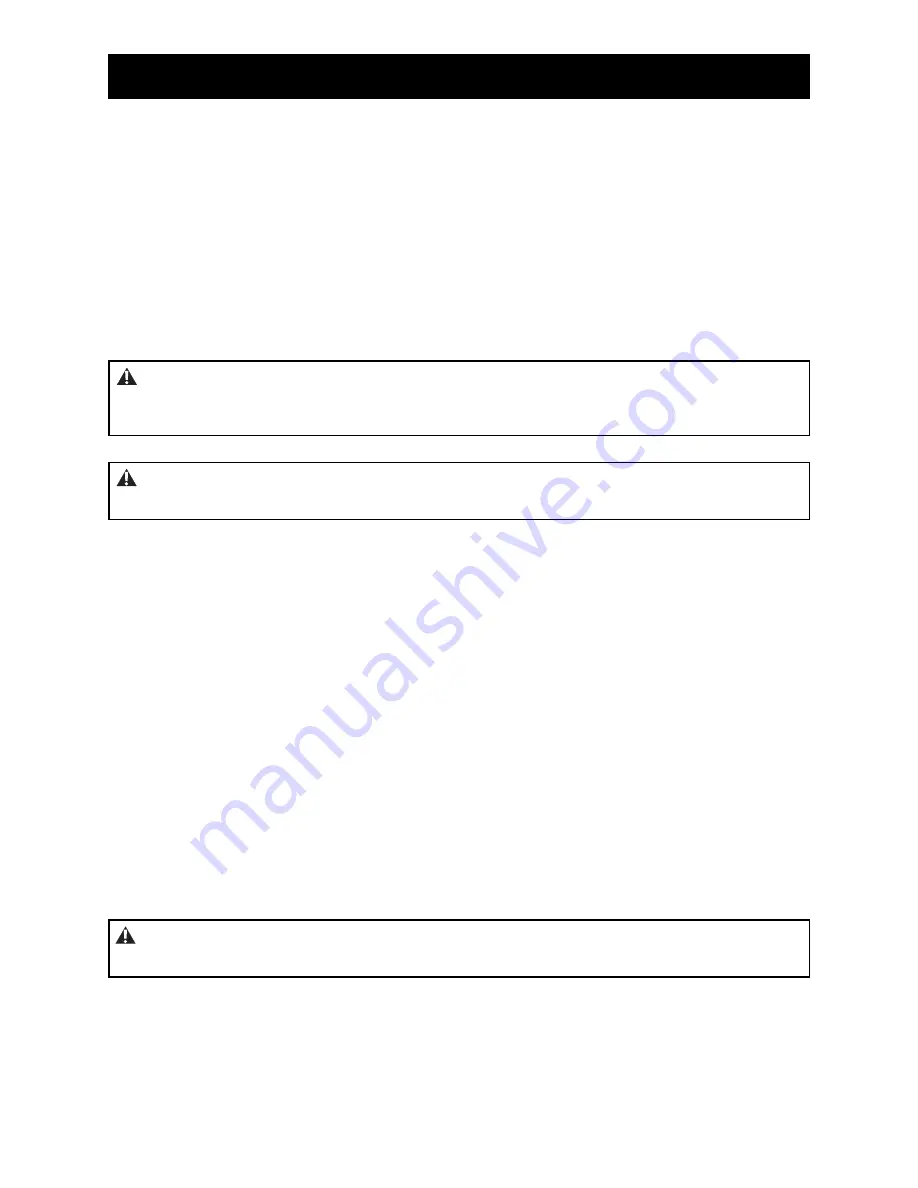
Page 4
5280 HYDRAULIC SAFE OPERATION
PRESSURE (continued)
2. Check the threads and/or seat angle for damage that may have occurred prior to or during
installation. Any ding or burr may be a potential leak path. Replace if necessary.
3. If the coupling was misaligned during installation, threads may have been damaged. Replace
and carefully install.
4. Overtorquing of a threaded connection can stretch and damage threads and mating seat
angles. Overtorquing can also damage the staking area of the nut. Undertorquing does not
allow proper sealing.
3. BURST:
Whether due to improper selection or damage, a ruptured hose can cause injury. If it bursts,
a worker can be burned, cut, injected or may slip and fall.
4. COUPLING BLOW-OFF:
If the assembly is not properly made or installed, the coupling could come
off and hit or spray a worker, possibly resulting in serious injury. Never operate machine without
guards.
FLAMMABILITY
With the exception of those comprised primarily of water, all hydraulic fluid is flammable when exposed to
the proper conditions (including many “fire-resistant” hydraulic fluids).
Leaking pressurized hydraulic fluids may develop a mist or fine spray that can flash or explode upon contact
with a cause of ignition. These explosions can be very severe and could result in serious injury or death.
Precautions should be taken to eliminate all ignition sources from contact with escaping fluids, sprays or
mists resulting from hydraulic failures. Sources of ignition could be electrical discharges (sparks), open
flames, extremely high temperatures, sparks caused by metal -to -metal contact, etc.
HYDRAULIC FLUID
Only use Texaco Rando 46 Hydraulic Oil or Compatible Fluid like IS032 (stock # 6280-1). Non-compatible
fluids could cause damage to unit or serious injury.
CAUTION:
Never check for leaks over hose or hydraulic connections. Instead, use a piece of
cardboard to locate a pressurized leak. For drips (low pressure leaks), use a rag to clean the area and
determine where the leak originates.
CAUTION:
Never touch a pressurized hose assembly. Shut down the hydraulic system before
checking hose temperature.
WARNING:
When using electric tools, always follow basic safety precautions to reduce the risk of
electric shock and personal injury.
Summary of Contents for PANTHER 5280
Page 38: ...Page 37 5280 MATERIAL SAFETY DATA...
Page 39: ...Page 38 5280 MATERIAL SAFETY DATA...
Page 40: ...Page 39 5280 MATERIAL SAFETY DATA...
Page 41: ...Page 40 5280 MATERIAL SAFETY DATA...
Page 42: ...Page 41 5280 MATERIAL SAFETY DATA...