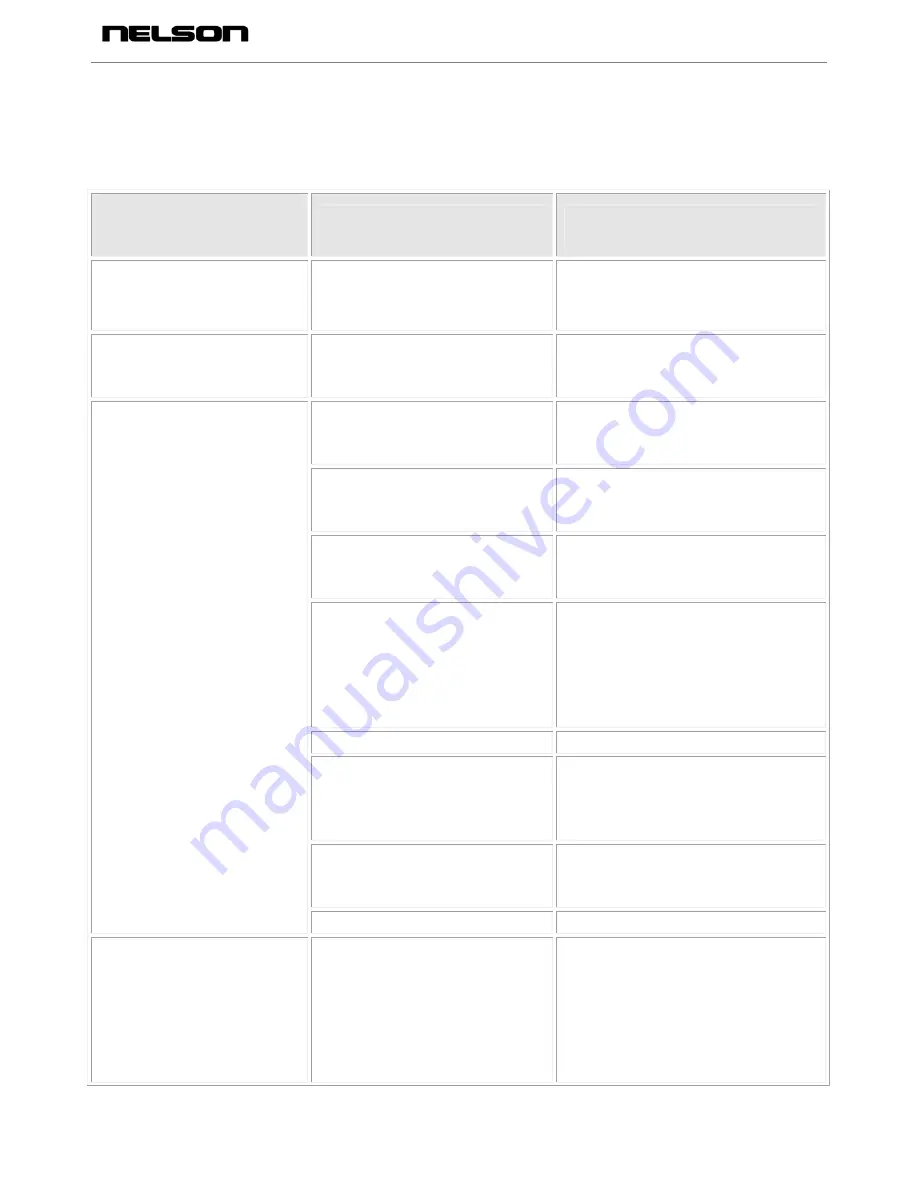
NW511
28
TROUBLESHOOTING
How
to
deal
with
any
problems
without
calling
the
after
‐
sales
service
PROBLEM
POSSIBLE
CAUSE
POSSIBLE
REMEDY
LIGHT
L1
DOES
NOT
COME
ON
Mains
power
failure
Check
electrical
mains
connection.
WASHING
PROGRAM
DOES
NOT
START
The
warewasher
has
not
yet
finished
filling.
Wait
for
the
3
program
lights
to
come
on.
POOR
WASHING
RESULTS
Spray
arm
washing
holes
blocked
by
dirt
or
limescale
Remove
spray
arms
and
clean
them
(9.2
Periodic
checks)
Filter
fouled
See
“Cleaning
the
filter
during
the
day”
Too
little
or
unsuitable
detergent
or
rinse
aid
Check
type
and
quantity
of
detergent.
No
or
not
enough
detergent
or
rinse
aid
being
supplied:
detergent
or
rinse
aid
not
being
taken
from
the
relative
container.
Check
that
the
intake
filter
is
not
fouled.
If
you
are
unable
to
solve
the
problem,
call
the
after
‐
sales
service.
Plates/glasses
badly
arranged
Arrange
plates/glasses
correctly.
Low
washing
temperature
Check
temperature
shown
on
the
display,
call
the
after
‐
sales
service
if
less
than
50°C
Inappropriate
cycle
set
Increase
wash
cycle
duration,
especially
if
dirt
has
dried
on.
INADEQUATE
RINSING
Dynamic
pressure
of
mains
water
insufficient
Spray
arm
nozzles
fouled
Limescale
in
boiler
Check
mains
water
pressure.
Check
that
water
intake
filter
is
not
fouled.
Clean
rinsing
nozzles.
If
you
are
unable
to
solve
the
problem,
call
the
after
‐
sales
service.