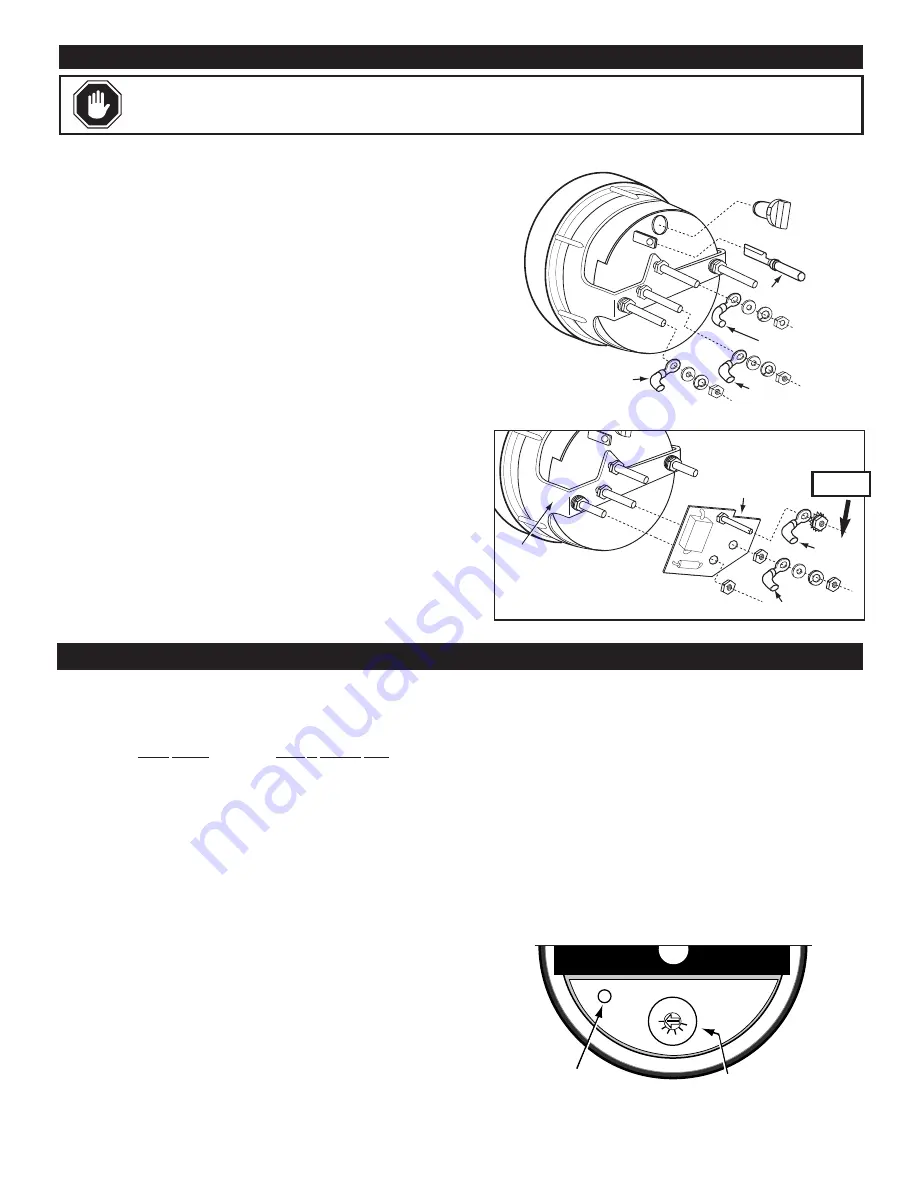
TAH-97029N (0258) page 3 of 5
Typical Wiring For ATA And ATHA Series Models
Connecting or Replacing Light Bulb
1.
Twist the “light assembly” socket one-eight turn counterclockwise and remove the “light
assembly”. See Fig. 4 at right.
2.
To replace the bulb, pull the bulb from the socket and replace with an 00-00-4617 (for
12V), 00-00-4618 (for 24V) bulb or equivalent size as marked on the bulb.
3.
Connect the lamp blade connector to (+) positive side of instrument lighting circuit.
Connecting to Alternator
(
see Fig. 4)
1.
Connect a wire from “SIG” terminal an AC phase terminal (sometimes marked “STA”
or “R”) on your alternator. If your alternator does not have an AC phase terminal, sol-
der the “SIG” wire to one of the negative or positive rectifier diodes of the alternator.
2.
After soldering, securely tape the wire to an alternator lead or wiring harness to damper
vibration on diode terminal.
