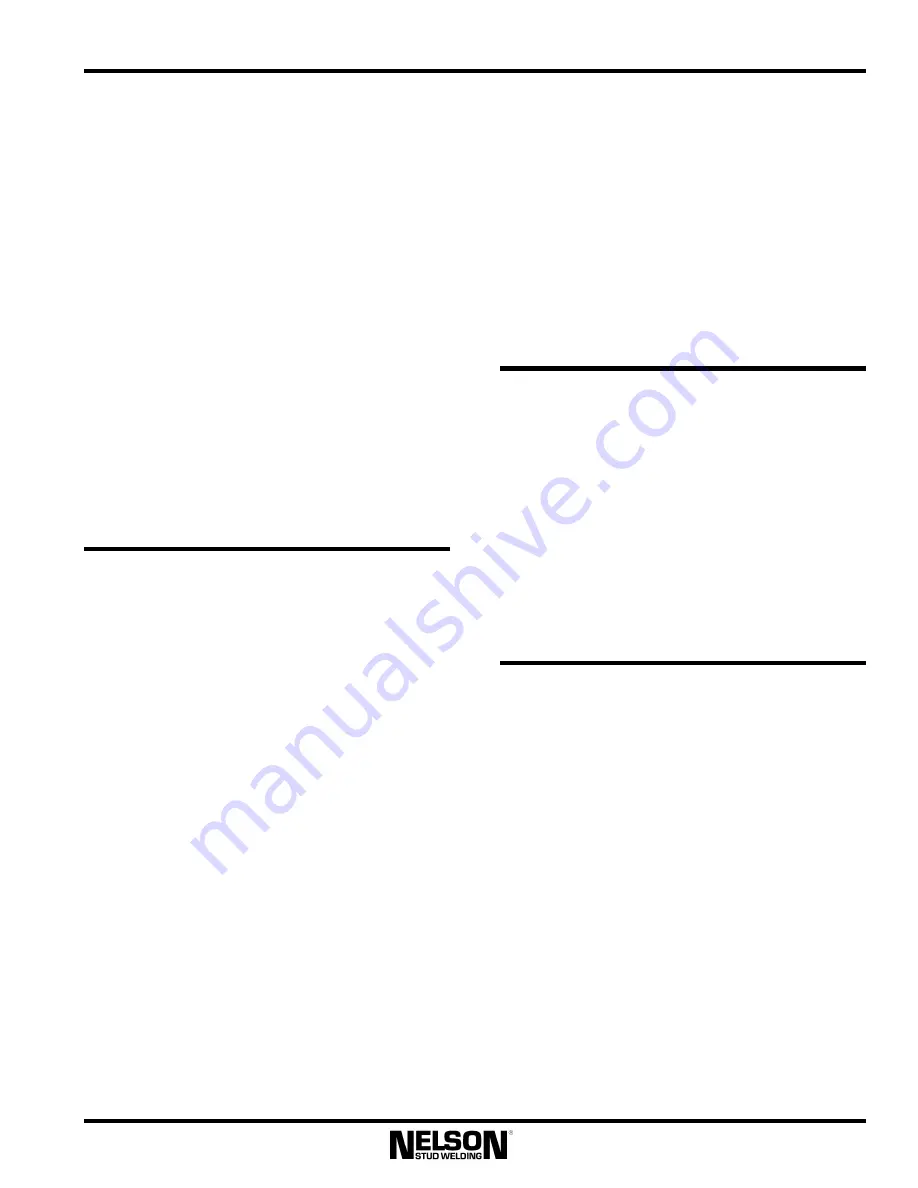
Nelweld Operations and Service Manual
- 13 -
Rather, the studs have a machined, slightly
tapered point through which the welding current
passes.
The weld pocket that is formed during Short
Cycle welding is not very deep, making it ideal
for welding to thin base materials.
Additionally, since the process can utilize
shielding gases, it is suitable for welding a wider
variety of metals, and attaching studs of greater
diameter. The use of a shielding gas during the
Short Cycle welding process defines the Gas Arc
welding process. The gas provides an inert
atmosphere in which highly reactive metals can
be welded safely.
Examples of the applications covered by both
Short Cycle and Gas Arc welding include
welding aluminum; copper, nickel, or chrome-
plated material; stainless steel; magnesium; and
even titanium.
2.4 Stud Welding Equipment
Stud welding was developed and has been in
continuous use for over 60 years. During that
time there have been many improvements in the
equipment used in the process, but the principles
remain the same. D.C. power is passed from a
stud welding control system that is set to provide
the time and current necessary to weld the stud,
and the lifting of the gun.
In past years, the power was supplied by power
sources separated from the control system such as
motor generators, transformer rectifiers or battery
banks.
The evolution in the stud welding industry in
recent years has been from mechanical to solid
state welding equipment with closed loop
controls. Incorporation of solid-state electronics
into stud welding units has facilitated:
•
Verification to measure both the weld time
and current
•
Compensation for weld cable or other
resistance changes in the weld circuit.
•
Compensation
for
incoming
power
fluctuations
•
System shutdown in case of variation from
the established weld parameters.
These features have contributed greatly to
simplified weld set up and increased weld quality
of current stud welding power supplies.
In another example, the change in the welding
gun plunge dampener from a potentially erratic
pneumatic weld plunge dampener to a very
reliable, self contained, sealed hydraulic plunge
dampener control has been another significant
contribution to weld quality.
2.5 Stud Materials
Stud materials and base materials must be
compatible with the stud welding process.
Suppliers of both materials can provide physical
and chemical certification on the products they
supply and these should be requested when orders
are placed, if needed.
Studs of all styles are available in low carbon
steel and various stainless steel grades. Most
commonly, Mild Steel Grades 1010 through 1020
and 18-8 Stainless Steel are used as stud
materials.
2.6 Stud Welding Setup Parameters
Full strength stud welding results can be obtained
by understanding the following settings or
adjustments, and how they relate to weld quality.
•
Plunge
is the amount of stud that protrudes
beyond the ferrule. This portion of the stud
length is available to be “burned off”, or
melted, to develop the weld flash. Long or
excessive plunge may cause excessive splatter
and high or uneven fillet formation. Plunge is
a physical measurement set and measured
with the stud and ceramic ferrule in place on
the stud gun.
•
Lift
is the distance the gun pulls the stud away
from the base material. Lift is essential to the
stud weld process since is creates an air gap
which the current must bridge. The current
flow across the resistance of this gap creates
the heat to melt the stud and base material.
Summary of Contents for Nelweld 4000
Page 58: ...Nelweld Operations and Service Manual 58 7 5 Declaration of Conformity...
Page 61: ...Nelweld Operations and Service Manual 61 8 2 Base and Side Cabinet Section...
Page 65: ...Nelweld Operations and Service Manual 65 8 4 Rear Cabinet Section...
Page 67: ...Nelweld Operations and Service Manual 67 8 5 Wiring Diagram...