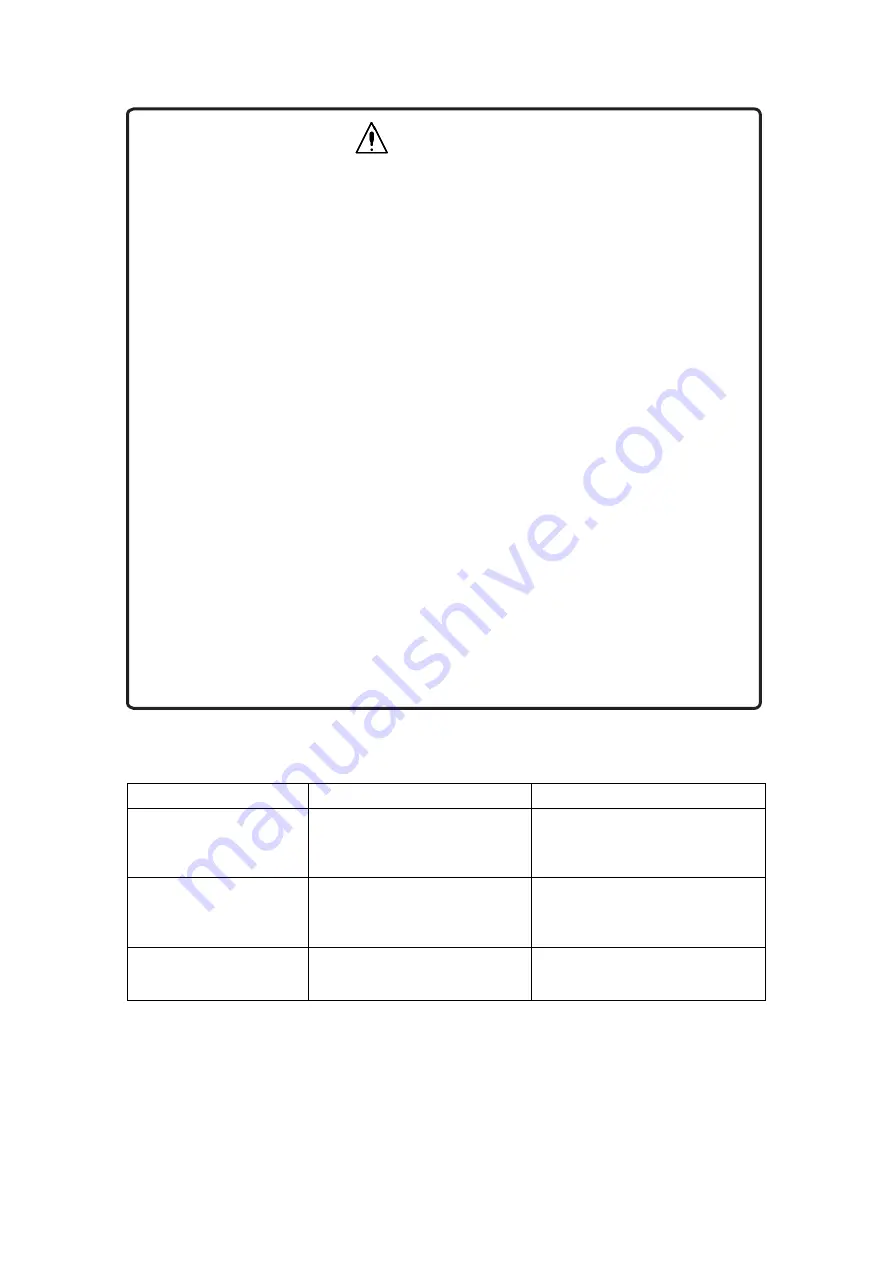
8
Installing Height
Type of gas
Installing height
Remarks
Gas heavier than air
(Example: LPG)
A maximum of 10 cm above the
floor.
(Height to the sensor guard tip)
Keep a space of approximately
7 cm from the sensor guard tip
for ease of maintenance and
inspection.
Gas almost the same as
air in specific gravity
(Example: Carbon
monoxide)
75 to 150 cm above the floor.
(Height to the sensor guard tip)
Decide the height by considering
the specific gravity and mounting
environment.
Gas lighter than air
(Example: City gas and
hydrogen)
Near the ceiling
Decide the height by considering
arrangements for ease of
maintenance (e.g., a scaffold).
CAUTION
Be careful not to damage the gas detector when installing it. Otherwise, the
explosion-proof performance of the gas detector will be lost.
Do not install the product in the following places.
- Places where the ambient temperature exceeds the operating temperature
range (
10
C to 50
C).
- Places where condensation occurs.
- Places where water is directly sprayed.
- Places subject to corrosive gas.
- Places close to equipment that generates high frequencies or a magnetic field.
- Places where silicone sealant is used or likely to be used.
- Places where silicone gas is used or likely to be used.
Install the gas detector in places where it can be maintained and inspected with
ease.
Install the gas detector in places free from vibration.
Install the gas detector in places free from sudden temperature changes.
Keep the gas detector free from impacts.
When installing the gas detector outdoors, be sure to install the protective cover
(optional).
The installing height of the gas detector has an important relation to the specific
gravity of the target gas to be detected. Install the gas detector in accordance
with required regulations.
Install the gas detector in the environment where there is no power outrage
including short interruption
Summary of Contents for KD-12B
Page 43: ...40 ...