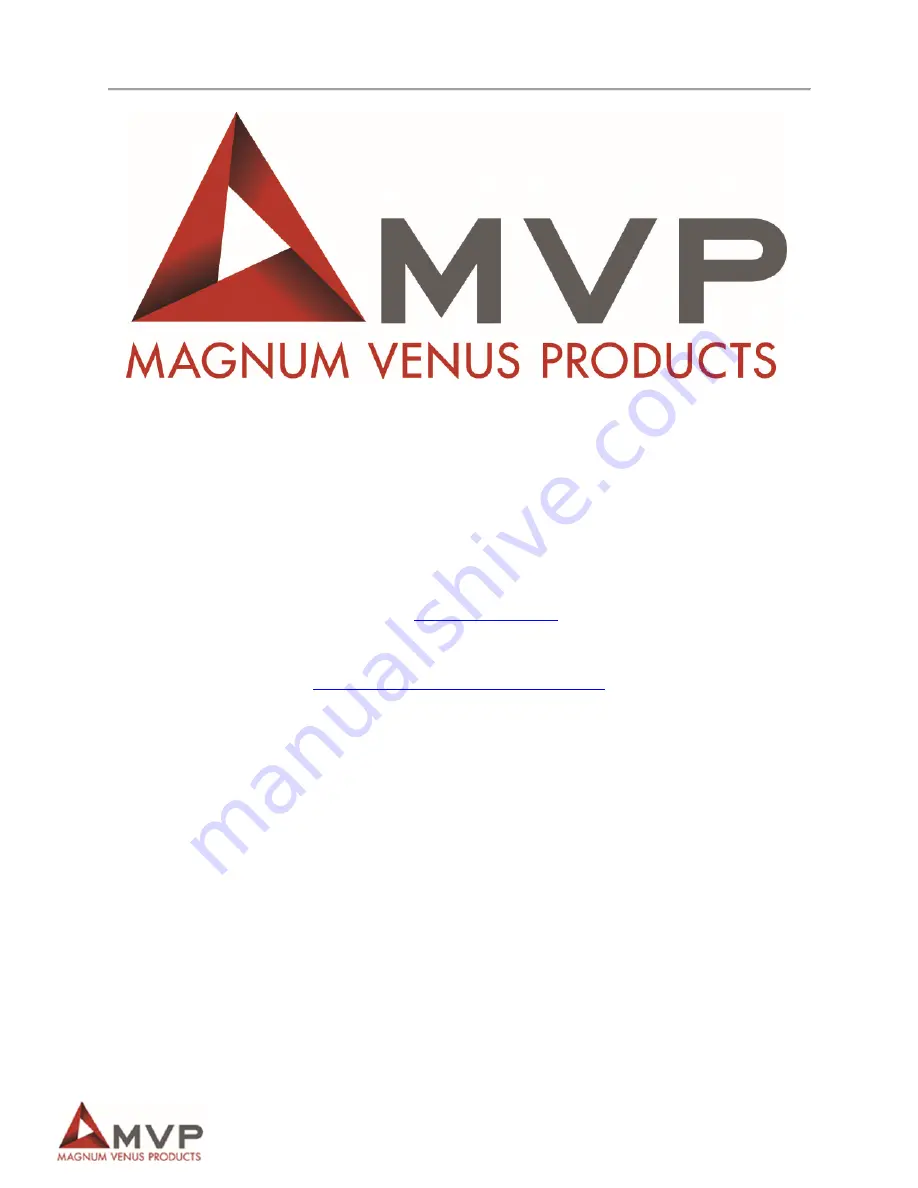
Innovator Plus System Operations Manual
Page | 2
C
ORPORATE
H
EADQUARTERS
2030 Falling Waters Rd, Suite 350, Knoxville, TN 37922 · USA · Tel: (865) 686-5670
D
ISTRIBUTION AND
P
URCHASING
642 Barbrow Ln, Knoxville, TN 37932 · USA · Tel: (865) 684-4416
T
ECHNOLOGY
C
ENTER AND
M
ANUFACTURING
1862 Ives Ave, Kent, WA 98032 · USA · Tel (253) 854-2660 · Fax (253) 854-1666
E-mail:
For a list of international distributors, visit our website at :
www.mvpind.com/mvp-international
Use of this product confirms that Magnum Venus Products, Inc.’s standard terms and
conditions of sale apply.