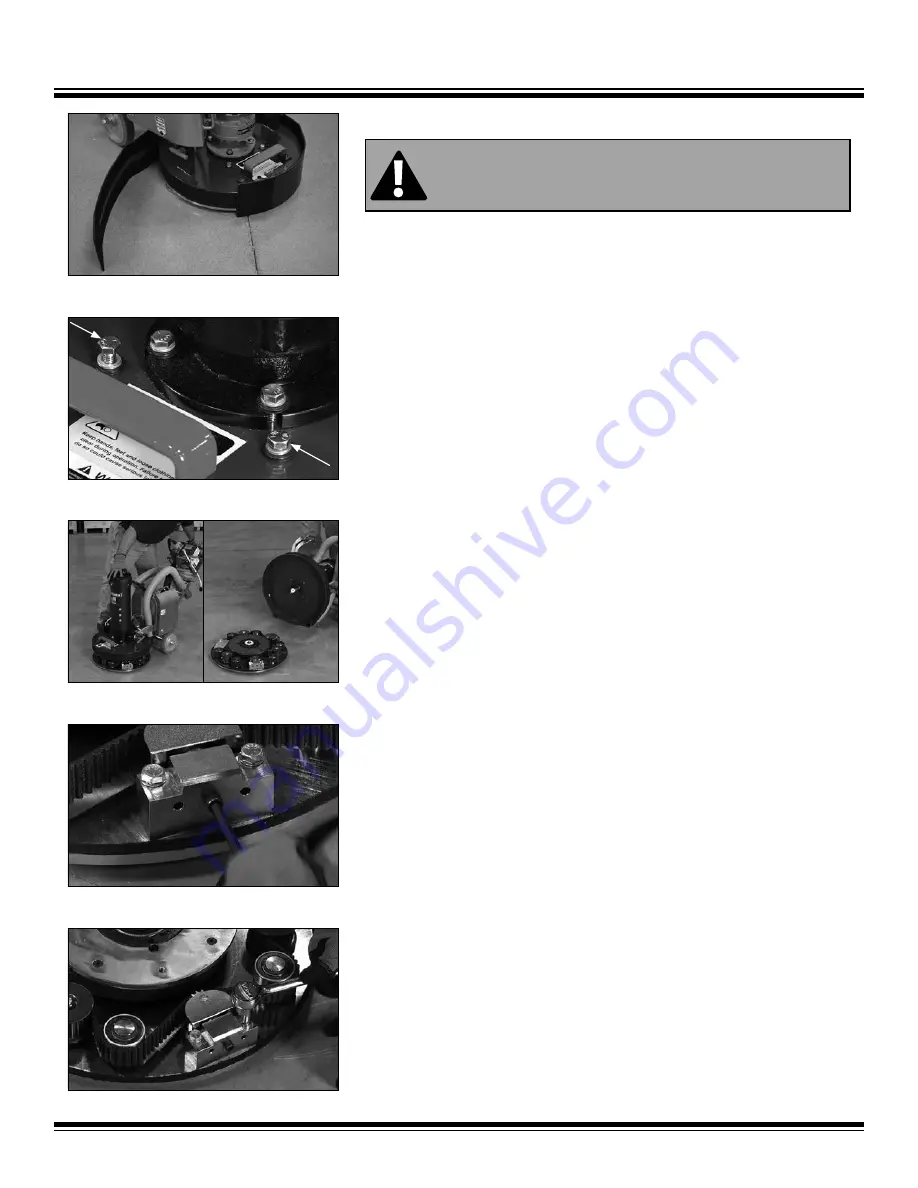
Maintenance
9
BELT PROCEDURES
Note:
Blue Loctite should be used on tensioner bolts. Torque on 3/8” bolts should not
exceed 25 lbs.
To Access Belt
1. Remove dust guard (Figure 1).
2. Remove the four bolts on top of the shroud cover (Figure 1.1).
3. Push down on the handle. The shroud should lift up and away from the grinding
deck. If not, with the four bolts on top of the shroud cover removed, tip the grinder
deck back to the tool changing position. Insert a 1/2”-13x4” threaded bolt into the
center of the underside of the deck plate. Turn bolt in clockwise until deck is free of
grinder shroud. Remove bolt and the shroud should now lift up and away from the
grinding deck (Figure 1.2).
4. Move machine back and off the plate (Figure 1.3).
Removing Belt
1. Remove any dust or debris from inside the deck.
2. Using an Allen wrench, install the 5/16-18x1 1/4” socket head cap screws into each
tensioner and compress the block spring by turning the screw clockwise. The belt
should be loose enough to slide off.
3. Leave approximately 1/8” gap when compressing the block spring to allow clear-
ance for removing the tensioner mounting bolts (Figure 2).
4. Remove one mounting bolt completely; loosen the other (Figure 3).
FIG. 1
FIG. 1.1
FIG. 1.2
FIG. 2
FIG. 3
CAUTION:
BEFORE ANY MAINTENANCE, MAKE SURE MACHINE IS DISCON-
NECTED FROM POWER SOURCE
FIG. 1.3
Summary of Contents for 8274-4
Page 1: ...Read Manual Before Servicing Machine 402973 Rev B 8274 4 PLANETARY GRINDER SERVICE MANUAL...
Page 2: ......
Page 18: ......