
occurring.
PFI3/GPCTR1_SOURCE
DGND
Input
Output
PFI3/Counter 1 Source—As an input, this is one of the PFIs.
As an output, this is the GPCTR1_SOURCE signal.
This signal reflects the actual source connected to the
general-purpose counter 1.
PFI4/GPCTR1_GATE
DGND
Input
Output
PFI4/Counter 1 Gate—As an input, this is one of the PFIs.
As an output, this is the GPCTR1_GATE signal. This signal
reflects the actual gate signal connected to the
general-purpose counter 1.
GPCTR1_OUT
DGND
Output
Counter 1 Output—This output is from the general-purpose
counter 1 output.
PFI5/UPDATE*
DGND
Input
Output
PFI5/Update—As an input, this is one of the PFIs.
As an output, this is the UPDATE* signal. A high-to-low
edge on UPDATE* indicates that the AO primary group is
being updated.
Table 3-1.
DAQPad-TB-52 Signal Descriptions (Continued)
Signal Name
Reference
Direction
Description