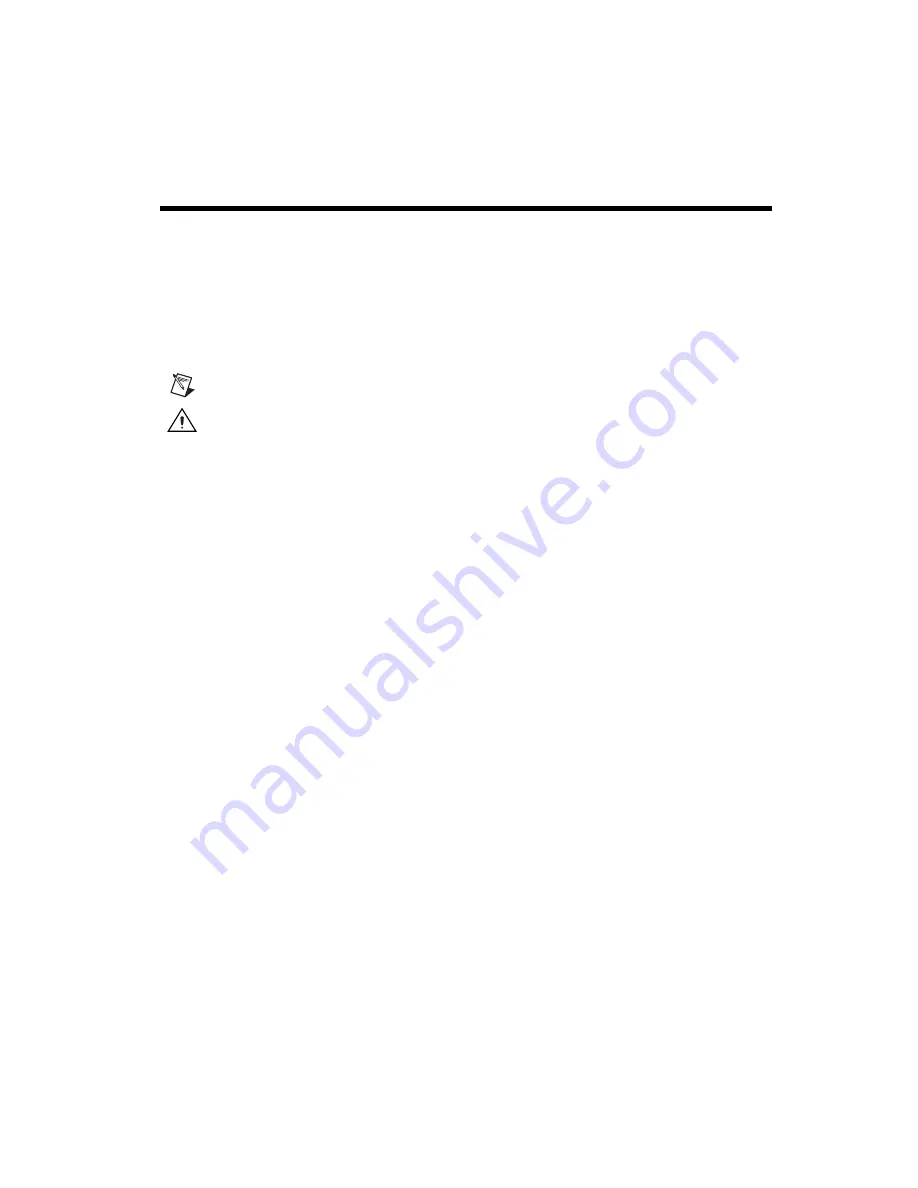
Conventions
The following conventions appear in this manual:
»
The
»
symbol leads you through nested menu items and dialog box options
to a final action. The sequence
File»Page Setup»Options
directs you to
pull down the
File
menu, select the
Page Setup
item, and select
Options
from the last dialog box.
This icon denotes a note, which alerts you to important information.
This icon denotes a caution, which advises you of precautions to take to
avoid injury, data loss, or a system crash. When this symbol is marked on
the product, refer to the
Read Me First: Safety and Radio-Frequency
Interference
document, shipped with the product, for precautions to take.
bold
Bold text denotes items that you must select or click in the software, such
as menu items and dialog box options. Bold text also denotes parameter
names and LED names.
cFP-21
xx
cFP-21
xx
refers to the cFP-2100, cFP-2110, and cFP-2120.
italic
Italic text denotes variables, emphasis, a cross reference, or an introduction
to a key concept. This font also denotes text that is a placeholder for a word
or value that you must supply.
monospace
Text in this font denotes text or characters that you should enter from the
keyboard, sections of code, programming examples, and syntax examples.
This font is also used for the proper names of disk drives, paths, directories,
programs, subprograms, subroutines, device names, functions, operations,
variables, filenames, and extensions.
monospace italic
Italic text in this font denotes text that is a placeholder for a word or value
that you must supply.