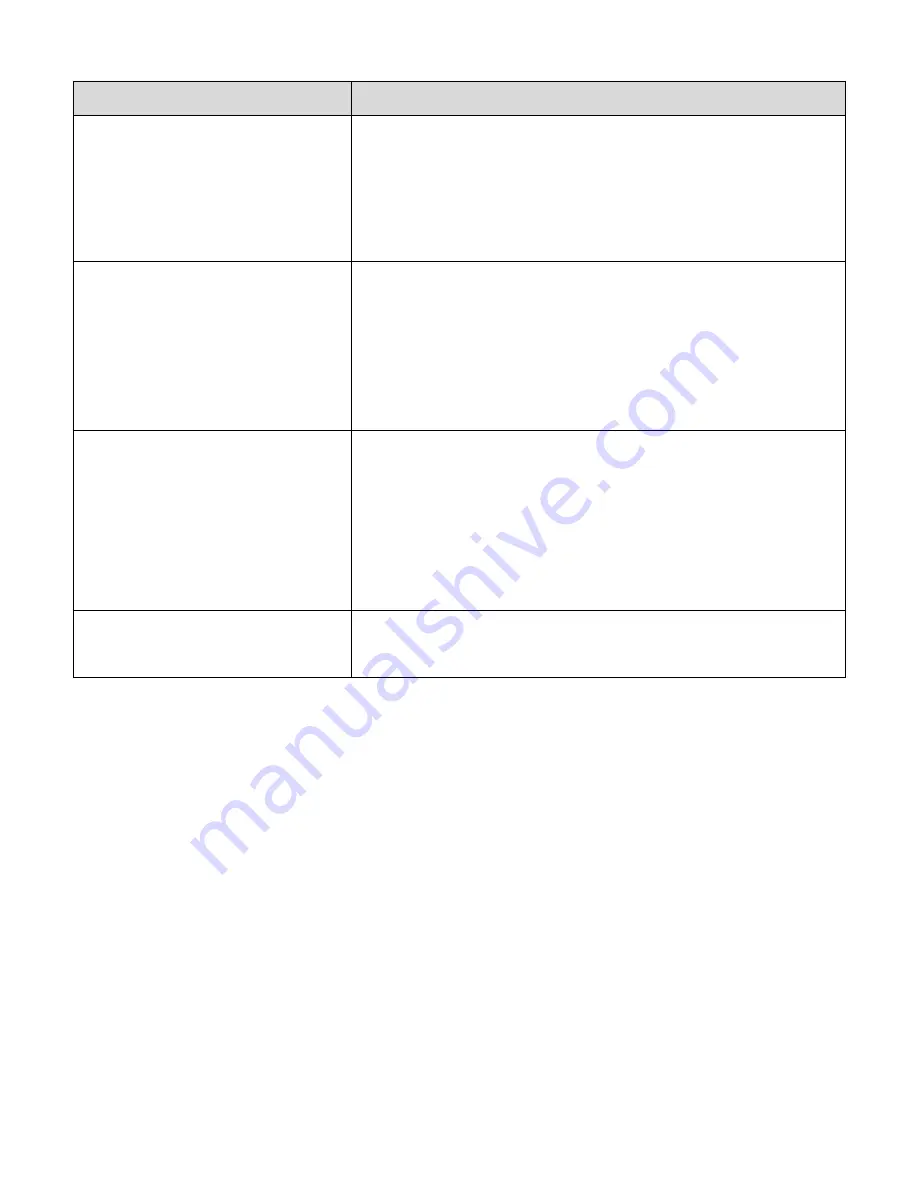
© 2016 Nelson Stud Welding, Inc.
Page 19
All Rights Reserved.
February 2016
Part No. 729-110-042 v1.03
Weld Issue
Weld Parameter Adjustments
Cold Weld
Weld failure at low strength value, no weld
flash or splatter, and weld base is
incompletely melted (very weak weld). This
indicates that not enough heat was
available.
Weld heat may be increased by:
Decreasing gap setting when in gap mode - The shorter distance reduces
the drop speed which allows for a longer arc or weld time.
Reducing spring pressure - Reducing the drop speed and provides a longer
weld time.
Increasing voltage - Increasing the voltage increases overall energy into
the weld.
Check stud timing tips (possibly too short).
Hot Weld
Weld failure at low strength value,
excessive weld flash and splatter, and weld
base may be undercut (weak weld). This
indicates that too much heat was available.
Weld heat may be decreased by:
Increasing gap setting when in gap mode - The longer distance speeds up
the weld time (faster drop time) and the faster drop time extinguishes the
arc sooner.
Increasing spring pressure - Speeding up the weld time and extinguishes
the arc sooner.
Decreasing voltage - Reducing the voltage reduces overall energy into the
weld.
Check stud timing tips (possibly too long).
Late or Cold Plunge
Cold plunge occurs when the stud contacts
the base material after solidification of the
molten weld metal has started. This results
in inconsistent weld strength and is
recognized by a shiny, mirror-like
appearance in the fracture surface.
This issue can be rectified by:
Increasing gap distance in gap mode - Increasing drop speed and gets the
stud into the molten pool faster.
Increasing spring pressure - Increasing drop speed and gets the stud into
the molten pool faster.
Decreasing voltage - Reducing the voltage reduces overall energy into the
weld.
Make certain that combo cable is installed (contact mode only). Otherwise
(if gap mode), remove combo cable - Reducing the amount of weld energy
consumed in the cables.
Misfire
No arc initiation due to timing tip failing to
flash.
This issue can be rectified by:
Increasing voltage.
Using 10% detergent solution spray mist.