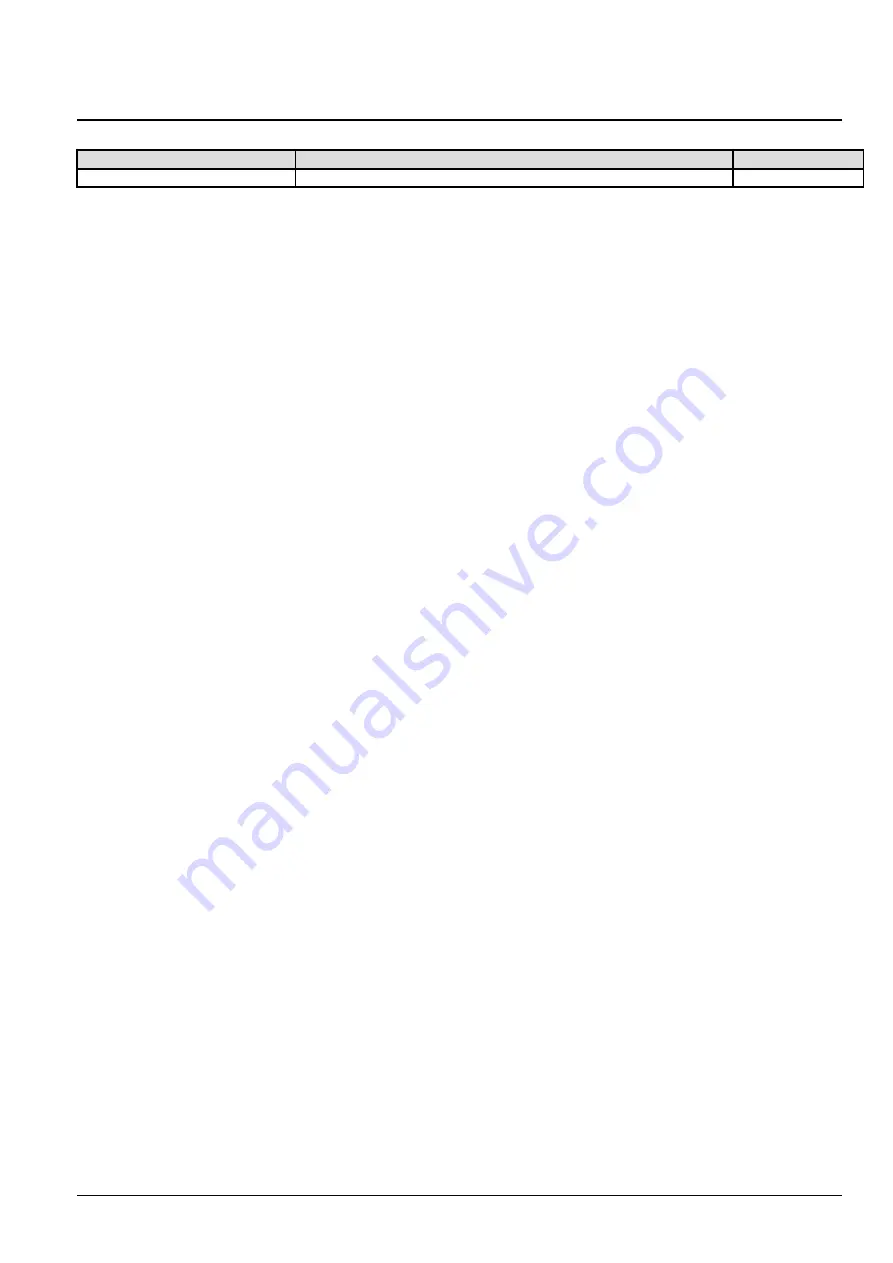
CONSUMABLES INDEX
Consumable
Reference
PAGE
Loctite® 518™
Engine and crankcase - Install
10.1 / 26
51553302 19/11/2018
10.1 [10.001] / 3
Summary of Contents for T3.60F
Page 6: ...INTRODUCTION 51553302 19 11 2018 1 Find manuals at https best manuals com ...
Page 15: ...51553302 19 11 2018 10 ...
Page 16: ...SERVICE MANUAL Engine T3 60F T3 70F T3 80F 51553302 19 11 2018 10 ...
Page 17: ...Contents Engine 10 10 001 Engine and crankcase 10 1 51553302 19 11 2018 10 ...
Page 19: ...51553302 19 11 2018 10 ...
Page 20: ...Engine 10 Engine and crankcase 001 T3 60F T3 70F T3 80F 51553302 19 11 2018 10 1 10 001 1 ...
Page 41: ...This as a preview PDF file from best manuals com Download full PDF manual at best manuals com ...