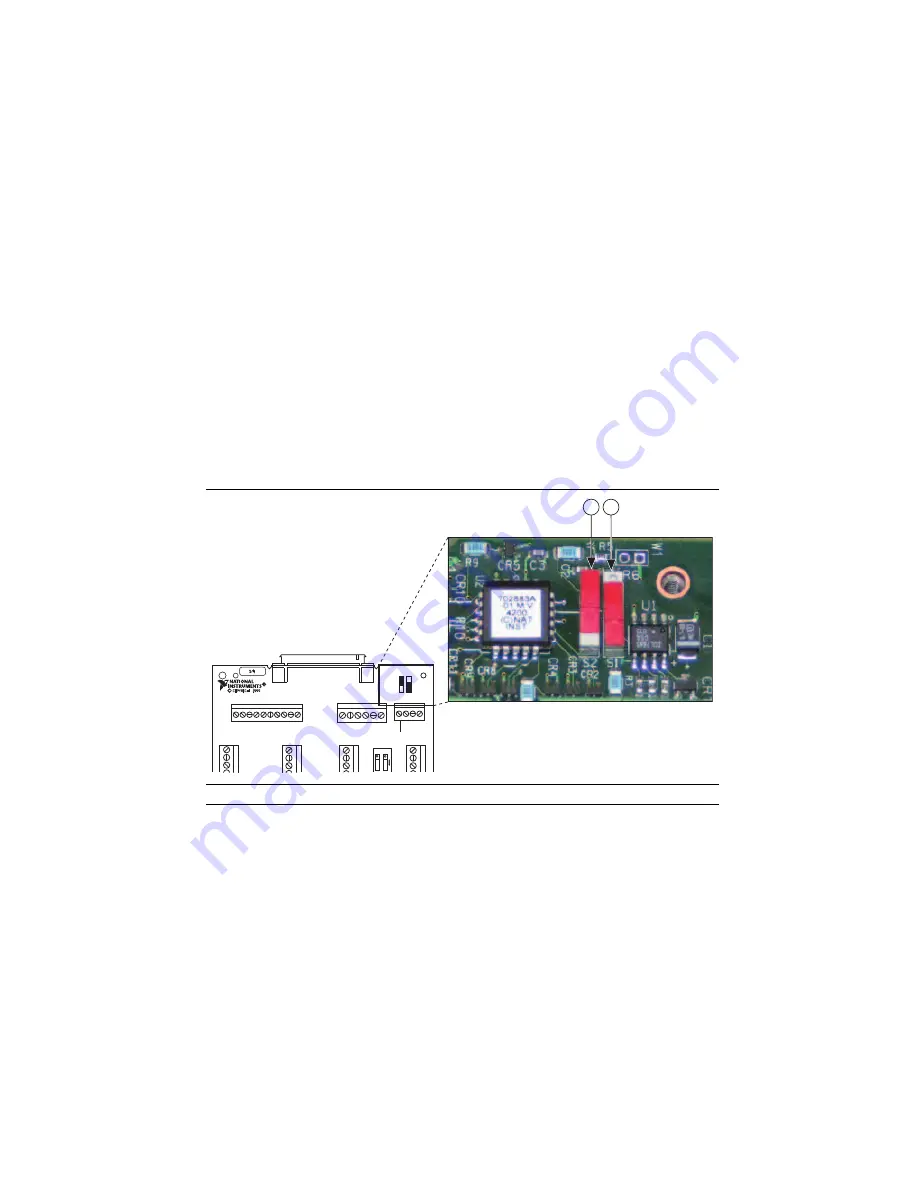
Getting Started with NI 7340/7350 Controllers and AKD Drives
|
© National Instruments
|
13
The UMI-7764 to AKD Drive Cable contains the following connections:
•
UMI-7764 Screw Terminal Leads
—Pigtail wire leads labeled with UMI-7764 signal
names.
•
X8 10-Pin Connector
—10-pin connector containing the servo command, enable, and
fault signals.
•
X9 DSUB Connector
—9-pin DSUB connector containing emulated encoder output
signals from the AKD servo drive.
•
X1 3-pin Connector
—+24 V power supply connection for the AKD servo drive.
•
+24V Power Supply Leads
—+24 V power supply leads.
3.
Configure the UMI-7764 DIP switches. You must set the DIP switches to the following
settings to match the polarity configuration for the AKD servo drive:
•
Inhibit Input (S2)—Active High
•
Inhibit Output (S1)—Active Low
The UMI-7764 DIP switch configuration is shown in Figure 7.
Figure 7.
UMI-7764 Inhi
b
it Input and Inhi
b
it Output DIP Switch Settings
4.
Connect an ex5 V power supply to the UMI-7764 Power Input Terminal Block. This
connection is required to power the encoder circuitry that converts differential encoder
signals to single-ended signals for the motion controller, as well as to power the UMI-7764
Inhibit Output signals.
1
Inhi
b
it Input Polarity Switch (S2)
2
Inhi
b
it Output Polarity Switch (S1)
1
BP4
BP3
BP2
BP1
GND
+5 V
TRIG4
TRIG3
TRIG2
TRIG1
ASSY1
8
6343A-01
UMI-7764
FWDLIM1
HOME1
REVLIM1
AXIS1
FWDLIM3
HOME3
REVLIM3
AXIS3
AIGND
AREF
AIN4
AIN3
AIN2
AIN1
FWDLIM2
HOME2
REVLIM2
AXIS2
FWDLIM4
HOME4
REVLIM4
AXIS4
GND
NC1
SHUTDO
WN
INH ALL
S2 S1
ACTIVE HIGH
LO
W
2
Summary of Contents for PXI-7358
Page 1: ...PXI 7358...