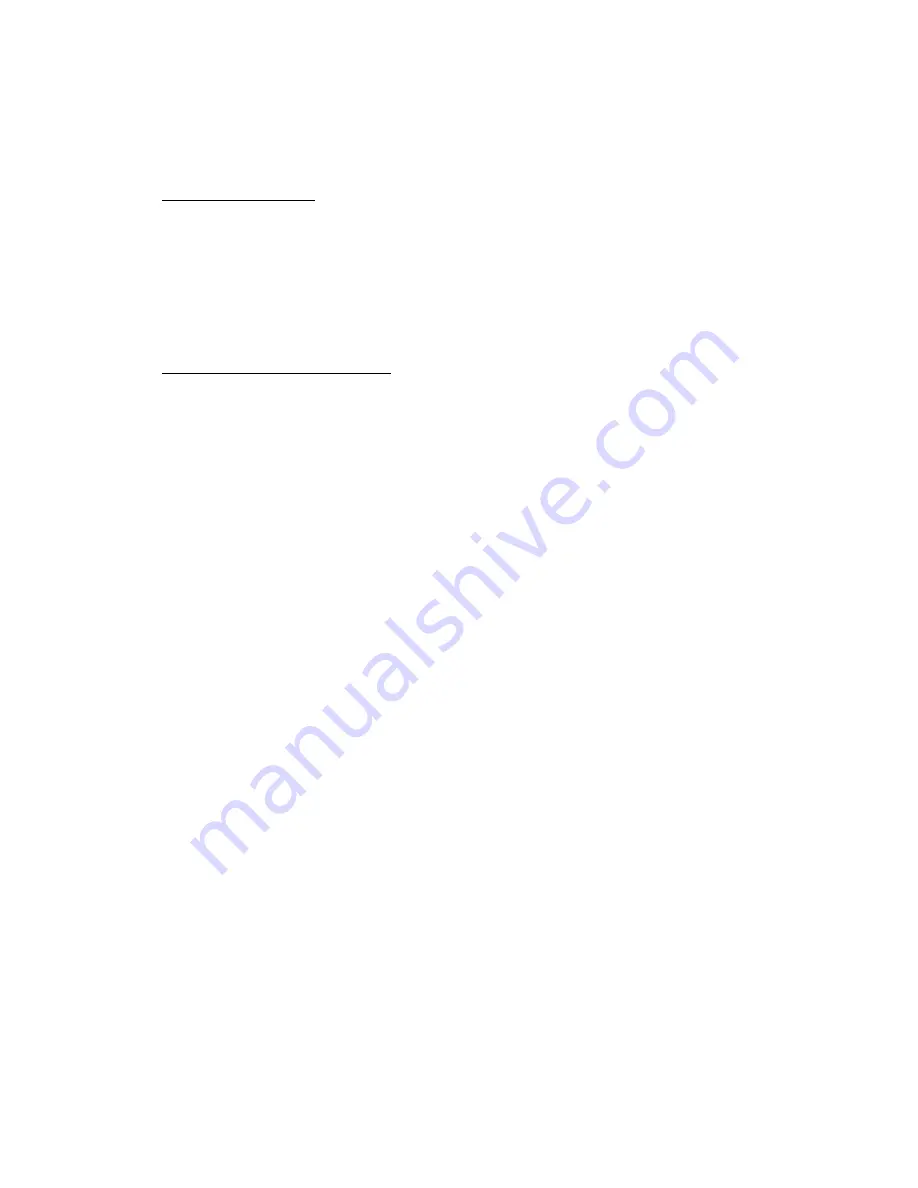
- A.5 -
APPENDIX C
SMART COUPLER II
INSTALLATION
When installing the mode switch in the instrument panel, orient it so that the two-color
LED is on top, and the word "HEADING" is on the right side.
Wire the NMEA 0183 output of your GPS receiver to pin 8 on the AP-1 main connector.
Plug the telephone-type cable into the appropriate jacks in the back of the AP-1 and the
mode switch.
INSTALLATION CHECK
After the installation is completed, you can quickly check if the Coupler is receiving and
decoding information from the GPS receiver.
1. Turn on the GPS receiver and put in a course from the present position to a nearby
waypoint.
2. Enable the serial output port from the GPS receiver to the AP-1.
3. Apply power to the AP-1. The LED will alternately flash green and yellow
several times.
4. Try to select course or heading mode before the GPS receiver has acquired its
minimum number of satellites. Do this by holding the switch to the left or right
for ½ second. The LED will rapidly flash alternately green and yellow, and then
go off. There should be 0±1 millivolts difference between pins 3 and 6 on the
AP-1 connector. If you enable the AP-1 in tracking mode, you should be able to
center the ailerons with the trim knob.
5. Once the GPS receiver has acquired its satellites, press the Coupler mode switch
to the left for ½ second. This selects Course mode, where the Coupler passes CDI
information from the GPS receiver to the AP-1. The LED will glow green. There
should still be less than 1 mV difference between pins 3 and 6.
6. Now enter a course such that your present position is at least 1.25 NM off course.
7. Again hold the switch to the left for ½ second to select Course mode. The LED
will again glow green if the receiver is ready. There should be 150±10 mV
difference between pins 3 and 6. The ailerons should be at full deflection.
8. Turn off the GPS receiver but leave the power applied to the AP-1.
9. After approximately 30 seconds, the Coupler LED will go off. The ailerons
should go back to center.
10. This completes the installation check.
Summary of Contents for AP-1
Page 2: ......
Page 9: ...7 WIRING DIAGRAM FOR HAND HELD GPS AND AP 1 WITH GPS COUPLER WIRING DIAGRAM Fig 3...
Page 27: ...A 3...