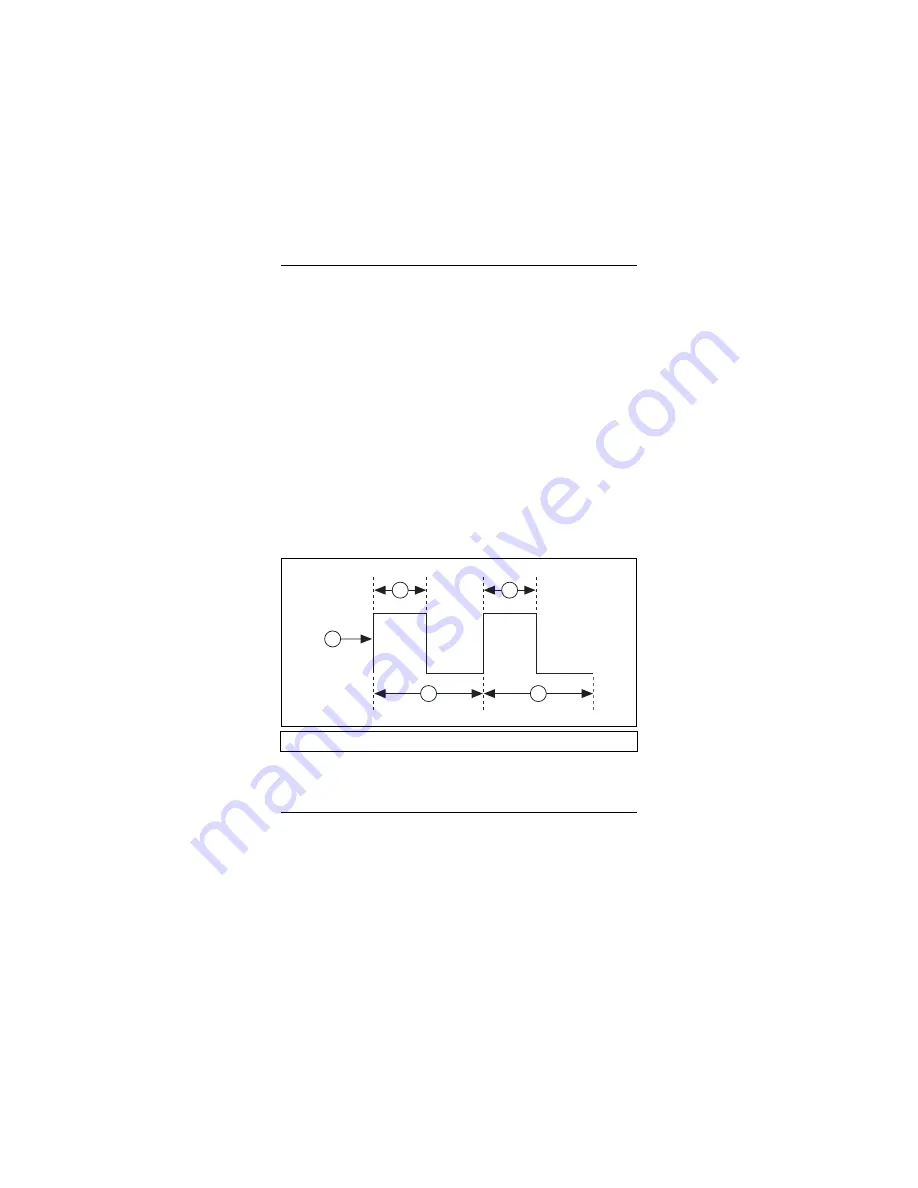
FP-PWM-520 and cFP-PWM-520
8
ni.com
Configuring the Output Channels
A [c]FP-PWM-520 output channel uses period and duty-cycle
settings to determine when the channel is on or off. To configure
the period, complete the following steps in Measurement &
Automation Explorer (MAX):
1. On the Channel Configuration tab for the [c]FP-PWM-520,
select
Period
from the Attribute menu.
2. Enter an integer between 1 ms (1 kHz) and 65,535 ms
(0.01525 Hz) in the Value field.
To configure the duty cycle, write to the channel for which you
want to set the duty cycle. The duty cycle is the proportion of time
that the PWM signal is ON over the period.
Enter a value from 0 to 100 to set the duty cycle. The duty cycle has
12-bit resolution (4,096 discrete duty-cycle settings).
Figure 4.
Period and Duty Cycle of a PWM Output
Status Indicators
The [c]FP-PWM-520 has two green status LEDs,
POWER
and
READY
. After you insert the FP-PWM-520 onto a terminal base
or the cFP-PWM-520 onto a backplane and apply power to the
connected network module, the green
POWER
indicator lights
and the [c]FP-PWM-520 informs the network module of its
presence. When the network module recognizes the
1
PWM Output
2
On Time
3
Period
Duty Cycle
OnTime
Period
---------------------
100
×
=
0
V
S
UP
1
3
2
2
3