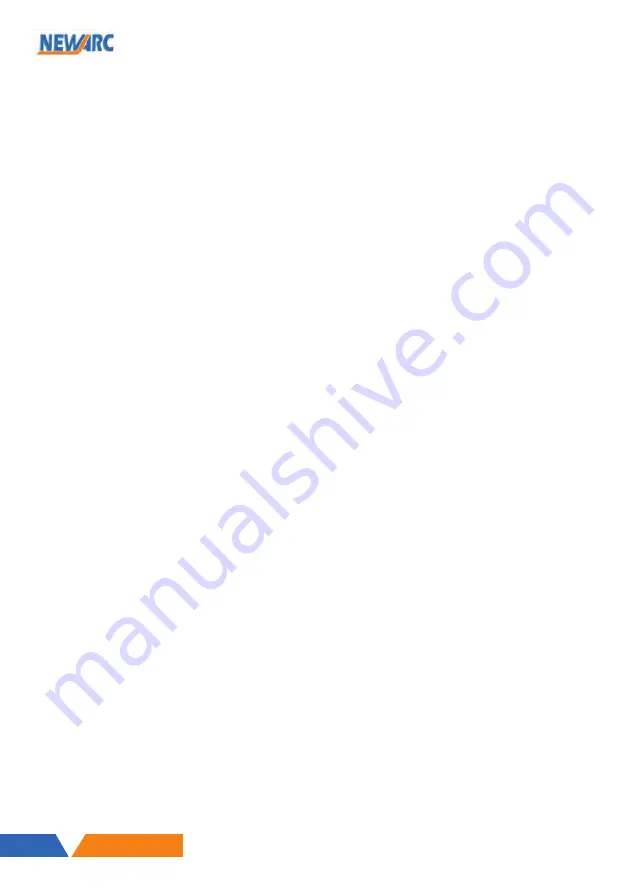
Wear suitable protective flame resistant clothing. The sparks and spatter from welding, hot work pieces,
and hot equipment can cause fires and burns. Welding on closed containers, such as tanks, drums, or
pipes, can cause them to explode. Accidental contact of electrode to metal objects can cause arcs,
explosion, overheating, or fire. Check and be sure the area is safe and clear of inflammable material
before carrying out any welding.
Protection against noise
Some welding and cutting operations may produce noise. Wear safety ear protection to protect your
hearing.
Protection from moving parts
When the machine is in operation, keep away from moving parts such as motors and fans. Moving
parts, such as the fan, may cut fingers and hands and snag garments. Protections and coverings may
be removed for maintenance and controls only by qualified personnel, after first disconnecting the
power supply cable. Replace the coverings and protections and close all doors when the intervention
is finished, and before starting the equipment. Take care to avoid getting fingers trapped when loading
and feeding wire during set up and operation. When feeding wire be careful to avoid pointing it at other
people or toward your body. Always ensure machine covers and protective devices are in operation.
Precautions against fire and explosion
Avoid causing fires due to sparks and hot waste or molten metal. Ensure that appropriate fire safety
devices are available near the cutting / welding area. Remove all flammable and combustible materials
from the cutting / welding zone and surrounding areas. Do not cut/weld fuel and lubricant containers,
even if empty. These must be carefully cleaned before they can be cut/welded. Always allow the cut/
welded material to cool before touching it or placing it in contact with combustible or flammable
material. Do not work in atmospheres with high concentrations of combustible fumes, flammable gases
and dust. Always check the work area half an hour after cutting to make sure that no fires have begun.
Risks due to magnetic fields
The magnetic fields created by high currents may affect the operation of pacemakers or electronically
controlled medical equipment. Wearers of vital electronic equipment should consult their physician
before beginning any arc welding, cutting, gouging or spot welding operations. Do not go near welding
equipment with any sensitive electronic equipment as the magnetic fields may cause damage.
RF Declaration
Equipment that complies with directive 2004/108/EC concerning electromagnetic compatibility (EMC)
and the technical requirements of EN60974-10 is designed for use in industrial buildings and not those
for domestic use where electricity is provided via the low voltage public distribution system. Difficulties
may arise in assuring class A electromagnetic compatibility for systems installed in domestic locations
due to conducted and radiated emissions. In the case of electromagnetic problems, it is the
responsibility of the user to resolve the situation. It may be necessary to shield the equipment and fit
suitable filters on the mains supply.
4
R4000CC
Summary of Contents for NewArc R4000CC
Page 19: ...19 8 Parts R4000CC...
Page 23: ...Notes 23 R4000CC...