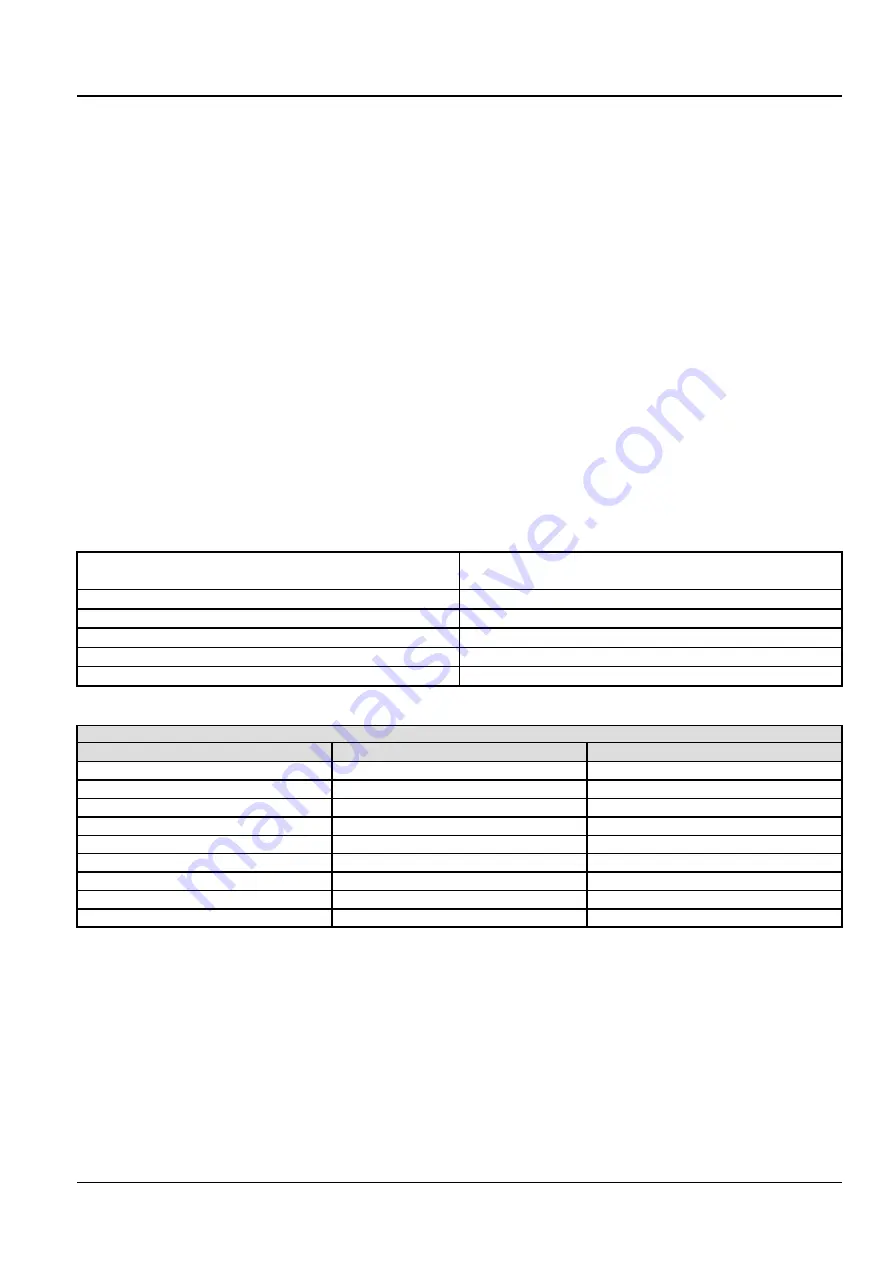
INTRODUCTION
Hydraulic Hoses and Tubes
NOTE: Tightening the joint to the proper torque will keep it leak free, and prevent it from damaging the hose or fitting.
Always replace hoses and tubes with damaged cone ends or the end connections.
When installing a new hose, loosely connect each end and make sure the hose fits its desired location, without kinking
or twisting, before tightening the connection. Tighten non-swivel end of hose first if applicable. Tighten the hose
clamps enough to hold the hose without chafing but not so tight as to crush the ends.
Keep the hoses and tubes clear of moving parts and replace any hoses and fittings that have moved from their original
positions over time. A hose with a chafed outer cover will allow moisture to get into the system. Concealed corrosion
of the wire reinforcement will then occur along the hose length and result in hose failure.
Ballooning of the hose indicates internal leakage as the hose deteriorates. This condition can rapidly lead to hose
failure.
Kinked, crushed, stretched or damaged hoses generally suffer internal structural damage that restricts fluid flow, re-
duces performance and ultimately causes the hose to fail.
Do not allow free moving, unsupported hoses or tubes to touch each other or related working surfaces. This causes
chafing and reduces line life.
National Pipe Thread (NPT) Fittings
Before installing and tightening pipe fittings, clean the threads with a cleaning solvent or Loctite® brand cleaner. Apply
the appropriate Loctite® brand sealant to all fittings including stainless steel, unless as otherwise stated. Generally
Loctite® 567™ can be used for all fittings including stainless steel. Loctite® 565™ is used for most metal fittings. For
high filtration/zero contamination systems use Loctite® 545™.
NPT PIPE FITTING TORQUE CHART
Thread Size
Torque (Maximum)
1/8" - 27
13 Nm
(
10 lb ft
)
1/4" - 18
16 Nm
(
12 lb ft
)
3/8" - 18
22 Nm
(
16 lb ft
)
1/2" - 14
41 Nm
(
30 lb ft
)
3/4" - 14
54 Nm
(
40 lb ft
)
PIPE FITTING
Nom. SAE Dash Size
Thread Size
TFFT (Turns For Finger Tight)
-2
1/8 - 27
2.0 - 3.0
-4
1/4 - 18
2.0 - 3.0
-6
3/8 - 18
1.5 - 3.0
-8
1/2-14
2.0 - 3.0
-12
3/4 - 14
2.0 - 3.0
-16
1 - 11-1/2
1.5 - 2.5
-20
1-1/4 - 11-1/2
1.5 - 2.5
-24
1-1/2 - 11-1/2
1.5 - 2.5
-32
2 - 11-1/2
1.5 - 2.5
Apply sealant/lubricant to male pipe threads. The first two threads should be left uncovered to avoid system contam-
ination. Screw pipe fitting into female pipe port to the finger tight position. Wrench tighten fitting to the appropriate
turns from finger tight (TFFT) shown in table above, making sure the tube end of an elbow or tee fitting is aligned to
receive incoming tube or hose fitting.
Installation of Adjustable Fittings in Straight Thread O Ring Bosses
1. Lubricate the O ring by coating it with light oil or petroleum jelly. Install the O ring in the groove adjacent to the
metal backup washer which is assembled at the extreme end of the groove.
2. Install the fitting into the SAE straight thread boss until the metal backup washer contacts the face of the boss.
NOTE: Do not over tighten and distort the metal backup washer.
3. Position the fitting by turning out (counter clockwise) up to a maximum of one turn. Holding the pad of the fitting
with a wrench, tighten the locknut and washer against the face of the boss.
84269855 20/04/2010
15
Summary of Contents for Workmaster 75
Page 1: ...SERVICE MANUAL Workmaster 75 84269855 20 04 2010 ...
Page 4: ...84269855 20 04 2010 Find manuals at https best manuals com ...
Page 5: ...INTRODUCTION 84269855 20 04 2010 1 Find manuals at https best manuals com ...
Page 41: ...This as a preview PDF file from best manuals com Download full PDF manual at best manuals com ...