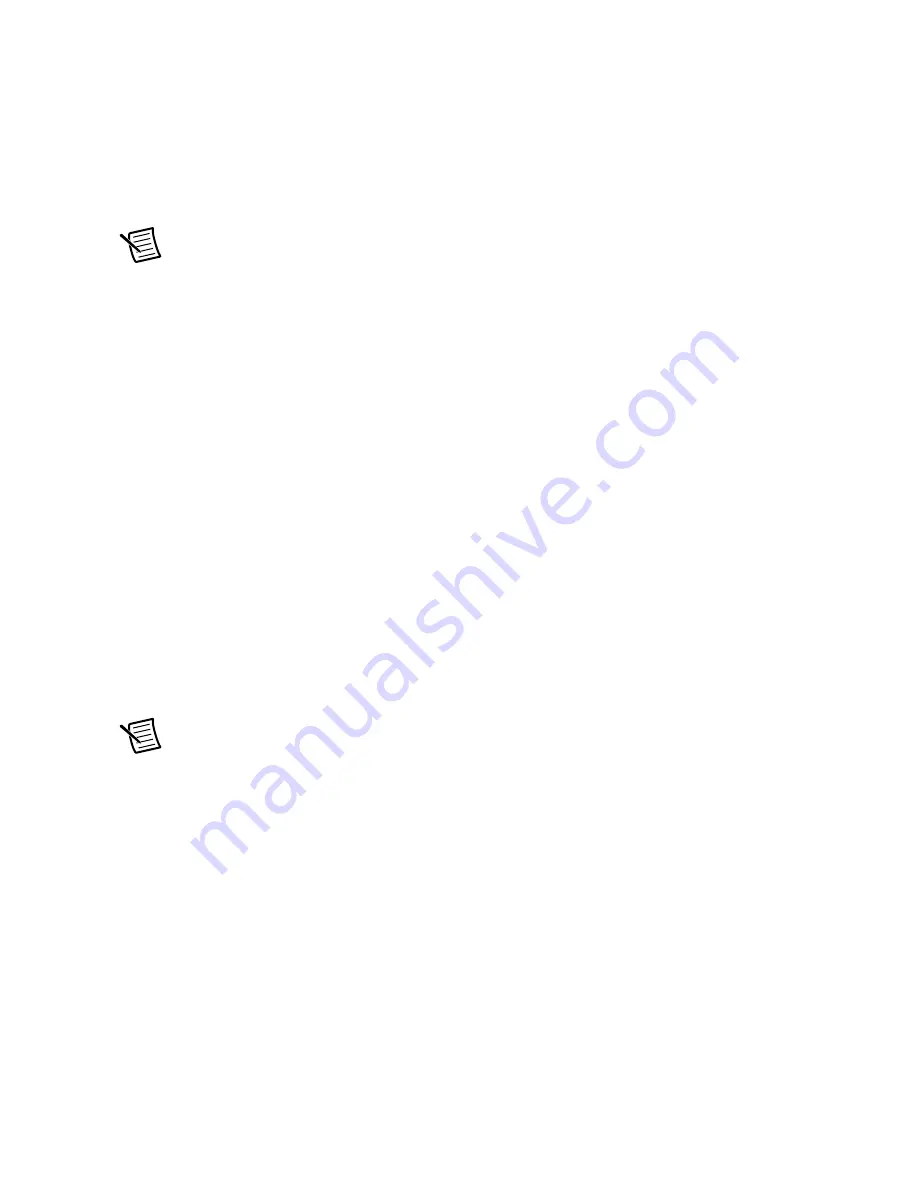
1
8
|
ni.com
|
PCI/PXI/PCIe-6509 User Guide and Specifications
The figure shows a rising (0 to 1) transition. The same filtering applies to falling (1 to 0)
transitions.
Programmable Power-Up States
You can program the DIO lines on the NI 6509 to power up at a predefined state: input, high
output, or low output. Programmable power-up states ensure that the NI 6509 powers up in a
known state.
Note
On the PCIe-6509, the DIO lines can be pulled high or low. For more
information, refer to the
I/O Pull-Up/Pull-Down Resistors (PCIe-6509 Only)
section.
The typical response time of programmable power-up states is 400 ms for the PCI/PXI-6509 and
500 ms for the PCIe-6509.
To use MAX (recommended) to program the power-up states, select the device and click the
Properties
button. Refer to the software documentation for information about how to program
the power-up states using NI-DAQmx with LabVIEW or other NI application development
environments (ADEs).
Change Detection
You can program the NI 6509 to send an interrupt when a change occurs on any input line. The
NI 6509 can monitor changes on selected input lines or on all input lines. It can monitor for rising
edges (0 to 1), falling edges (1 to 0), or both.
When an input change occurs, the NI 6509 generates an interrupt and notifies the software.
However, the NI 6509 does not report which line changed or if the line was rising or falling.
After a change, you can read the input lines to determine the current line states. The rate of
change detection is determined by the software response time, which varies from system to
system.
Note
Excessive change detections may affect system performance. Use digital
filtering to minimize the effects of noisy input lines.
An overflow bit indicates that the NI 6509 detects an additional rising or falling edge before the
software processes the previous change.
Refer to the software documentation for information about how to set up and implement the
change detection feature.