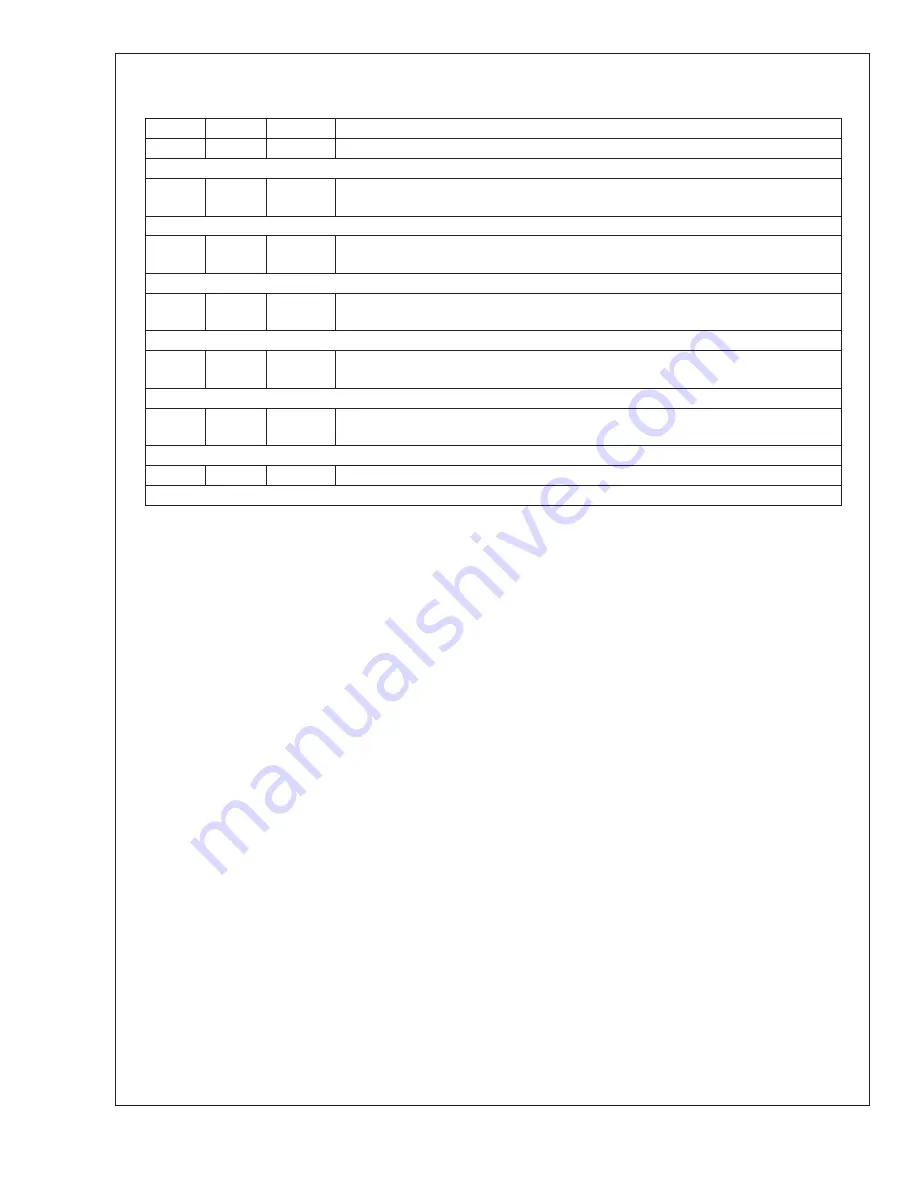
I. Program Modules
(Continued)
TABLE 5. Trajectory Programming Module
Port
Bytes
Command
Comments
c
1F
LTRJ
This command initiates loading the trajectory parameters input buffers.
Busy-bit Check Module
d
d
00
0A
HB
LB
These two bytes are the trajectory control word. A 0A hex LB indicates velocity and
position will be loaded and both parameters are absolute.
Busy-bit Check Module
d
d
xx
xx
HB
LB
Velocity is loaded in two data words. These two bytes are the high data word.
Busy-bit Check Module
d
d
xx
xx
HB
LB
velocity data word (low)
Busy-bit Check Module
d
d
xx
xx
HB
LB
Position is loaded in two data words. These two bytes are the high data word.
Busy-bit Check Module
d
d
xx
xx
HB
LB
position data word (low)
Busy-bit Check Module
c
01
STT
STT must be issued to execute the desired trajectory.
Busy-bit Check Module
STOP MODULE
This module demonstrates the programming flow required to
stop shaft motion.
While the LM628 operates in position mode, normal stopping
is always smooth and occurs automatically at the end of a
specified trajectory (i.e. no stop module is required). Under
exceptional conditions, however, a stop module can be used
to affect a premature stop.
While the LM628 operates in velocity mode, stopping is
always accomplished via a stop module.
The example stop module, shown in
, utilizes an
LTRJ command sequence and an STT command.
Load Trajectory Parameters
Bits eight through ten of the trajectory control word select the
stopping mode. See
In the case of the example module, the first byte of the
trajectory control word, x1 hex, selects motor-off as the
desired stopping mode. This mode stops shaft motion by
setting the motor drive signal to zero (the appropriate
offset-binary code to apply zero drive to the motor).
Setting bit nine of the trajectory control word selects stop
abruptly as the desired stopping mode. This mode stops
shaft motion (at maximum deceleration) by setting the target
position equal to the current position.
Setting bit ten of the trajectory control word selects stop
smoothly as the desired stopping mode. This mode stops
shaft motion by decelerating at the current user-programmed
acceleration rate.
Note:
Bits eight through ten of the trajectory control word must be used
exclusively; only one of them should be logic one at any time.
Start Motion Control
The start motion control command, STT, must be executed
to stop shaft motion.
Comments
After shaft motion is stopped with either an “abrupt” or a
“smooth” stop module, the control system will attempt to hold
the shaft at its current position. If forced away from this
desired resting position and released, the shaft will move
back to the desired position. Unless new trajectory param-
eters are loaded, execution of another STT command will
restart the specified move.
After shaft motion is stopped with a “motor-off” stop module,
desired shaft position tracks actual shaft position. Conse-
quently, the motor drive signal remains at zero and the
control system can not affect shaft position; the shaft should
be stationary and free wheeling. If there is significant drive
amplifier offset, the shaft may rotate slowly, but with minimal
torque capability. Unless new trajectory parameters are
loaded, execution of another STT command will restart the
specified move.
AN-693
www.national.com
8