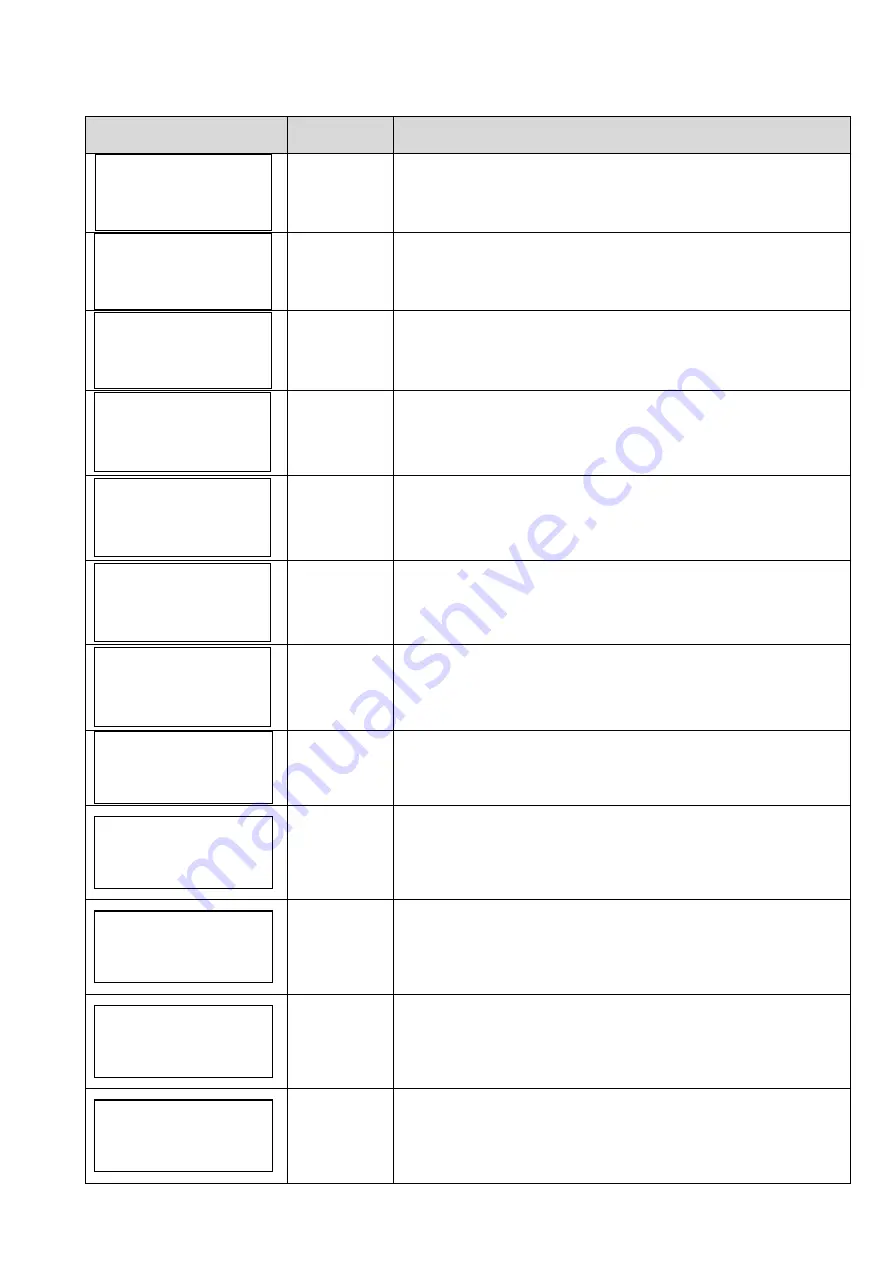
31
6.7 IN/OUT parameters
Parameter
Default
Description
bar
Unit [bar,%,ft,in,cm,m,K,F,C,gpm,l/min,m3/h,atm,psi]
16
Sensor full scale.
0
Sensor minimum value.
20%
Zero correction for analog input 1 (4-20 mA)
(20 mA x 20% = 4 mA).
20%
Zero correction for analog input 2 (4-20 mA)
(20 mA x 20% = 4 mA).
0%
Zero correction for analog input 3 (0-10V)
(10V x 00% = 0 V).
0%
Zero correction for analog input 4 (0-10V)
(10V x 00% = 0 V).
Independent
Function logic for analog input AN1,AN2 (independent, lower value,
higher value, difference 1-2).
N.O.
By selecting N.O. (normally open) the unit runs the motor if the digital
input 1 is open; motor will be stopped if the digital input 1 is closed.
By selecting N.C. (normally closed) the unit runs the motor if the digital
input 1 is closed; motor will be stopped if the digital input 1 is opened.
N.O.
By selecting N.O. (normally open) the unit runs the motor if the digital
input 2 is open; motor will be stopped if the digital input 2 is closed.
By selecting N.C. (normally closed) the unit runs the motor if the digital
input 2 is closed; motor will be stopped if the digital input 2 is opened.
N.O.
By selecting N.O. (normally open) the unit runs the motor if the digital
input 3 is open; motor will be stopped if the digital input 3 is closed.
By selecting N.C. (normally closed) the unit runs the motor if the digital
input 3 is closed; motor will be stopped if the digital input 3 is opened.
N.O.
By selecting N.O. (normally open) the unit runs the motor if the digital
input 4 is open; motor will be stopped if the digital input 4 is closed.
By selecting N.C. (normally closed) the unit runs the motor if the digital
input 4 is closed; motor will be stopped if the digital input 4 is opened.
Unit
XXXXX
F. scale sensor
XXX.X
Min.value sensor
XXX.X
Offset input 1
[%]
Offset input 2
[%]
Offset input 3
[%]
Offset input 4
[%]
AN1,AN2 function
XXXXXX
Digital input 1
N.O. / N.C
.
Digital input 2
N.O. / N.C.
Digital input 3
N.O. / N.C
.
Digital input 4
N.O. / N.C.
Summary of Contents for Vasco V209
Page 1: ...VAriable Speed COntroller Operating manual manVASCO_eng_31 ...
Page 42: ...42 NOTE ...
Page 43: ...43 ...