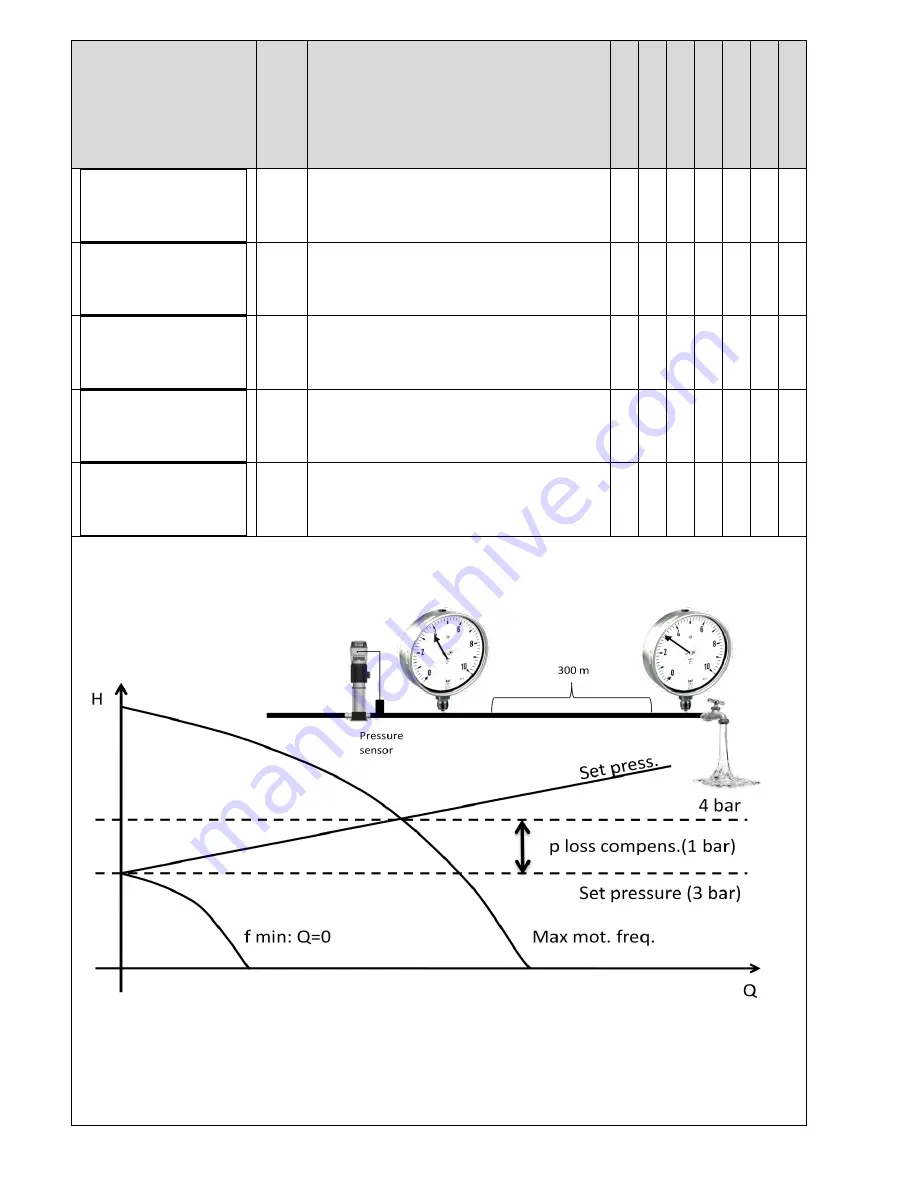
18
parameter
defa
ul
t
desciption
Co
n
stan
t
p
re
ss.
Fi
x sp
e
e
d
Co
n
st.p
re
ss.
2v
al
Fi
x sp
e
e
d
2
val
.
Exte
rn
al
sp
e
e
d
Co
n
stan
t
te
m
p
.
Co
n
stan
t
fl
o
w
3
The pressure value to be kept constant.
0
Pressure compensation at the maximum
frequency for each pump. Acting on the green
button you can reverse the sign.
3
The pressure value to be kept constant.
0
Pressure compensation at the maximum
frequency for each pump. Acting on the green
button you can reverse the sign.
5
Time to update p set for losses compensation.
To ensure proper operation of pressure control is recommended to place the sensor near the pump.
To compensate the pressure loss in the pipes (proportional to flow) it is possible to vary the pressure set in a linear relation
with respect to frequency. If Q = 0, Set pressure is granted while at the max output frequency will be granted the
Set pressure
+ p loss compens.
It can perform the following test to verify the correct value of p loss compensation:
1. install a pressure gauge away from the pressure sensor
2. open completely the valve
3. check the pressure gauge
--> Set the value of
p loss compens
. equal to the difference of the values from the two gauges.
When using a group of pumps, the pressure compensation to be applied to each pump is equal to the total pressure
compensation (when all the pumps are running at full speed) divided by the number of pumps in the group.
Press. set update
t = XX [s]
p loss compens. 2
p = XX.X [bar]
Set pressure 2
p = XX.X [bar]
p loss compens.
p = XX.X [bar]
Set pressure
p = XX.X [bar]