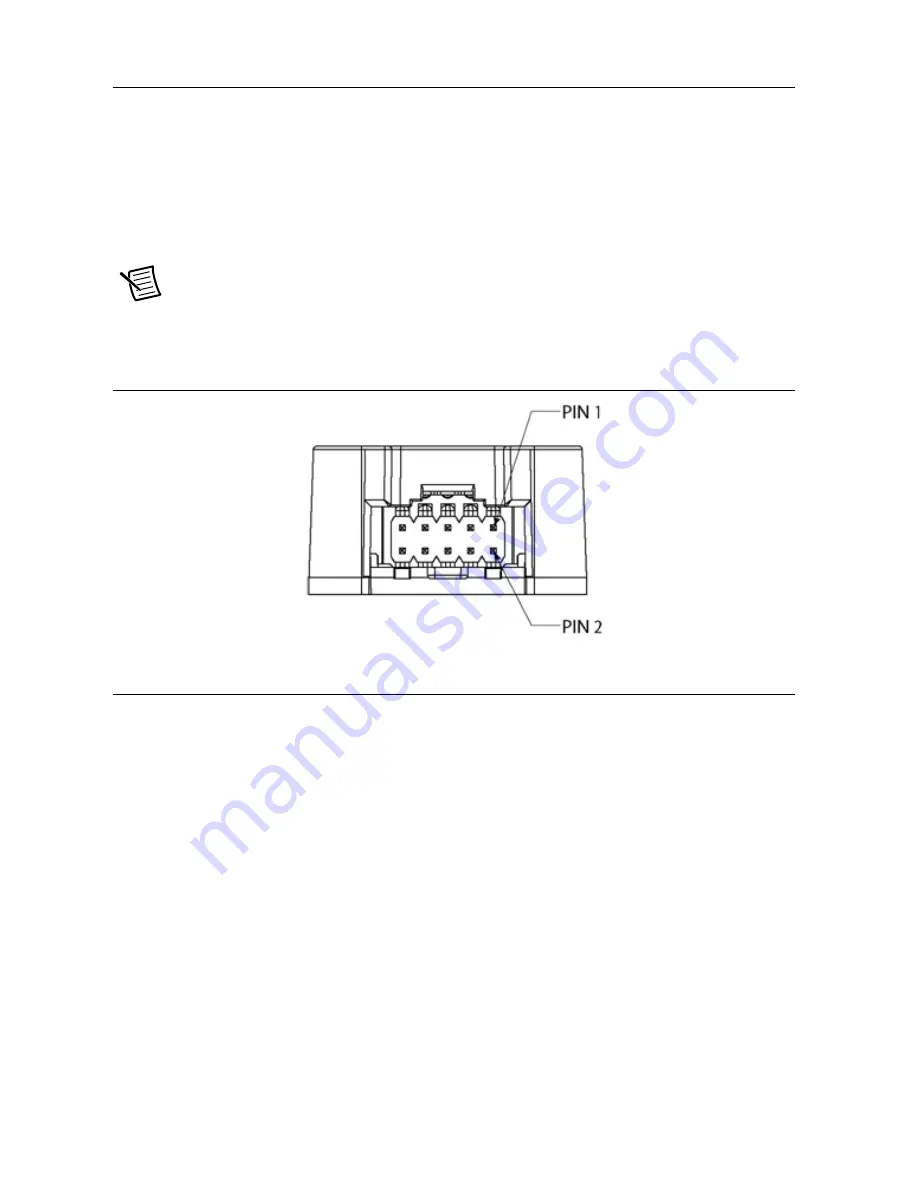
12
|
ni.com
|
NI ISM-7401/7402 User Manual
Using the Optional Encoder
There are three versions of the NI ISM-7401 and NI ISM-7402: the NI ISM-7401/7402 has a
single shaft, the ISM-7401D/7402D has a dual shaft, and the ISM-7401E/7402E has a dual shaft
with a 1000-line, incremental encoder assembled to the rear shaft of the unit. You can connect
the A, B, and Index (Z) channel signals of this encoder to the external controller for position
verification and enhanced performance, depending on the features of the controller. To facilitate
connecting the encoder signals to your external controller, you should purchase cable part
number 748995-01.
Note
If you are making your own cable to connect the encoder signals to your
controller, NI recommends using a shielded cable with four or five twisted pairs for
improved noise immunity.
Figure 16.
NI ISM-7401/7402 Encoder Connector
Configuring the NI ISM-7401/7402
Setting the Current
Set the current to 100% to achieve maximum torque. However, under some conditions you
might want to reduce the current to save power or lower motor temperature. This is important if
the motor is not mounted to a surface that will help it conduct heat away or if you expect the
ambient temperature to be high.
Step motors produce torque in direct proportion to current, but the amount of heat generated is
roughly proportional to the square of the current. If you operate the motor at 90% of rated
current, the motor provides 90% of the rated torque and approximately 81% as much heat. At
70% current, the torque is reduced to 70% and the heating to about 50%.