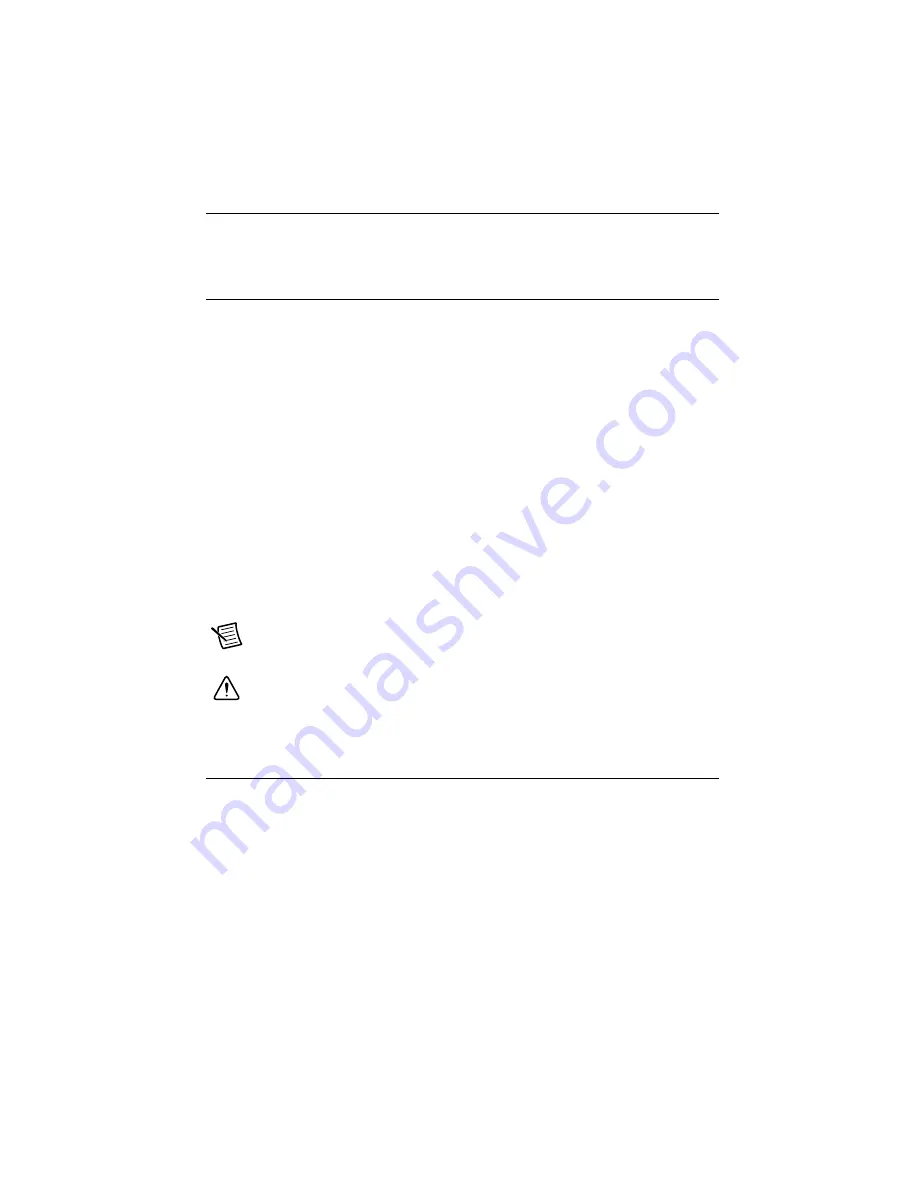
NI 9759 User Manual
|
© National Instruments
|
3
Hardware
The NI 9759 includes two H-Bridge drivers and analog position feedback in a NI CompactRIO
module.
Powering the Module
The NI 9759 requires power from two different sources, the CompactRIO backplane male high
density D-SUB 15-pin (HD15) connector and the external screw-terminal connector.
The HD15 connector mates with the module's female HD15 connector and provides a regulated
5 V and ground to various digital logic functions. The CompactRIO 5 V source is active
whenever the CompactRIO or R Series Expansion Chassis is properly powered. The module
should only be powered at the HD15 connector by plugging it into a CompactRIO or R Series
Expansion Chassis. The module's HD15 connector should not be connected to any other device.
The external screw-terminal connector has terminals labeled BATT (0) and GND (9). Typical
power sources will be from automotive 12 V or 24 V battery systems. The NI 9759 can accept
power from a range of 7 V to 32 V. Without throttles connected, the module requires a maximum
100 mA from the external supply. Driving a single throttle under full load requires a maximum
of 60 W peak and 30 W continuous. Driving two throttles at full load requires a maximum 120 W
peak and 60 W continuous.
The NI 9759 requires both external power and power from the CompactRIO backplane. The
NI 9759 directs the high current path through the BATT (0) and GND (9) terminals on the front
of the NI 9759 and not through the HD15 backplane connector.
Note
The NI 9759 will not be recognized by software without both power supplies
active.
Caution
The external battery supply input terminals are not reverse voltage
polarity protected. Connecting power to the NI 9759 in reverse polarity will cause
damage. This event is not covered by the warranty.
Platform Compatibility
NI Powertrain Control modules require a hardware support system to function. You cannot use
the modules independently or interfaced with third-party devices at the backplane HD15
connector. NI Powertrain Control modules are compatible with the following National
Instruments platforms:
•
CompactRIO, which consists of a CompactRIO controller, chassis, or integrated
controller/chassis.
•
NI PXI, which consists of any NI PXI chassis, NI PXI RT controller, and NI PXI-78
xx
R
R Series FPGA card. The NI Powertrain Control modules insert into an NI R Series
expansion chassis. Connect an NI R Series expansion chassis to the NI PXI FPGA card
using a SHC68-68-RDIO cable.