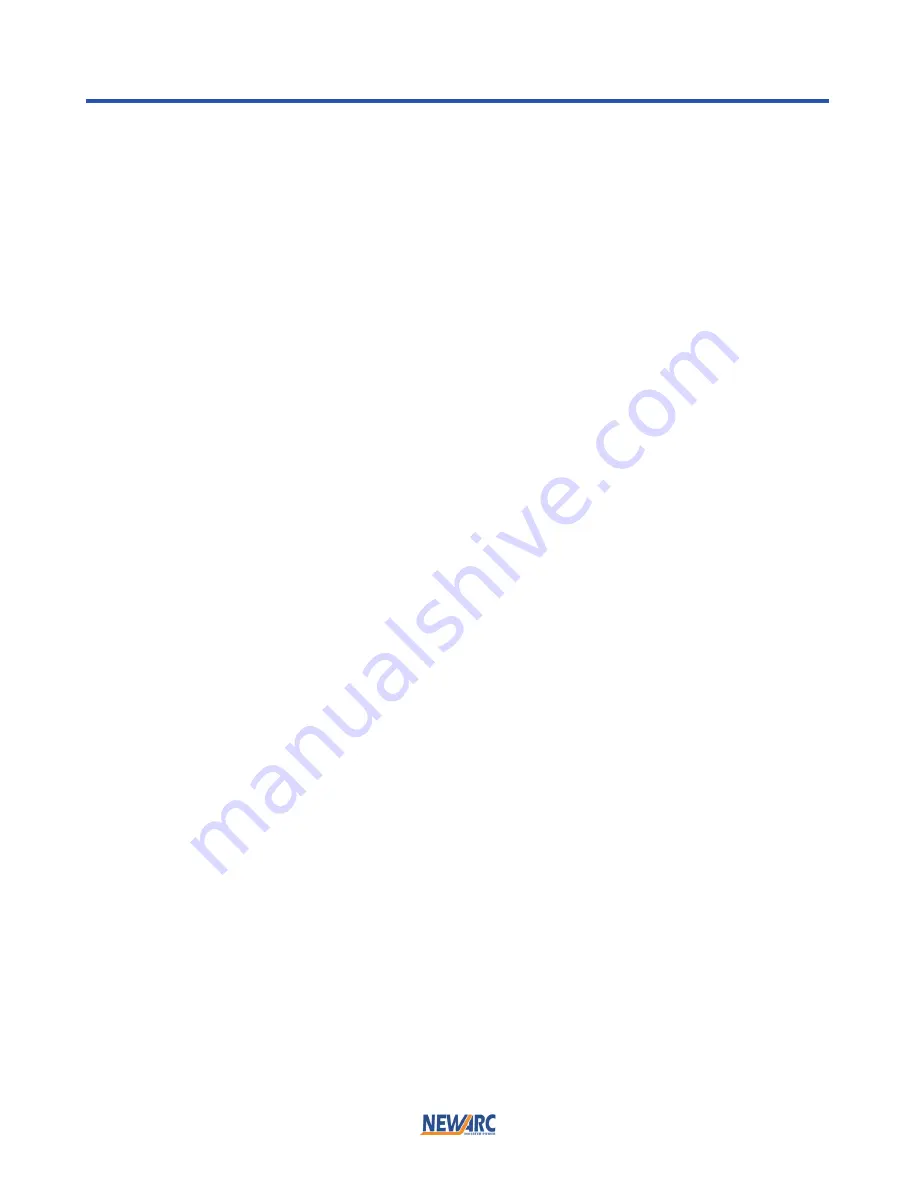
RT2500
4
Fire and Explosions
Pay attention to fire and safety regulations in force at the
welding site.
•
Remove all flammable or combustible materials from
the welding area and the immediate vicinity.
•
Suitable fire fighting equipment must always be present
where welding is carried out.
•
Be aware that a fire risk is present for a considerable
time after welding operations have ceased because
of sparks and hot slag etc. Take suitable precautions
when you have finished welding.
•
Take care when welding containers that have held
flammable or combustible material, these should have
been specially cleaned before being given to the
welder. If in doubt do not weld them.
Burns
Be aware that burns may be the result of the heat involved
in the welding process, welding spatter or the Ultra Violet
Radiation given off by the arc itself.
•
Wear suitable fireproof clothing over all your body.
•
Wear protective gauntlets designed for welding use.
•
Wear a welding facemask fitted with the correct filter
shade suitable for the current at which you will be
welding.
•
Avoid wearing oily or greasy clothing as a spark may
ignite them. Where possible ensure that a suitable first
aid kit and a first aid person qualified in the treatment
of burns are available nearby.
Fumes
Welding operations give off harmful fumes that are haz-
ardous to your health.
•
Make sure the welding area is well ventilated. Use suit-
able fume extractors or exhaust fans if necessary.
•
If the ventilation is not suitable then breathing appara-
tus may have to be used.
•
Do not weld plated metals or metals which contain
Lead, cadmium, Zinc, Mercury or Beryllium unless you
are wearing suitable breathing apparatus.
Electric Shock
•
Do not touch live electrical parts.
•
Do not work in wet or excessively humid areas and do
not site the RT2500 on a wet surface.
•
Avoid touching the work piece whilst welding.
•
Do not use the RT2500 without it’s protective
cover.
•
Keep your clothing and body dry.
The safe handling of gas cylinders
The RT2500 uses argon when TIG welding. This is an inert
gases and can displace oxygen in the atmosphere lead-
ing to asphyxiation.
•
Note!
If dropped the gas cylinder may explode.
•
Check the gas cylinder, pressure regulator and gas
hoses regularly for leaks and discard any suspect item.
•
Do not try to directly connect a gas cylinder to the
RT2500 without using a pressure-reducing regulator
designed for use with argon.
•
Do not use gas cylinders whose of contents you are
unsure.
•
The Argon cylinder must be securely fastened to a
wall or placed in a specially designed cylinder carrier.
•
Always turn off the valve on the gas cylinder when you
have finished welding.
•
Always install and use pressure regulators in accor-
dance with the manufacturers instructions.
•
It is advisable, when attaching the regulator to the gas
bottle, to briefly turn on the bottle valve to expel any
foreign objects that may be present. These may later
block the solenoid valve of the machine if not dealt
with. Turn your face away from the bottle valve when
carrying out this action.
Further information is available in publication HSG118
'The safe use of compressed gases in welding, flame
cutting and allied processes', which may be ob-
tained from the Health & Safety Executive.
Welding and earth return cables
•
Earth return and electrode holder cables must have a
cross sectional area of at least 35mm
2
.
•
Only use copper cables, the use of Aluminium cables
may have a detrimental effect on the performance of
the machine.
•
Regularly inspect welding cables and connectors for
wear abrasion and corrosion. Corroded cables and
connectors may overheat and become a fire hazard.
•
Ensure that all welding connectors are fully mated, the
connectors should be pushed fully home and then
turned clockwise to lock. If the connectors are not
mated fully they may overheat and become a fire
hazard.
•
If possible, fasten the earth return clamp directly to the
job to be welded and ensure that the surface is free
from rust and paint.
SECTION 1 — SAFETY
Summary of Contents for rt2500
Page 2: ......
Page 9: ...RT2500 9 6 1 Parts Locations SECTION 6 PARTS BREAKDOWN 34...
Page 11: ......