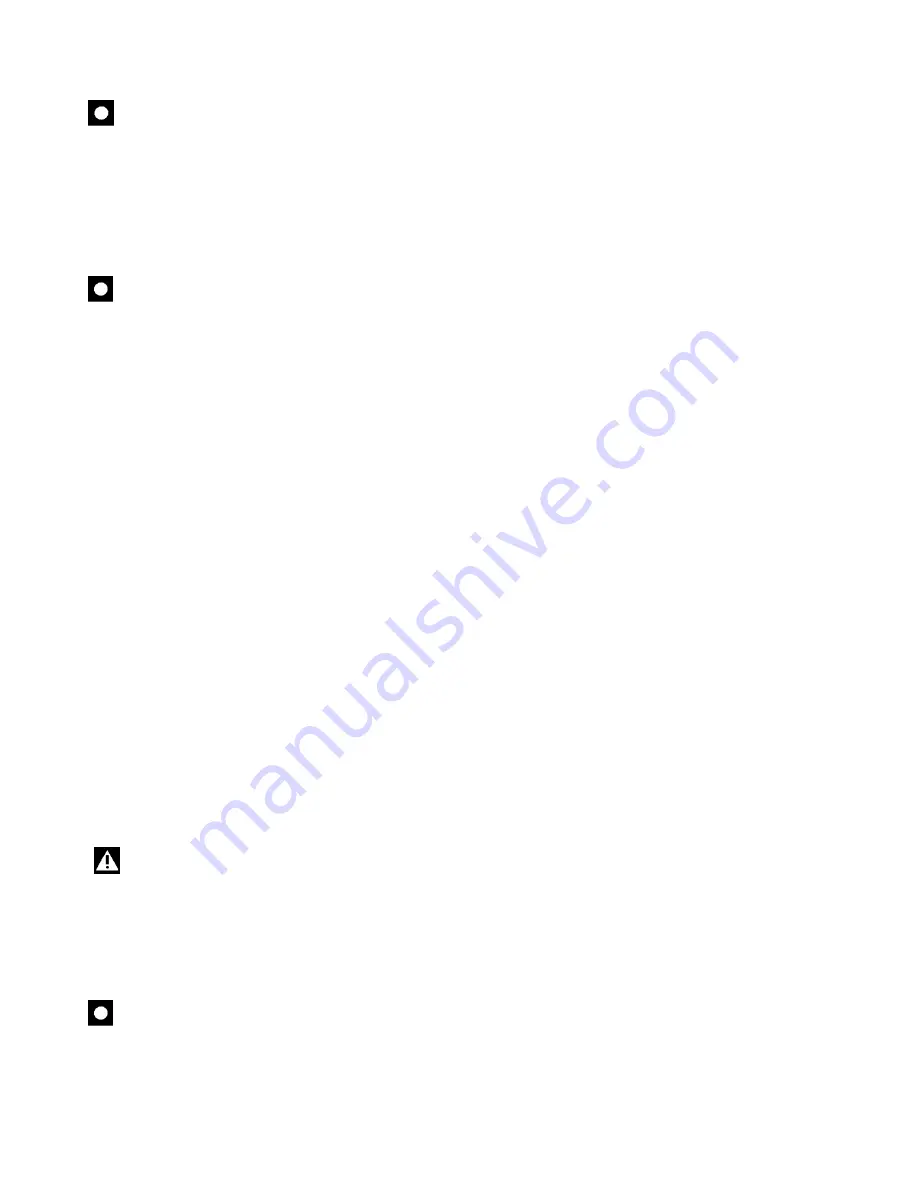
11
Important:
The machine was constructed for the preparation of welded surfaces. Machining
accuracy is within limit
+/-1mm. The condition for reaching the satisfactory results is a perfect
preparation of the material edges. Unfortunately the material is often burned or
cut. The inaccuracy shall be reflected on the resulting machining.
Important:
If it is difficult to machine the bevel within the recommended number of steps,
we recommend dividing the process to more chips. The reason can be the wear of
the cutting inserts or worse machining properties of material.
11.2
Bevelling
Connect the device in electricity distribution
After careful setting of the first reduction, see clause 11.1, hold the device with
both hands and use the main switch to switch on the device.
Fit the machine on material in such way the thrust/contact plate (fig. 10.0.1 position
G) was in contact with material at maximum possible surface.
Slowly move the machine to the material until you feel the milling machine is in
reduction. CAUTION!!! The rebound is possible at this moment, be careful.
Press the machine in the direction into the material until the miller is embedded in
the material in the full profile of the set chip. Contact roller (fig. 10.0.1 position E)
must now touch the workpiece edge. The thrust plate (fig. 10.0.1 position G) must be
placed with the surface on material.
Now, you can start the machining from the left to the right. Shift the machine
constantly; using only such speed the milling machine was able to remove material
in the set chip profile. Otherwise, the milling machine will be pushed out from the
material and the bevel will be unequal.
Attention :
During work, wear gloves and other personal protective equipment.
The maintenance operations must be carried out on the machine at rest and after
disconnecting from the power supply.
Important:
The shift during machining is always from left to the right.