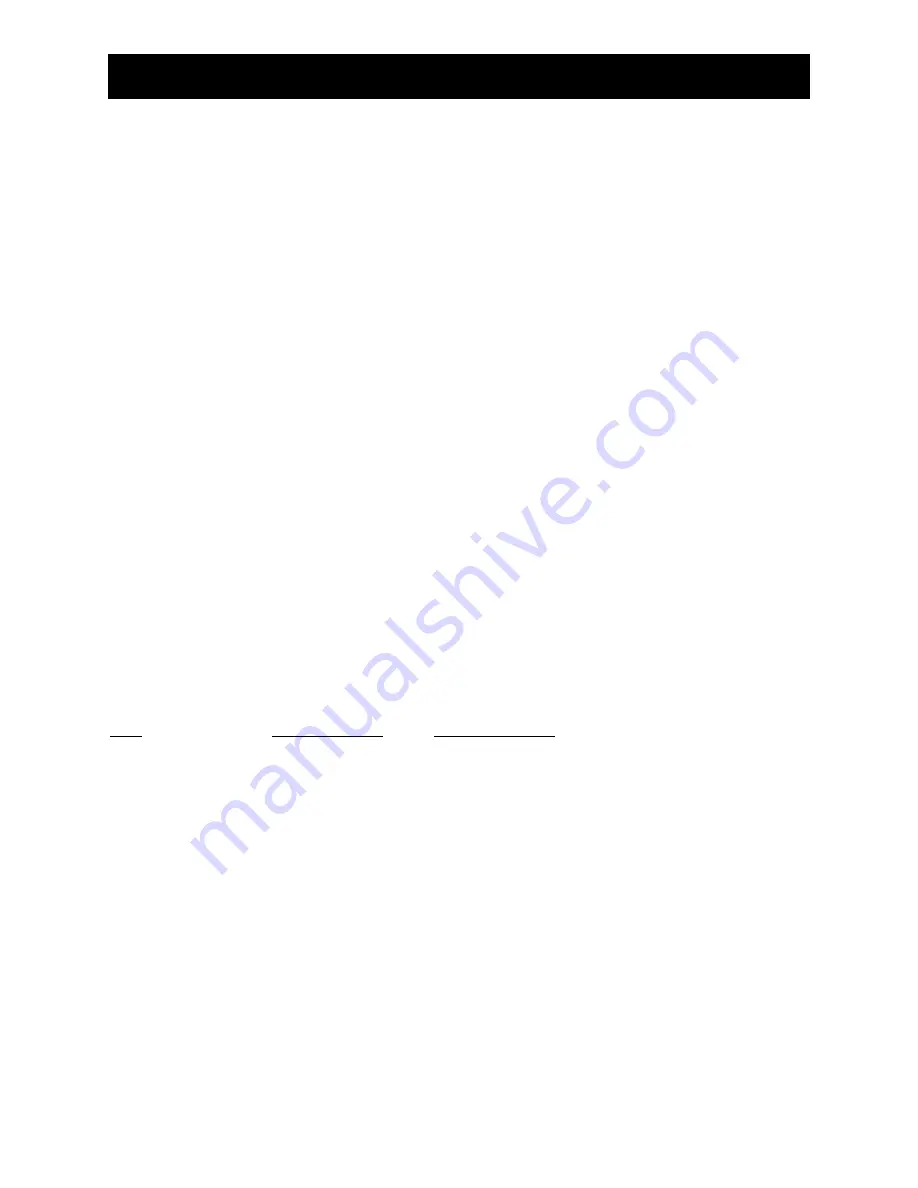
Page 14
PROCEDURE
SETTING THE BLAST PATTERN
Setting the proper blast pattern is determined by trial and error. The importance of selecting the proper
blast pattern can not be overstated. An improper or unevenly distributed blast pattern results in
excessive blasting on either the right or left side of the machine and leaves shadows or “track” lines in the
blast pattern.
When setting the blast pattern perform the following steps:
Verify the blast wheel is rotating in the direction shown on the blast housing. Place a sheet of steel
approximately 1/4" thick under the machine and blast with the shot valve fully open for approximately on
minute. Do not move the machine. After blasting for one minute shut down the machine and inspect the
blast pattern. The “hot spot” should be in the center of the width blasted. The “hot spot” can be altered
by rotating the control cage. Rotating the control cage in a
counter-clockwise
direction will move the “hot
spot” to the right while rotating the control cage in a
clockwise
direction will move the “hot spot” to the left.
If you visualize a clock, the opening of the control cage should be set at approximately 10:30 and 8:30 on
the clock. The size of the steel shot used will impact where the “hot spot” appears in the blast pattern.
The operator will need to adjust the control cage based upon the size of steel shot utilized.
WEAR PARTS
The #3390 contains parts which are continually exposed to steel shot moving at high rates of speed.
Exposure to steel shot traveling at high rates of speed and concrete dust cause these parts to deteriorate
thus they are known as
wear parts
. As a result, the operator or maintenance personnel should inspect
the #3390 wear parts prior to operation and change the parts as necessary. Wear parts and inspection
times, other than inspection prior to use, on the #3390 are listed as follows:
P
ART
W
HEN
TO
I
NSPECT
E
VIDENCE
OF
W
EAR
Shot Hopper
30 Hrs
Warping or Thin Spots
Feed Spout
50 Hrs
Thin Spots
Blast Wheel
10 Hrs
Blades Deteriorated > 40%
Control Cage
10 Hrs
Deteriorated Edges
Blast Wheel Hub
10 Hrs
Missing Pins/Deterioration
Liners
10 Hrs
Warping/Holes/Deterioration
Blast Housing
50 Hrs
Thin Section or other Deterioration
Parts of the #3390 which should also be inspected regularly but are not exposed to steel shot are the
control panel, motor, electric cords, dust collector hose, filters and
motors
. If any of these components
show signs of wear they should be repaired so that they are in the same working condition as when they
were new. If they cannot be repaired they should be replaced immediately.