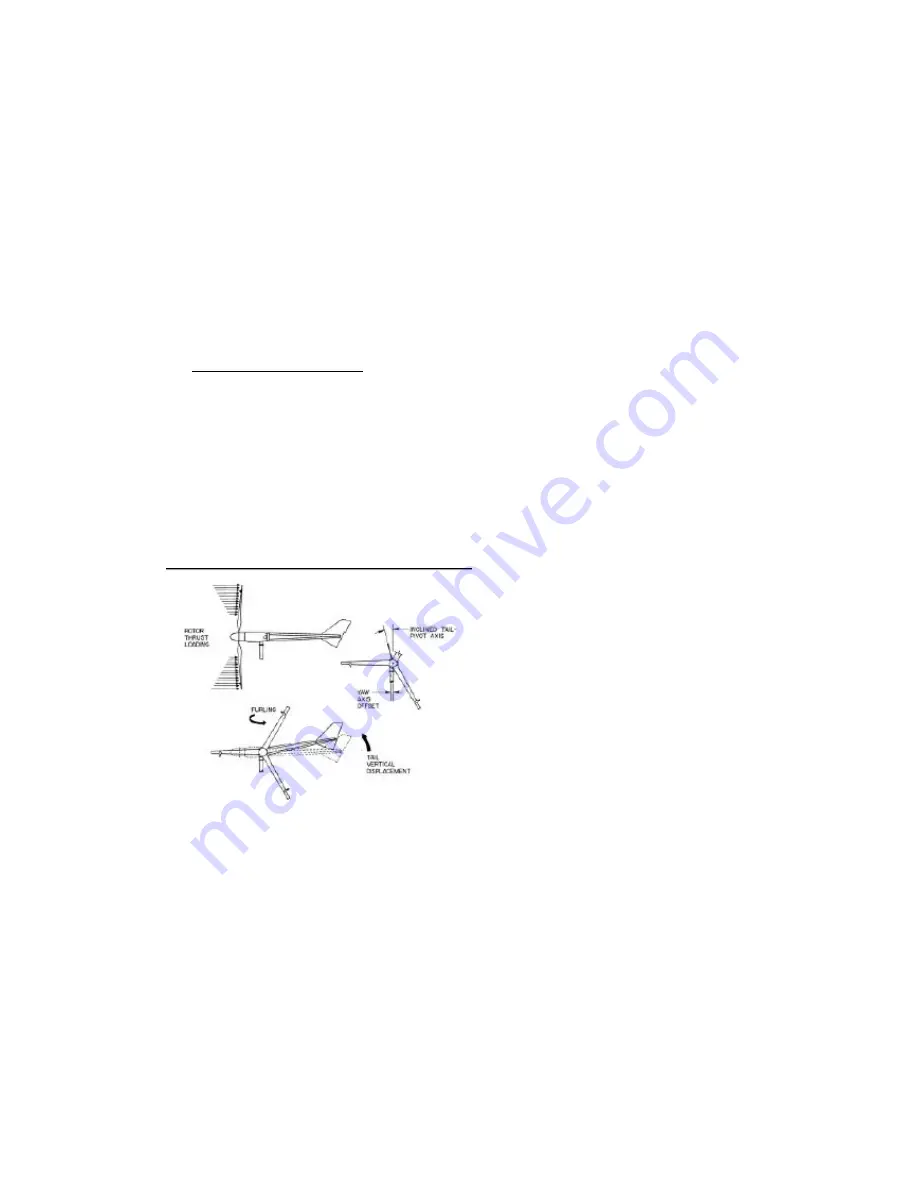
The rotor should begin to rotate when the wind speed reaches approximately 3m/s.
(for the first several weeks of operation, however, the start-up wind speed will be
higher because the bearing seals have not wornin.) battery charging should
commence shortly after the rotor spins up to speed. Once turning, the rotor will
continue to turn in lower wind speeds, down to approximately 2.5m/s. the rotor speed
will increase with increasing wind speed and the system will provide a higher output.
This output increase rapidly because the energy available in the wind varies as the
third power(cube) of the wind speed. For example, if the wind speed doubles from
5m/s to 10m/s, the energy in the wind increases by a factor of eight(2
3
=2x2x2=8).
One result of this relationship is that there is very little energy available in light
winds. For the average site, winds in the range of 5.5-9m/s will provide most of the
system annual energy production.
B. High Winds – AutoFurl
During periods of high wind speeds the AutoFurl system will automatically protect
the wind turbine. When furled, the power output of the turbine will be significantly
reduced. In winds between 13m/s and 18m/s it is normal for the turbine to repeatedly
furl, unfurl and then furl again. In winds above 18m/s the turbine should remain
continuously furled.
AutoFurl is a simple and elegant method of providing high wind speed protection.
The AutoFurl system is based on aerodynamic forces on the rotor, gravity, and the
carefully engineered geometry of the wind turbine. As shown in Figure, the
aerodynamic forces acting on the blades cause a thrust force pushing back on the
rotor. This force increases with increasing wind speeds. The thrust force acts
through the centreline of the rotor, which is offset from the centreline of the tower
pivot axis(yaw axis). Therefore, the thrust force on the rotor is always trying to push
the rotor over to the side, away from the wind.
But the rotor is kept facing into the wind at speeds up to
~
12.5m/s by the wind
turbine tail assembly. The tail, in turn, is kept straight by its own weight because its
pivot at the back of the nacelle is inclined. So the weight of the tail holds it against a
rubber bumper and the tail holds the rotor into the wind.
The geometries in the systems are carefully balanced so that at
~
12.5m/s the rotor
force acting on the yaw-offset is large enough to overcome the preset force holding
the tail straight. At this point the rotor will start turning away from the wind or
furling. The tail stays aligned with the wind direction. The speed of furling depends