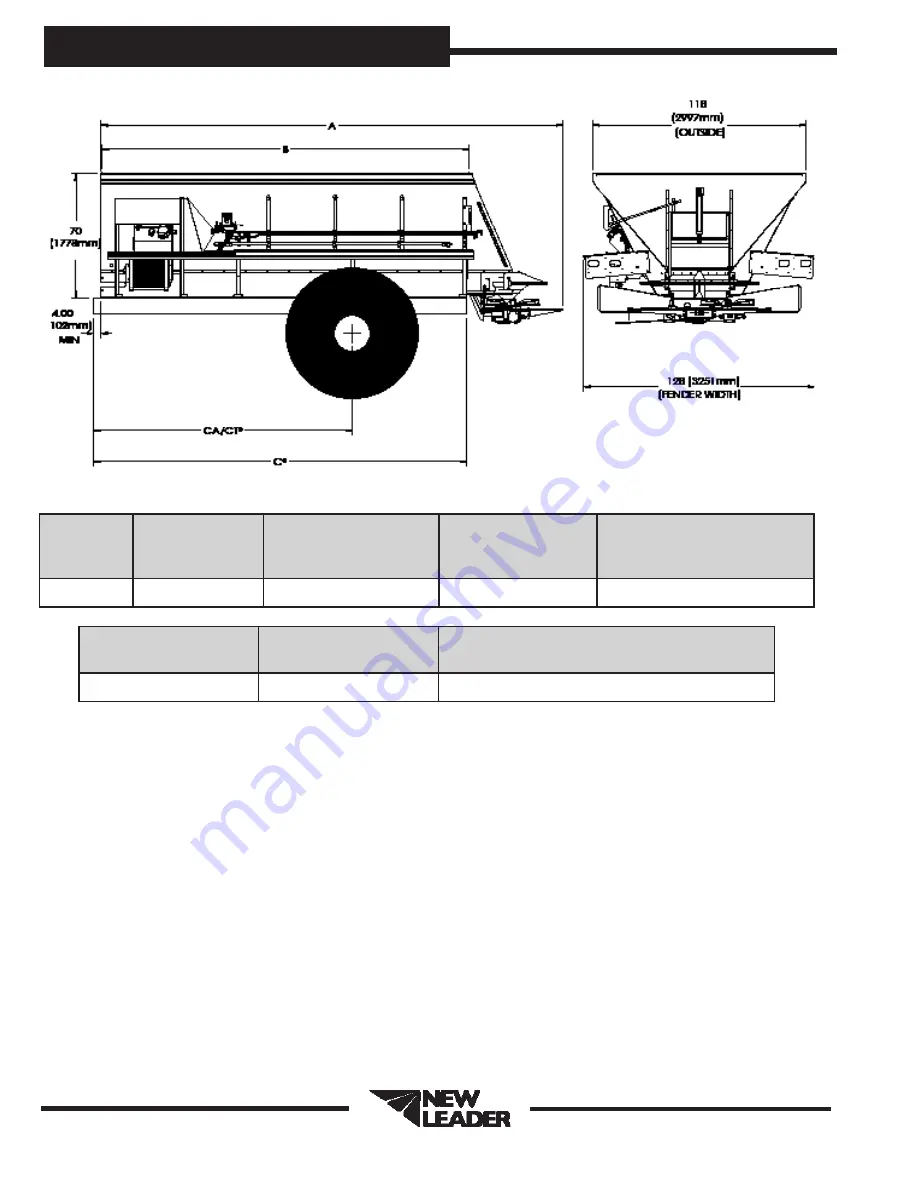
- 26 -
www.NewLeader.com
(800) 363-1771
306375-AA-E
L5034G4 AGCO
Dimensions & Capacities
Unit
Length
Overall Lenth
A
Body Length
B
Frame Length
C
Cab to Axle or Cab to
Tandem
CA/CT
14’
208” (5283mm)
156” (3962mm)
159” (4039mm)
114” (2896mm) CA
Unit Length
Struck Capacity
Cu Ft (Cu M)
Approximate Weight
Pounds (kilograms)
14’ (4�27 m)
392 (11�1)
5600 (2540)