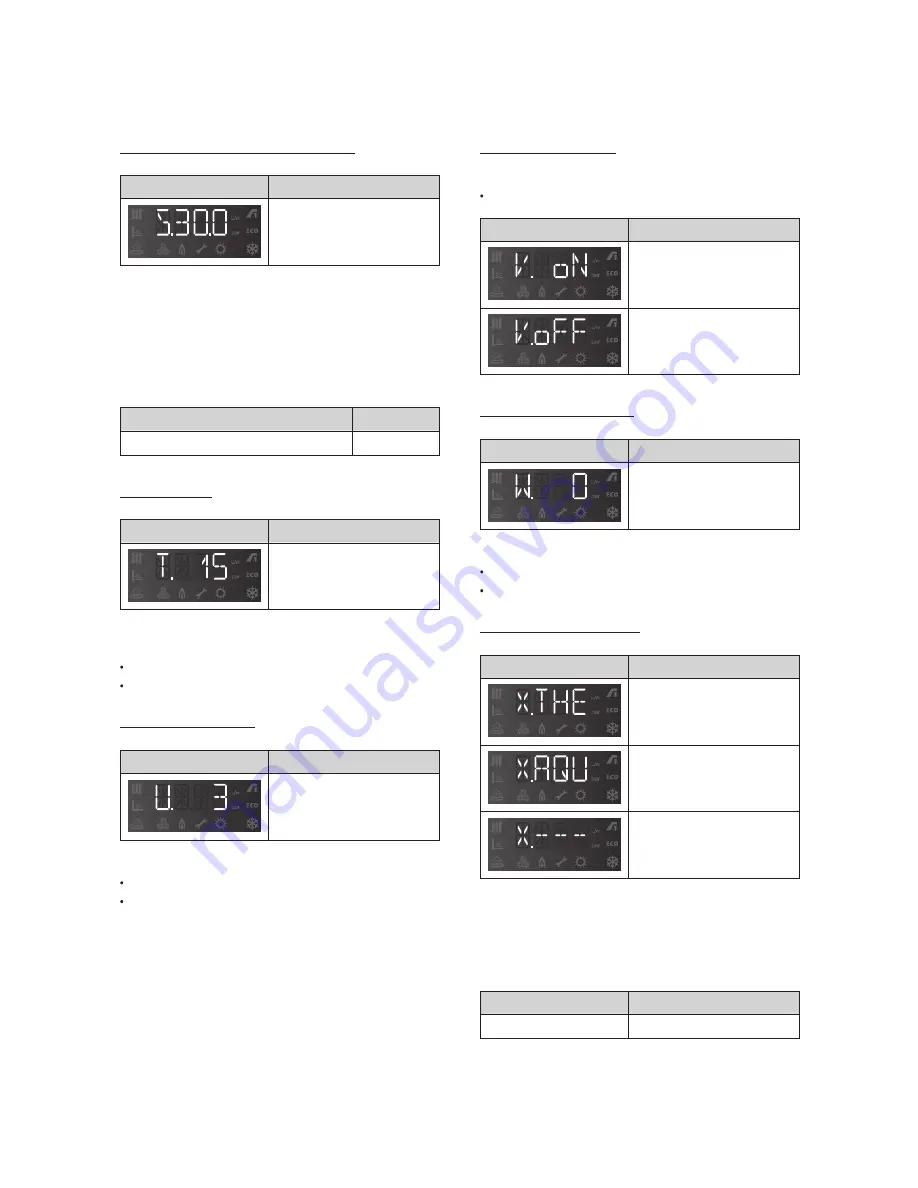
Setting the LCD Back Light
This menu may be used to set the status of LCD back light.
Default: ON
Display
Description
LCD back light maintains
minimum brightness.
LCD back light is off when no
button is pressed.
Setting the Maintenance Time
Display
Description
Maintenance time
This menu may be used to set the maintenance time.
Default: 0
Range: 0–999 days
Setting the DHW Heat Demand
Display
Description
DHW heat demand (with
cylinder temp. sensor)
DHW heat demand (with
cylinder stat)
DHW tank not in use
This menu may be used to select the control method for the
domestic hot water temperature when using an external tank.
You can select either cylinder temp. sensor or cylinder stat.
DHW Heat Demand Setting
Setting
Remark
DHW Heat Demand
Default: Cylinder temp. sensor
Setting the Return Absolute MIN Temperature
Display
Description
Return absolute MIN set point
(°C)
This menu can be used to change the minimum return
temperature range in Return Control mode. When Custom
mode is configured in Outdoor Reset Control mode, changes to
the return temperature are based on the return absolute MIN
temperature range.
Return Absolute MIN Temperature Range
Range
Remarks
20°C – [MAX set point - 10°C]
Default: 30°C
Low Burning Time
Display
Description
Low burning time during initial
heating.
This menu may be used to set the low burning time during
initial heating.
Default: 1 min
Range: 0–20 min
Burning Acceleration Time
Display
Description
Burning acceleration time to CH
Max during initial heating.
This menu may be used to set the burning acceleration time.
Default: 3 min
Range: 0–20 min
53
Operating the Boiler
Summary of Contents for NCB-20LHWE
Page 41: ...41 Wiring Examples for Different Applications...
Page 71: ...71 13 4 Ladder Diagram 3 15A Appendices...
Page 75: ...Memo...
Page 76: ...Memo...
Page 77: ...Memo...
Page 78: ...Memo...
Page 79: ......