NOTE:
On some alternators it may be necessary to remove
the rear housing to solder the wire to the diode.
Connecting to Ignition
(
see Fig. 4)
1.
Connect a wire from “SIG” terminal to the negative “-” side of the igniton coil or to the
terminal marked “TACH” on solid-state ignition systems.
Connecting to Power
(
see Fig. 4)
Important:
These units are for 12 VDC only.
1.
Connect a wire from “BAT” to a 12 VDC circuit activated by the ignition switch.
2.
Connect a wire from “GND” to negative voltage source (electrical ground).
Connecting ATVC12/24 Convertor
(
see Fig. 5)
For 24 VDC applications, a ATVC12/24 convertor must be used.
1.
Insert the ATVC12/24 convertor as shown.
2.
Secure the ATVC12/24 convertor with a nut on the “BAT” and “GND”stud terminals of
the Tachometer.
3.
Notice that the stud terminal on the ATVC12/24 convertor becomes the “BAT” stud for
connecting to 24 VDC. Proceed with the connection as shown.
4.
Replace the 12 V bulb with the 24 V bulb supplied with the converter assembly.
Calibration Instructions
Calibration for ATS and ATHS models
The ATS and ATHS Series models have been designed to function with flywheels
having anywhere from 70 to 225 teeth. This wide range is divided into 6 switched
positions acting as a “coarse adjustment” as follows:
Switch Position
Range of Flywheel Teeth
1
70 - 80 teeth
2
81 - 100 teeth
3
101 - 130 teeth
4
131 - 160 teeth
5
161 - 190 teeth
6
191 - 225 teeth
1.
If the number of teeth on the flywheel is known, set the calibration “course
adjustment switch”, (see Fig. 6, at right), using a fine blade slotted head screw-
driver to the applicable position per chart above.
2.
If the number of teeth on the flywheel is not known, set up a calibrated “shop
tach” to monitor the engine’s true RPM. Start the engine and after an appropriate
warm-up period increase to normal running RPM as read on the shop tach. If the
course switch was not set in step 1, set it now to the position that causes the
Murphy tach to read closest to true RPM.
*
*
Some engines incorporate a governor that limits full throttle RPM to pre-set
level equal to the engine’s recommended maximum running speed. If your
engine has such a governor, and if the governed full throttle RPM is known (it
should be clearly stated on the engine’s certification documentation), use of a
calibrated shop tach is not necessary. Simply run the engine up to governed
maximum running RPM and calibrate the Murphy tach to the rated RPM as
specified in the engine’s certification documentation.
W
WA
AR
RN
NIIN
NG
G::
Make sure that the engine has a properly functioning
and certified governor before attempting this alternate procedure.
Fine Adjustment for ATS and ATHS models
The “fine adjustment” of calibration is accomplished by varying the calibration
Trimpot located behind the “fine adjustment” access hole on the rear of the case,
(see Fig. 6, below). Proceed with calibration as follows:
1.
To adjust the trimpot for accurate RPM, punch through the label and insert a
1/16 x 1-3/4 in. flat blade Screwdriver (Sears item #00941659000/Mfr. model
#504-062C) or a #000 phillips screwdriver through the access hole and into the
fine adjustment trim pot.
*Note it is typically necessary to rotate the screwdriver to locate the trim pot slot orientation.
2.
Rotate the trimpot clockwise or counterclockwise as necessary.
3.
Once calibration at the engine’s normal running RPM has been set, the tach will
simultaneously be calibrated at all other engine speeds.
CAUTION:
Disconnect the battery/power source and determine voltage and polarity of the application before wiring
the unit. Use the appropriate wire size. It is recommended using 16 AWG (1.5 mm
2
) or larger stranded, insulated wire and
insulated crimp-on (solderless) ring-type wire terminals. Allow a few inches of excess wire to make adjustments.
TO LIGHT (+) CIRCUIT
LIGHT
ASSEMBLY
TO GROUND (-)
TO ALTERNATOR
SIG
GND
BAT
CAUTION:
TO 12 VDC ONLY
SIG
GND
BAT
TO GROUND (-)
MOUNTING
BRACKET
TO 24 VDC
ATVC12/24
CONVERTER
F
Fiig
g.. 4
4
F
Fiig
g.. 5
5
F
Fiig
g.. 6
6
BAT
Coarse
Adjustment Switch
Fine Adjustment
Trimpot Access
5
6
4
3
2
1
Tach Back View
(under label)
N
NO
OT
TE
E