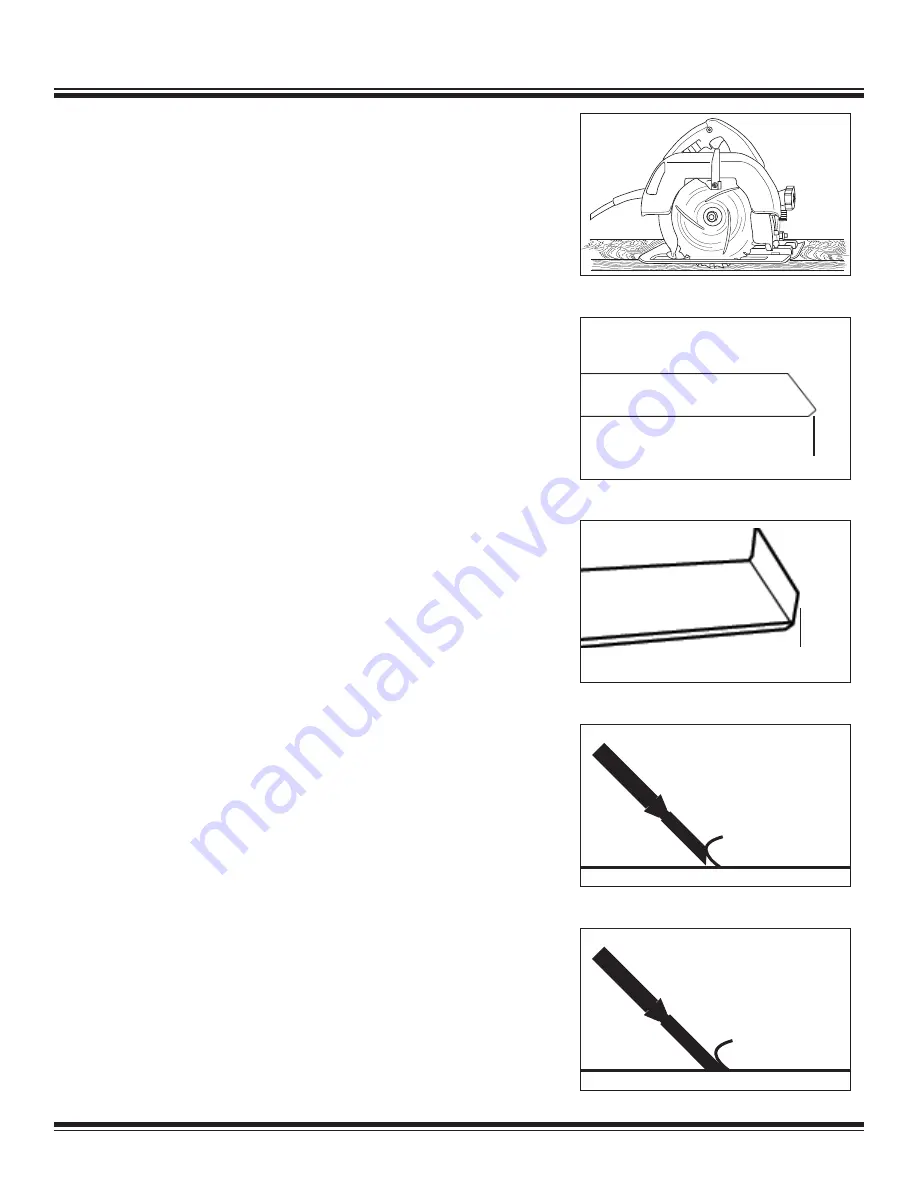
Machine Operation
www.nationalequipment.com
Phone: 763-315-5300
13
CONCRETE
When working on concrete slab, normal blade position is bevel up for best performance,
especially when cleaning adhesive. On occasion, bevel down gives better blade life. Test
each job for best performance.
GIBCRETE AND SOFT POURED FLOORING
Requires blade bevel down to create a better wearing surface.
HARD TO REMOVE SURFACES
Ripper teeth can be used on hard surfaces to remove material (hardwood & VCT).
GLUED HARDWOOD FLOORING
A 6” blade is recommended for regular adhesive. For proper removal of hardwood fl oor-
ing (parkay laminated, plank laminated, plank solid) fl ooring must be scored. This is done
by using a circular saw set at a depth of 100% of the thickness of the board, just missing
the subfl oor surface when on concrete. (See Figure P) A chalk line for scoring lines can
be used across the fl oor the width of the blade. A ripping guide attached to the saw can
be used to eliminate chalk line marks. Open an area large enough to fi t machine or start
from a doorway. It is important to keep all debris cleaned up for maximum performance of
machine. Ture parkay scoring will come up in small pieces so scoring is not necessary.
BLADE SHARPENING
Always check for blade sharpness before using; dull blades greatly reduce cutting ef-
fectiveness. Over time, used blades will develop a back bevel (Figure Q); when sharpen-
ing, blades will not recover until the back bevel is completely leveled out. NOTE: Thinner
blades are easier to sharpen, but they also break easier.
•
Always wear gloves and safety glasses.
•
Grind blade using a 4” diameter disk with 120 or fi ner grit. Be careful not to catch
disk on edge or corner of blade.
•
Pass grinder along blade edge starting on one end and continuing in one direction
being careful to hold grinder at proper angle of blade. Grind until sharp.
•
Using a high quality fi ne tooth hand fi le, follow the same procedure as above.
•
Blades are sharp. Use extreme caution.
•
Have plenty of sharp blades on each job so on-the-job blade sharpening is elimi-
nated.
•
It is best to re-sharpen dull blades on proper bench or belt grinder in the shop, so
the blades are ready for the next job.
SELF-SCORING BLADE SHARPENING
It is important to keep the “wings” on these self-scoring blades sharp. Use a fi le on the
edge. Sharpen the fl at part of the blade, the same way as described above.
CARBIDE TIPPED BLADE SHARPENING
To sharpen carbide tipped blades, a carbide grinding wheel is necessary, ie: silicon
carbide or green wheel.
FIG. C
FIG. D
FIG. E
BEVEL UP
BEVEL DOWN
Front of Blade
Back Bevel
Self-Scoring Wing
Front of Blade
Summary of Contents for 550
Page 1: ...Read Manual Before Operating Machine ADJUSTABLE HANDLE SCRAPER INSTRUCTION MANUAL 101713...
Page 2: ......
Page 26: ......