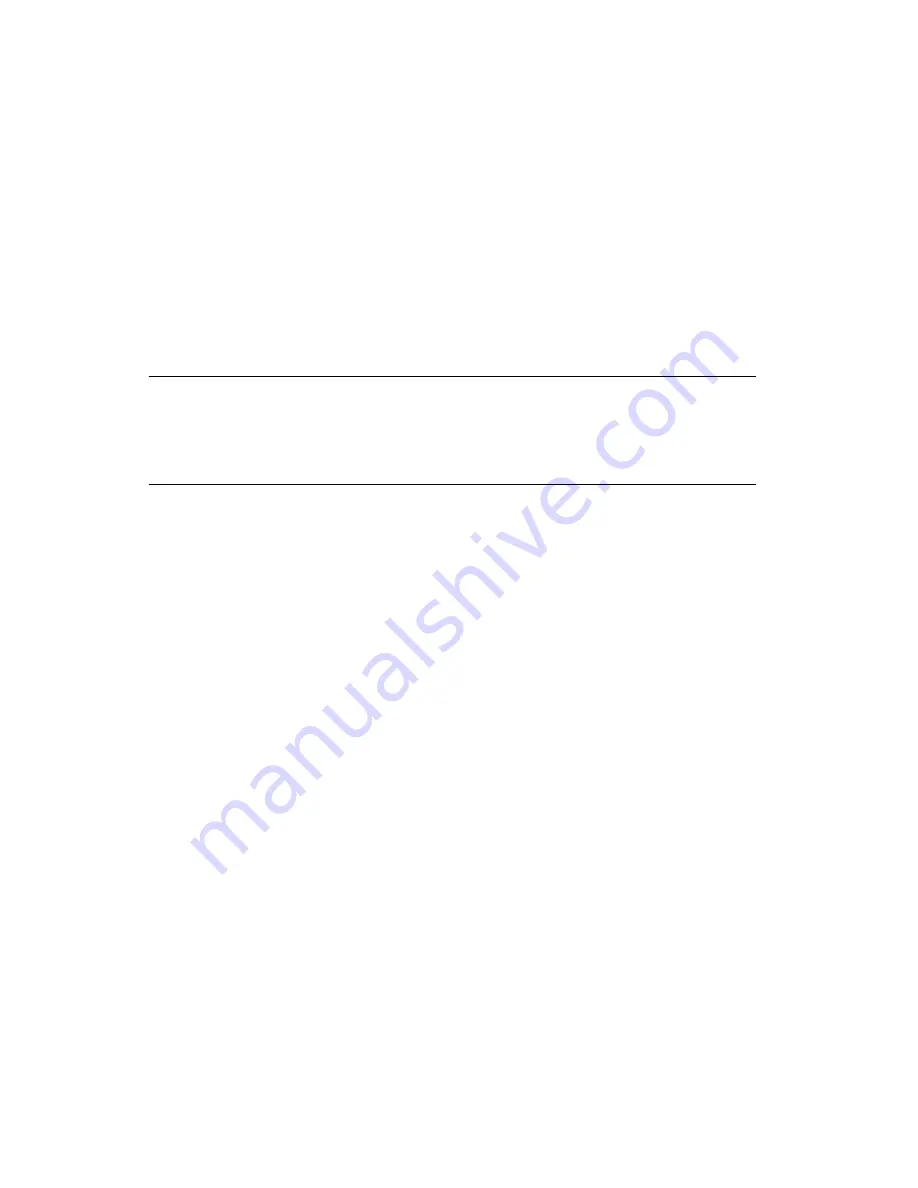
MID-7654/7652 Servo Power Motor Drive User Guide
26
ni.com
Changing the Line Voltage
Follow these steps to change the line voltage on your MID-7654/7652:
1.
Pry open the hinged cover on the power entry module (number 7 in Figure 6).
2.
Remove the fuse holder.
3.
Replace the two fuses with the appropriate fuses for the desired line voltage as listed in the
section.
4.
Rotate the fuse holder 180 degrees so the desired line voltage number shows through the window
when the power module cover is closed.
5.
Push the fuse holder back into the power entry module with the new orientation.
6.
Close the hinged cover.
Amplifier/Driver Command Signals
The PWM amplifiers used in the MID-7654/7652 accept an industry-standard ±10 V analog torque
(current) command signal. Servo motion controllers used with the MID-7654/7652 provide this standard
output and are programmed to close both the velocity loop and position loop using an enhanced
PID algorithm.
Specifications
The following specifications apply only to the MID-7654/7652. You must account for your motion
controller to obtain a system specification. Refer to your controller specifications to determine overall
system specifications.
Some signals define compatibility as signal pass-through, which means the MID-7654/7652 may use
passive filtering on these signals. This will not affect the voltage range or current handling capability.
Consult your motion controller specifications to determine the allowable voltage range and logic level
compatibility of the signal.
Servo Amplifiers
Type........................................................................Elmo Motion Control VIO 10/100
Peak current limit (2.7 s)........................................1.7–10 A (default 1.7 A)
Continuous current limit ........................................0.85–5 A (default 0.85 A)
DC-bus motor voltage............................................48 VDC
PWM frequency .....................................................32 kHz
Continuous power output rating
(all axes combined) ................................................400 W at 25% duty cycle
Encoders
Inputs .....................................................................Quadrature, incremental
Differential input threshold....................................± 0.3 V (typical)
Single ended input threshold..................................TTL/CMOS
Voltage range .........................................................0–5 VDC
Maximum quadrature frequency............................20 MHz