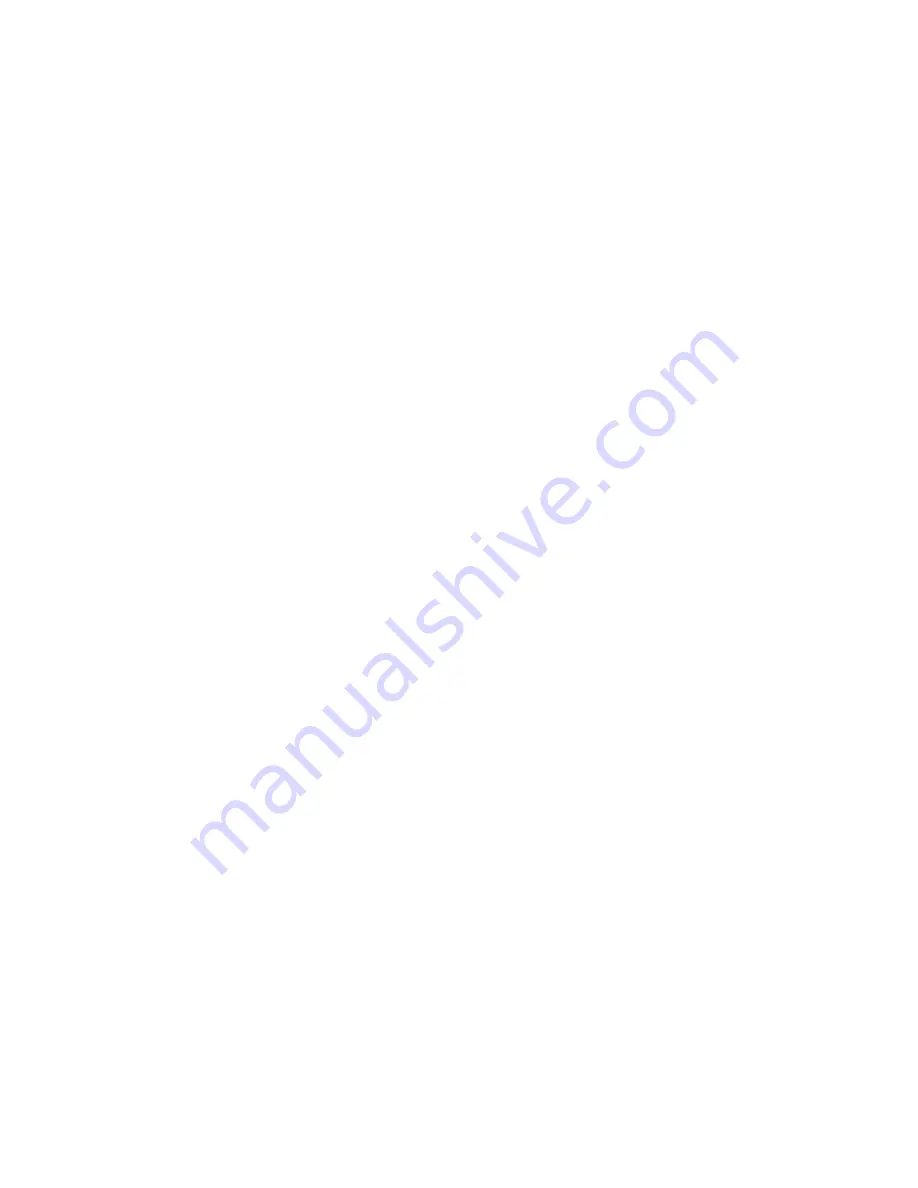
4
3. GETTING
STARTED
3.1 Set-up
Fitting the air inlet with the nitto fitting
-
Put plumbers tape around the thread of the nitto fitting.
-
Screw the nitto fitting into the air inlet.
Connect to a compressor with an air hose.
Fit the required socket to the anvil
3.2 Air supply
Ensure wrench trigger is in the “off” position before connecting to the air supply.
It will require air pressure of 6.3 bar, and air flow according to specification.
WARNING! Ensure the air supply is clean and does not exceed 90psi while operating
the wrench. Too high an air pressure and unclean air will shorten the product life due
to excessive wear, and may be dangerous causing damage or personal injury.
Drain the air tank daily. Water in the air line will damage the wrench.
Clean air inlet filter weekly.
Line pressure should be increased to compensate for unusually long air hoses
(over 8 meters). The hose diameter should be 3/8” I.D.
Keep hose away from heat, oil and sharp edges. Check hose for wear, and make
certain that all connections are secure.
3.3 Lubrication
An automatic in-line filter-regulator-lubricator is recommended as it increases tool
life and keeps the tool in sustained operation. The in-line lubricator should be
regularly checked and filled with air tool oil.
Proper adjustment of the in-line lubricator is performed by placing a sheet of paper
next to the exhaust ports and holding the throttle open approximately 30 seconds.
The lubricator is properly set when a light stain of oil collects on the paper.
Excessive amounts of oil should be avoided.
In the event that it becomes necessary to store the tool for an extended period of time
(weeks, months,…), it should receive a generous amount of lubrication at that time.
The tool should be run for approximately 30 seconds to ensure oil has been evenly
distributed throughout the tool. The tool should be stored in a clean and dry
environment.
It is most important that the tool be properly lubricated by keeping the air line
lubricator filled and correctly adjusted. Without proper lubrication the tool will not
work properly and parts will wear prematurely.
Use the proper lubricant in the air line lubricator. The lubricator should be of low air
flow or changing air flow type, and should be kept filled to the correct level. Use only
recommended lubricants, specially made for pneumatic applications. Substitutes
may harm the rubber compounds in the tools, O-rings and other rubber parts.
3.4 Installation lubricator/regulator
If no filter/ pressure regulator/ lubricator is installed in the compressed air system,
then pneumatic tools must be lubricated with 2 to 6 drops of tool oil at least once a