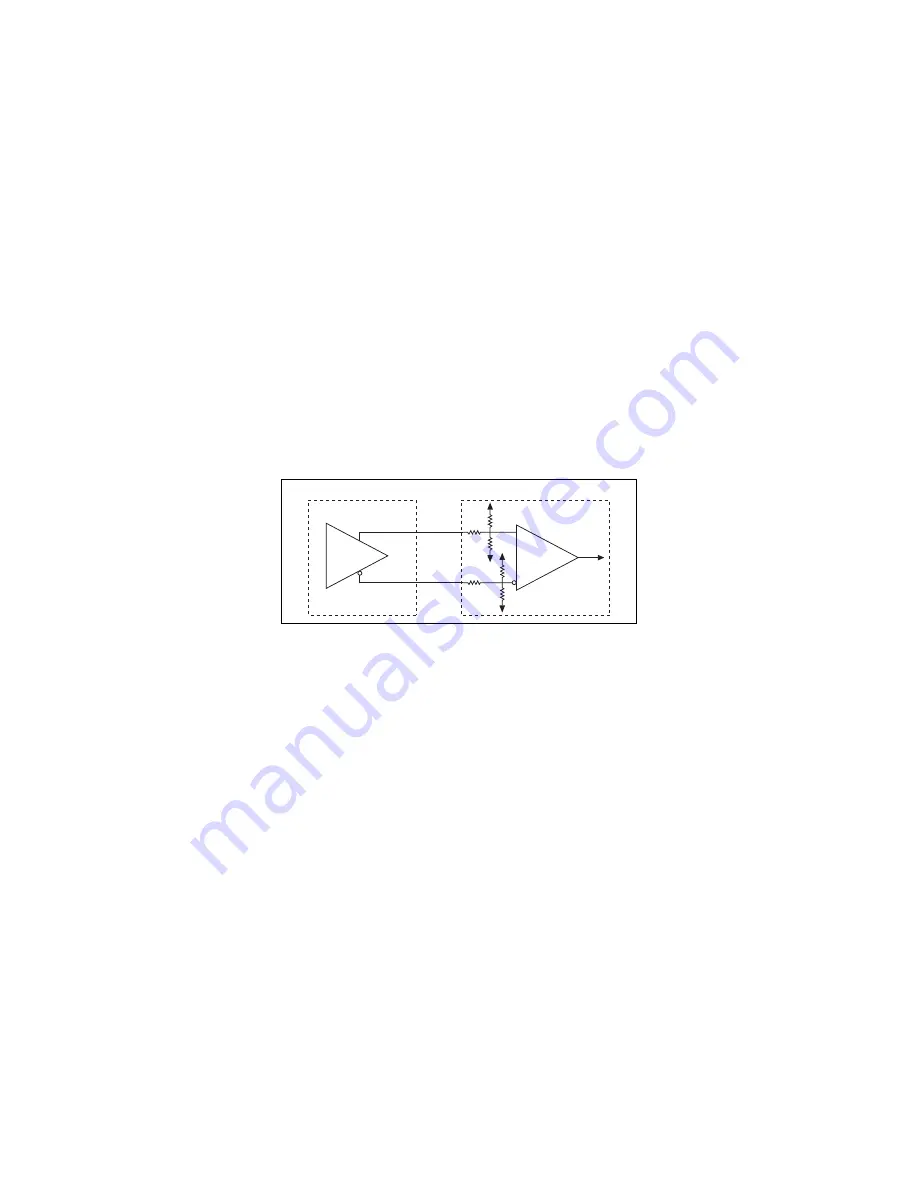
NI 9505E Operating Instructions and Specifications
18
ni.com
If the encoder cable length is greater than 3.05 m (10 ft), use
encoders with differential line driver outputs for your applications.
Power for a +5 V encoder—generated by a power supply on the
NI 9505E—is available on pin 5 of the DSUB connector.
Figure 8.
Differential Encoder Input Circuit
Receiver
Phase +
Phase –
Encoder
COM
COM
+5 V
+5 V
Encoder
NI 9505E