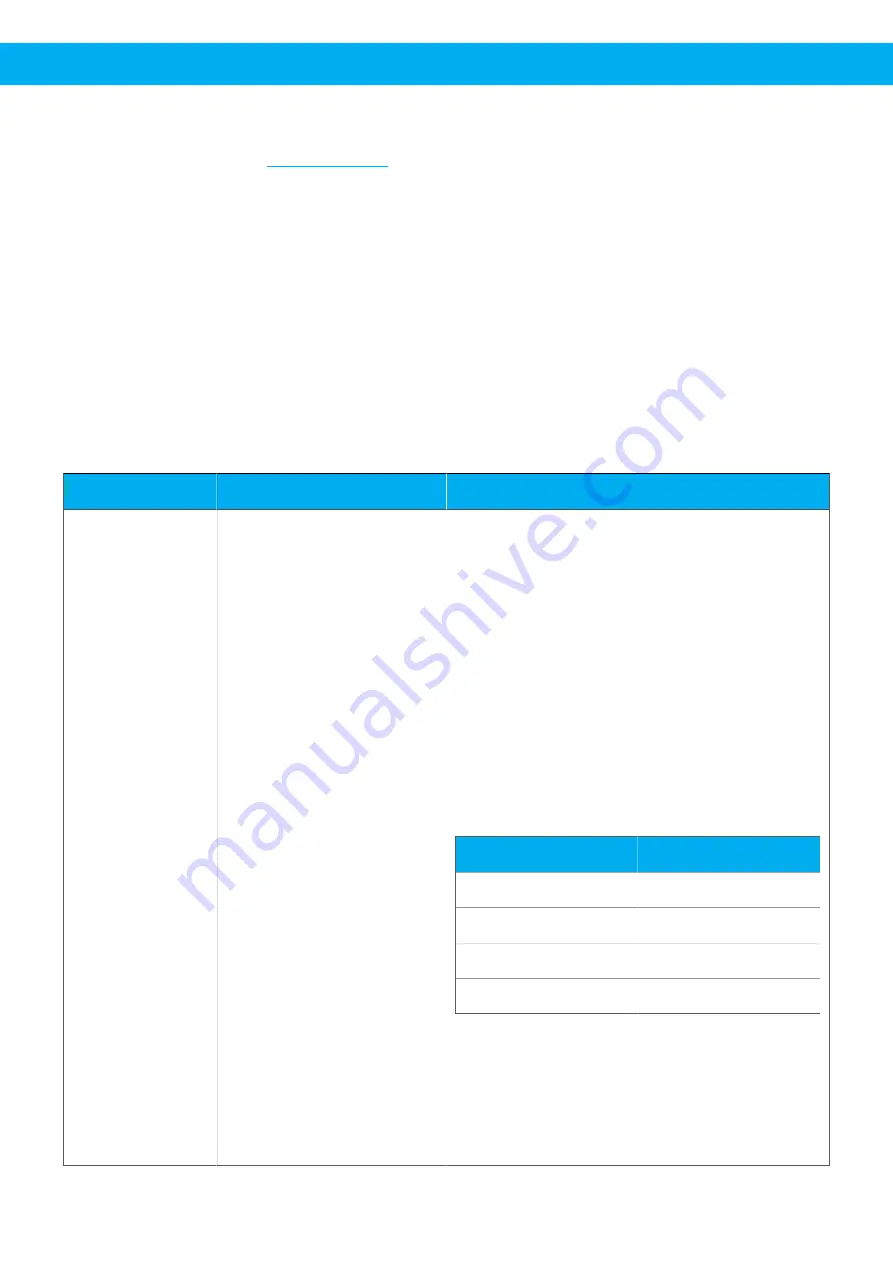
FlexPAK
7 Troubleshooting
and the included electrical diagrams.
There is no overcurrent relay. The frequency converter parameter for maximum current is adjusted from the
factory and is not to be adjusted.
If a fault occurs which cannot be adjusted according to the following descriptions, a Nederman service techni-
cian is to be called.
7.1 Tools
To carry out troubleshooting, it is necessary to have a multimeter with V DC and ohm measuring capabilities.
7.2 Remove the lid of the start and control unit
Remove the lid as follows:
1 Unscrew the four plastics screws in the corner of the control cabinet.
2 Lift of the lid.
3 Identify the PLC and the terminals at the bottom of the cabinet.
Table 7.1 Troubleshooting guide
Error
Possible cause
Solution
The unit unexpec-
tedly goes directly
into Running mode
when the Standby/
Running button is
pressed.
• A valve at a workstation is open
and its micro switch is activated
• The PS cable is damaged with
its wires short-circuited
If the PS cable is damaged, press the Standby/Running but-
ton to put the unit into Off mode and investigate the fault.
If necessary, loosen the PS cable from the control unit, see
the electrical diagrams, and use an ohmmeter across the
leads in turn to locate the fault.
Defect PT100 tem-
perature sensor.
Check whether the PT100 sensor is defective as follows:
1 Disconnect the PT100 sensor wire from terminal 77
and measure the resistance between terminal 78 and
the disconnected sensor wire.
2 Measure the resistance in the sensor using an ohm-
meter. The values in the table below are standard val-
ues, so a deviation from the measured value is normal.
If the averaged output (in ohm) deviates more than
±2% from these values, the sensor will need to be re-
placed.
Temperature (°C)
Averaged output (ohm)
0
100
20
110
80
131
135
150
If the sensor has a resistance >150 ohms, there will be a
high-temperature alarm. To check whether the sensor in-
put is working correctly, disconnect the PT100 wire at ter-
minal 77 and connect a jumper between terminals 77 and
78. Press the OK button on the PLC to reset the alert.
If the alert disappears, the PT100 sensor input is working,
and the PT100 sensor will need to be replaced.
21
Summary of Contents for FlexPAK Series
Page 6: ...FlexPAK 13 12 10 9 7 8 2 1 3 4 6 5 11 3 11 7 8 9 12 13 15 14 18 19 10 17 4 16 15 20 5 6...
Page 7: ...FlexPAK 6 1 2 3 6 7 8 9 16 15 14 13 11 10 12 4 5 7 7...
Page 9: ...FlexPAK 2 1 4 5 6 8 7 9 3 9 1643 1mm 65 662 1mm 26 2 1771 4 1mm 70 1 10 9...
Page 10: ...FlexPAK 11 12 13 14 10...
Page 11: ...FlexPAK A A A A C Min 2 1m 83 15 1 0 m 39 4 16 A B C 17 11...
Page 29: ...www nederman com...