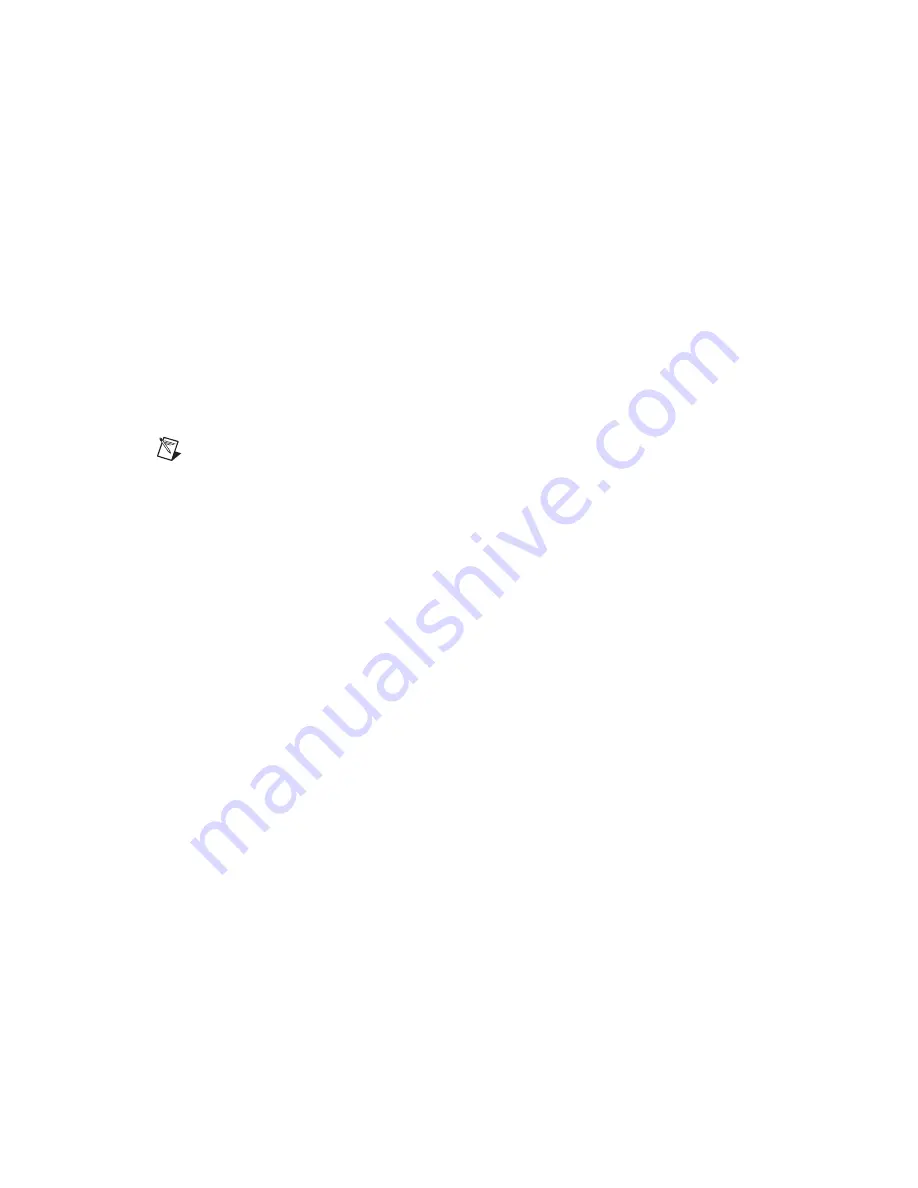
Chapter 1
Introduction
NI PCI-7342 Hardware User Manual
1-2
ni.com
National Instruments devices. The RTSI bus provides high-speed
connectivity between National Instruments products, including image
acquisition (IMAQ) and data acquisition (DAQ) devices. With RTSI, you
can easily synchronize several functions to a common trigger or timing
event across multiple motion, IMAQ, and DAQ devices.
RTSI requires no external cabling and does not consume host bus
bandwidth. Additionally, the RTSI bus features built-in switching that you
can control with software to route signals to and from the bus on the fly.
The bus interface on PCI devices is an internal 34-pin connector. Signals
are shared through a ribbon cable inside the PC enclosure. RTSI cables are
available for chaining two, three, four, or five devices together.
Note
Seven of the 34 pins on the RTSI connector are available for user signals. You can
use the software-configurable RTSI switch to accommodate more than seven signal options
for each device. With this many-to-few selector switch, any available signal can be routed
to any RTSI pin. You can also route more than one signal to a single RTSI pin or connect
two RTSI pins to the same signal.
Refer to the National Instruments Developer Zone at
ni.com/zone
for
more information about RTSI, including tutorials, examples, and
configuration guidelines.
PCI-7342 Features
The PCI-7342 controller combines servo and stepper functionality for PCI
bus computers. It provides motion control for up to two independent or
coordinated axes of motion.
You can use the PCI-7342 motion controller for point-to-point
and straight-line vector moves for stepper and servo motor applications.
Servo and Stepper Fundamentals
Servo axes can control servo motors, servo hydraulics, servo valves, and
other servo devices. Servo axes always operate in closed-loop mode. These
axes use quadrature encoders or analog inputs for position and velocity
feedback and provide analog command outputs with an industry-standard
range of ±10 V.
Stepper axes control stepper motors and operate in open- or closed-loop
mode. They use quadrature encoders or analog inputs for position and
velocity feedback (closed-loop only), and provide step/direction or