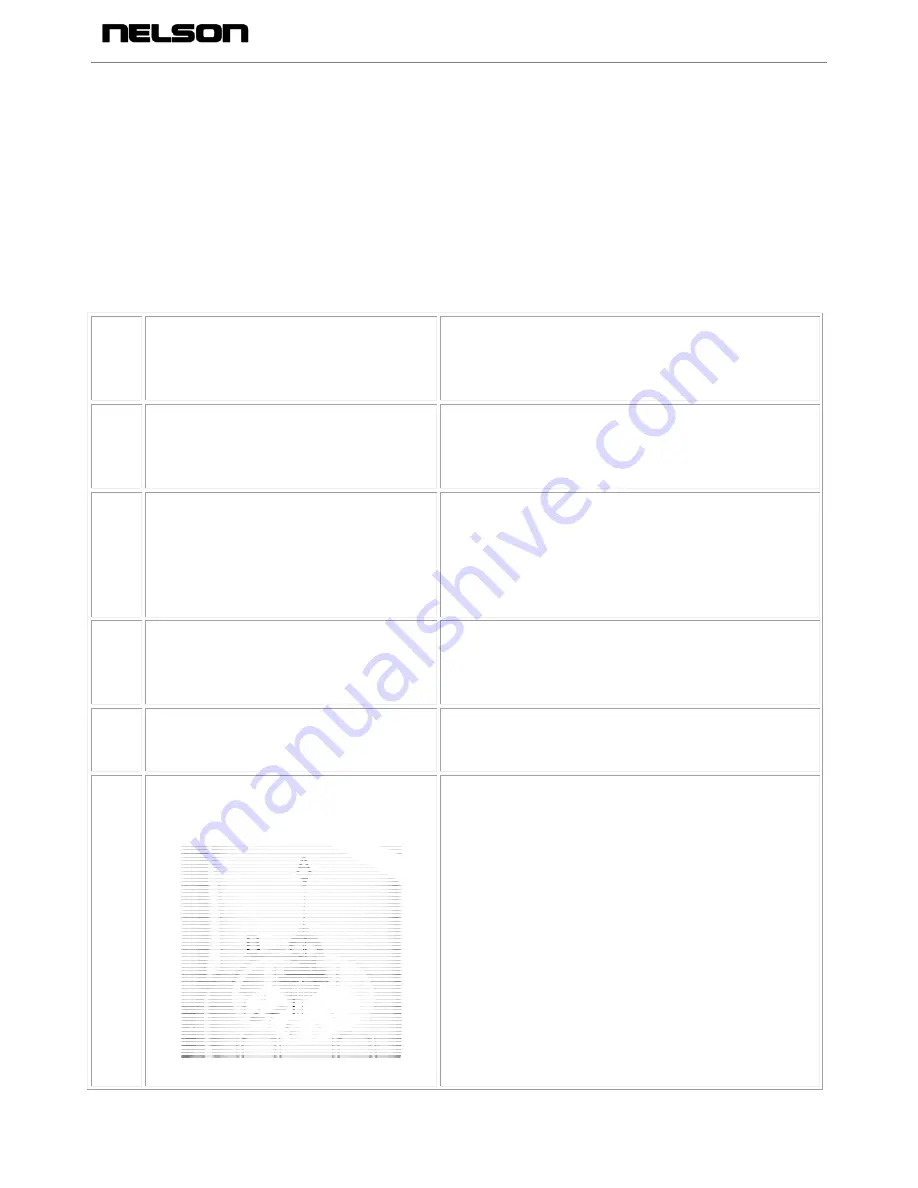
‐
NWG410
‐
26
11 MALFUNCTIONS SHOWN ON THE DISPLAY (FOR
THE USER)
The
glasswasher
is
able
to
identify
a
number
of
malfunctions
and
show
them
on
the
display.
If
the
problem
persists
after
the
glasswasher
has
been
switched
off
and
back
on,
proceed
as
described
below:
E.1
Boiler
temperature
probe
malfunction
Switch
the
glasswasher
off
and
back
on
and
perform
another
cycle;
if
the
problem
persists
call
the
after
‐
sales
service
E.2
Tank
temperature
probe
malfunction
Switch
the
glasswasher
off
and
back
on
and
perform
another
cycle;
if
the
problem
persists
call
the
after
‐
sales
service
E.3
Water
intakemalfunction
Water
intake
not
completed
in
the
maximum
time
allowed
Check
dynamic
pressure
in
intake
system:
the
water
intake
filter
may
need
cleaning,
the
tap
may
be
turned
off
or
the
rinsing
nozzles
may
be
fouled.
E.4
Boiler
overheating.
Switch
the
glasswasher
off
and
wait
a
few
minutes,
then
switch
back
on
and
perform
another
cycle
If
the
problem
persists
call
the
after
‐
sales
service.
E.5
Tank
overheating
Switch
the
glasswasher
off
and
wait
a
few
minutes,
then
switch
back
on
and
perform
another
cycle.
If
the
problem
persists
call
the
after
‐
sales
service.
E.6
Water
not
pumped
out
of
tank
Inspect
the
filters
for
dirt
and
check
that
the
drain
hose
is
not
blocked,
bent
or
crushed.
Check
that
the
drain
pump
is
not
blocked
by
dirt
by
removing
the
insert
on
the
sump
(from
inside
the
tank,
see
photo)
If
the
system
fails
to
pump
out
because
the
drain
pump
is
fouled
(as
a
result
of
incorrect
filter
positioning),
proceed
as
follows:
Bale
out
the
glasswasher
with
a
basin
and
disconnect
it
from
the
electrical
mains.
Unscrew
the
screw
A
,
release
the
tang
B
and
lift
it.
Check
that
the
impeller
of
the
drain
pump
underneath
the
cover
turns
freely,
and
is
free
from
dirt,
limescale
residues,
or
pieces
of
glass.
Never
use
tools,
screwdrivers,
scissors,
etc.
Summary of Contents for NWG410MD
Page 1: ...PROFESSIONAL DISHWASHER...