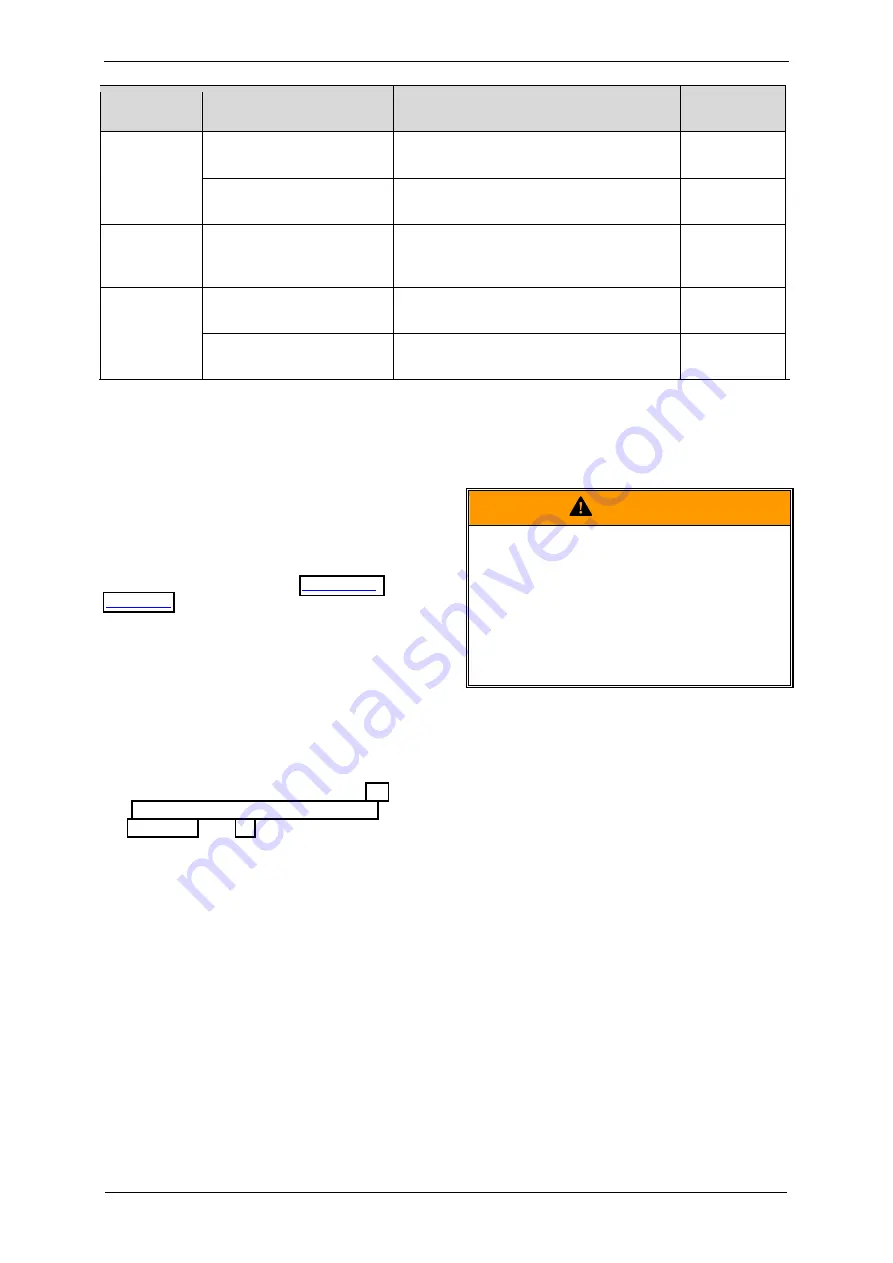
nash_elmo Industries GmbH
22 / 23
Order No.: 610.44436.40.000
Subject to change
Edition 09/2003
Disposal
Fault
Cause
Remedy
Carried out
by
Flow speed too high.
Clean pipes. Use pipe with larger cross-
section if necessary.
Operator
Abnormal
flow noises.
Muffler soiled.
Clean muffler inserts, check condition and
replace if necessary.
Service*)
Abnormal
running
noise.
Ball bearing lacking grease
or defective.
Regrease or replace ball bearing.
Service*)
Seals on muffler defective.
Check muffler seals and replace if
necessary.
Service*)
Compressor
leaky.
Seals in motor area
defective.
Check motor seals and replace if
necessary.
Service
*) Only when the maintenance manual is at hand: rectification by the operator.
9.2 Service/After-sales
service
Our Service is available for work (in particular
the installation of spare parts, as well as
maintenance and repair work), not described in
these operating instruction.
A list of spare parts with an exploded drawing
is available on the Internet at
Observe the following when
returning
pump-
motor unit:
•
The pump-motor unit must be delivered
complete, i.e. not dismantled.
•
The pump-motor unit may not present a
danger to the workshop personnel.
If the pump-motor unit has come into
contact with dangerous substances, then
the procedure described in Chapter 9.3,
"Decontamination and Declaration of
Clearance", Pg. 22, must be used.
•
The original rating plate of the pump-motor
unit must be properly mounted, intact and
legible.
All warranty claims are voided for pump-
motor units delivered for a damage
expertise without the original rating plate or
with a destroyed original rating plate.
•
In case of warranty claims, the
manufacturer must be informed of the
operating conditions, operating duration etc.
and additional detailed information provided
on request if necessary.
9.3
Decontamination and Declaration of
Clearance
WARNING
Danger from flammable, caustic or toxic
substances!
To protect the environment and persons, the
following applies:
Pump-motor unit which have come into contact
with
dangerous substances
must always be
decontaminated before being passed on to a
workshop!
To provide proof that the decontamination was
carried out, a so-called
declaration of
clearance
must be included with the pump-
motor unit on delivery to the workshop.
The form required for this purpose is available
from the Service Department.
10 Disposal
Have the entire pump-motor unit scrapped by a
suitable disposal company. No special
measures are required when doing so.
For additional information on disposing of the
unit, ask the Service Department.
11 Explosion-Protected Design
An additional set of operating instructions with
supplementary or specific information is
provided with these pump-motor units.