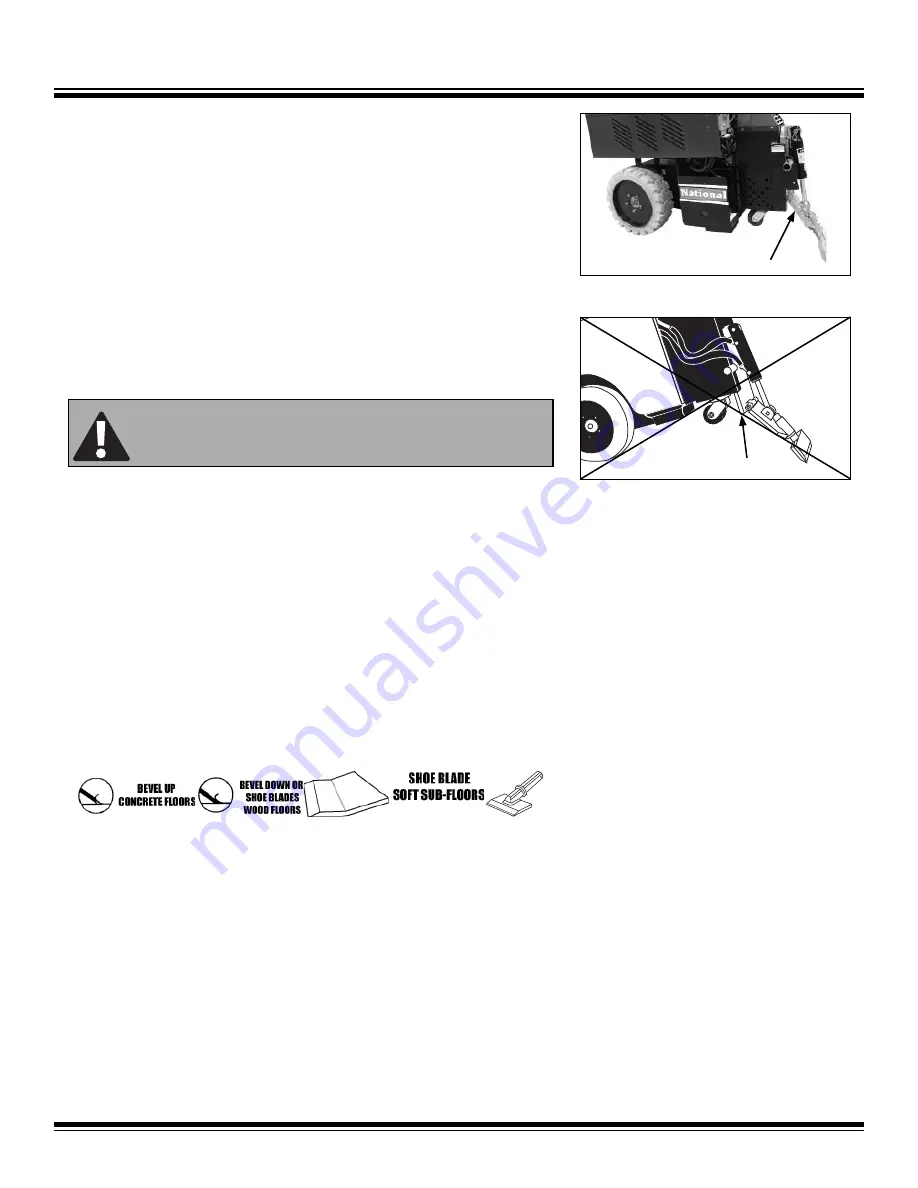
Machine Operation
www.nationalequipment.com
Phone: 763-315-5300
17
STEEP CUTTING HEAD ANGLE
A steep angle is only used for re-scraping. The slide plate has to be raised so the bottom
of the slide plate is higher or even with the bottom of the guide channels (See Figure
DD). Not raising the slide plate when operating the machine at a steep angle will cause
the machine to jump and buck. It does not give the operator a clear vision of the cutting
head and it raises the machine to operate at a unsafe operating height (See Figure EE).
Failure to raise the slide plate could cause machine damage and/or bodily injury.
SWIVEL HEAD
The swivel head keeps the blade in contact with the
fl
oor even when the
fl
oor is uneven.
When using a
fl
at blade, by swiveling the head over 180° allows another sharp edge on
the blade without having to replace the blade.
CUTTING HEAD INSERTION
With machine off, insert desired cutting head into cutting head holder. Secure with cutting
head clip.
SHANK BLADE INSERTION
Shank blades do not require a cutting head. Insert desired shank blade into cutting head
holder. Secure with cutting head clip.
BLADE SETTING
•
Dull blades greatly reduce cutting ability. Re-sharpen or replace as needed.
•
Proper blade size and placement, depending on material and sub-
fl
oor type, af-
fects performance.
•
The harder a job comes up, for best results, use a smaller blade.
•
Start with a narrow blade, then increase blade size to optimize cutting pass. Nar-
rower blades work easier than wider blades and usually clean the
fl
oor better.
Wider is not always better or faster.
•
Normally bevel on blade is up for concrete. Bevel down for wood and shoe blades
for soft sub-
fl
oors.
•
KEEP BLADES SHARP.
•
Dull blades greatly affect the performance of the machine and reduce cutting ability,
resharpen or replace as needed.
•
Keep your work area clean and clear of debris.
•
After you have removed a portion of material, remove it out of the way. This will give
the machine maximum performance and help to keep the work area safe.
•
Always wear gloves when handling blades.
•
Everyone in work area should wear eye protection.
SELF-SCORING BLADES
Instead of pre-scoring a job, for soft goods (carpet, vinyl, linoleum, membrane) the self-
scoring blades automatically do the scoring.
FIG. DD
FIG. EE
CAUTION:
WATCH OUT FOR OBSTRUCTIONS IN THE FLOOR (IE: EXPAN-
SION JOINTS, NAILS, BOLTS, RECEPTACLES). THEY WILL BREAK BLADES.
Slide Plate Is Not Raised
Slide Plate Is Raised
Summary of Contents for 5625
Page 2: ......
Page 50: ...Parts List and Diagrams Fax 763 535 8255 info nationalequipment com 50 5625 WIRING DIAGRAM...
Page 55: ...Fire Extinguisher MSDS www nationalequipment com Phone 763 315 5300 55...
Page 56: ...Fire Extinguisher MSDS Continued Fax 763 535 8255 info nationalequipment com 56...
Page 57: ...Fire Extinguisher MSDS Continued www nationalequipment com Phone 763 315 5300 57...
Page 58: ...Fire Extinguisher MSDS Continued Fax 763 535 8255 info nationalequipment com 58...
Page 59: ...Fire Extinguisher MSDS Continued www nationalequipment com Phone 763 315 5300 59...
Page 60: ...Fire Extinguisher MSDS Continued Fax 763 535 8255 info nationalequipment com 60...
Page 61: ...Fire Extinguisher MSDS Continued www nationalequipment com Phone 763 315 5300 61...
Page 62: ......