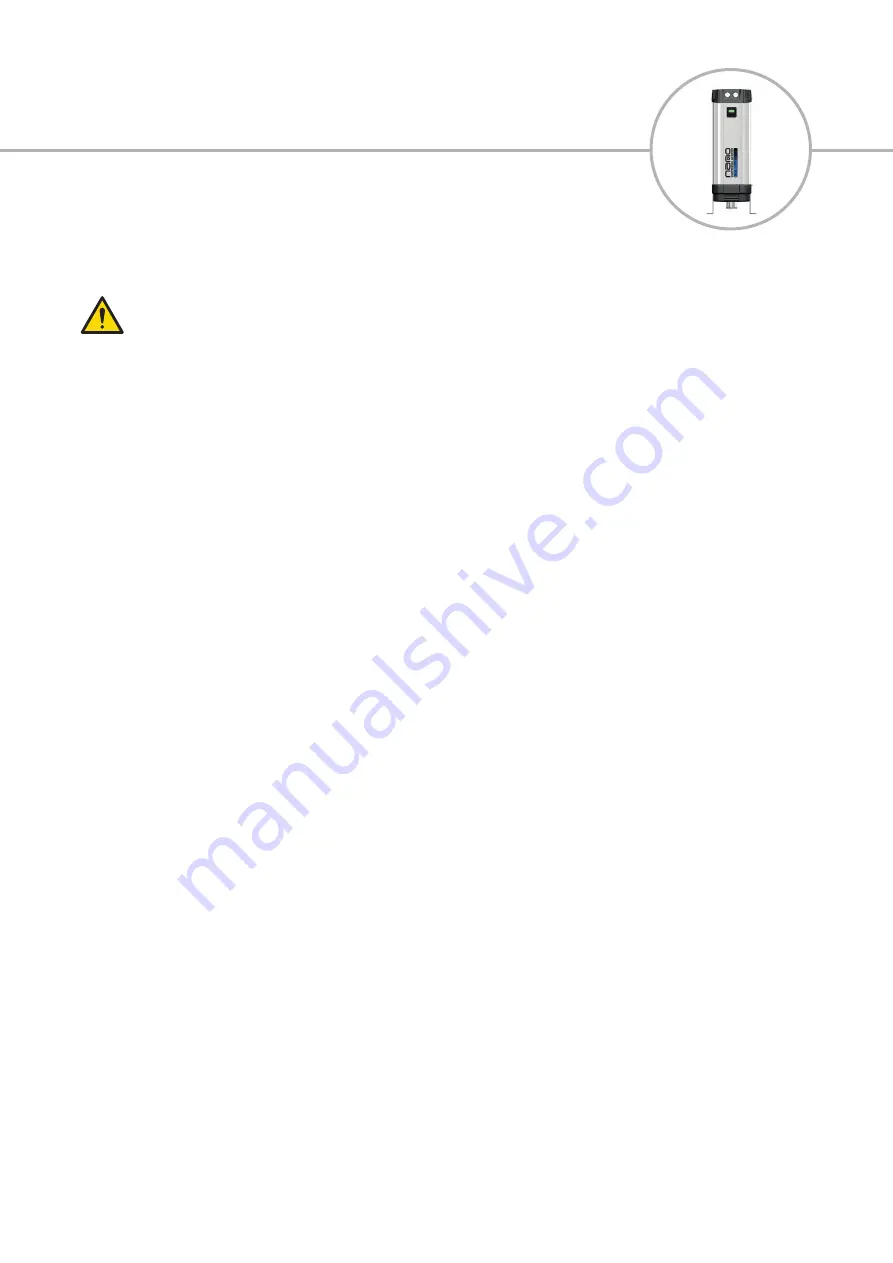
17
heatless desiccant air dryer
D2
3.1 maintenance
Maintenance operations should only be conducted once the system has been shut down and is fully
depressurized. All operations should be carried out by authorized and suitably trained personnel
•
Isolate the unit from the compressed air and electrical supply ensuring the system is in a safe condition for maintenance to be
carried out.
•
All connections must be removed with care, paying particular attention to the areas that become pressurized.
•
All seals removed during maintenance operations must be replaced with new seals.
•
Only certified and approved replacement parts should be used.
•
Do not modify or adjust the control settings.
•
Check all connections and sealing faces for cleanliness and secure seating prior to assembly.
•
Ensure all components are re-fitted to the product before operation.
•
Check all connection and sealing faces for any leakage, if any found resolve and check again.
•
Ensure the unit is left operating in a safe working condition after completion of maintenance
3.2 cleaning
Clean the equipment with a damp cloth only and avoid excessive moisture around any electrical connections.
If required a mild detergant can be used. Do not use abrasives/solvents as these may cause damage.
3.3 daily checks
•
Check the unit for any signs of external damage.
•
If the red service indicator is active, the unit must be serviced to ensure continued operation.
•
Remove any loose dust or dirt from the unit, clean all surfaces that appear to have attracted unwanted contaminants.
•
Ensure the unit is operating within the specification.
•
Always check all connections for any leaks.
•
Ensure all loose parts are removed or secured to the unit before operation.