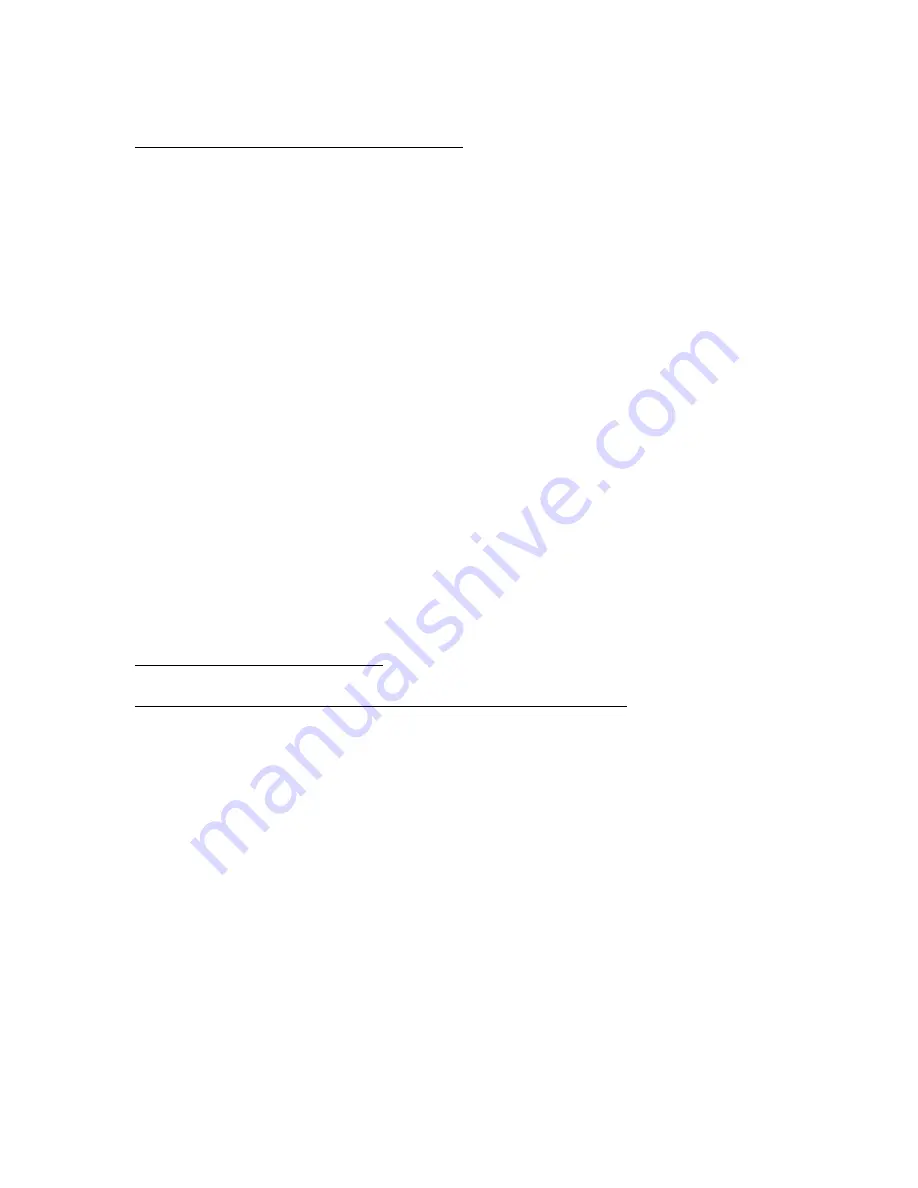
Ver: 10/14/2004 7
Driving screws with Adjustable Clutch - Tips
Factors affecting torque with self-drilling screws include: 1) Drilling speed 2)
Drilling Torque required 3) Threading Torque required to thread 4) Head seating Torque to
prevent breakage or stripping.
These factors vary with material thickness. Drilling speed must be lower for thick
material due to heat buildup and wear of drill point. Threading torque increases with
thickness. Head seating torque must be low enough to prevent fastener spin out or stripping,
in thin to moderate thickness when the head seats. Over torque can break off heads.
The correct torque setting must be high enough to drill, thread and seat the fastener but low
enough to prevent stripping or head breakage. This is quickly determined by listening to the
sound of the tool in action. The clutch buzzes when the clutch releases,
this should occur
for only ½ a second at the point when the screw seats down properly.
If short buzzing intermittently is heard while driving but the screw still seats properly, the
torque setting should be increased further. The clutch is releasing, probably while threading,
which normally requires more torque than drilling.
If you drive a screw and no buzzing is heard on seating, the screw is probably spinning at the
bottom and is stripping out the newly formed threads in the metal; reduce the clutch setting
and try again. In very thin material <22 ga, using the depth control as well may be required
for satisfactory results.
Approximate settings for MK6827
Thickness of Mild steel sheet Approx. Torque Setting
.032 inches (20 ga) … … … … … … … … … … ..… … .1
.072 inches (14 ga) … … … … … … … … … … … ..… .2.5
.125 inches (10 ga) … … … … … … … … … … … .… ...4
.190 inches (3/16) … … … … … … … … … … … … … 5
________________________________________________________________
¼ - 1/2 inch Aluminum (Tek 5 screw)… … … … … … … … ..5
(for thicker steel – use the HITACHI W8VB driver)
Summary of Contents for VISLIDER CH7260 METAL PRO
Page 11: ...Ver 10 14 2004 11 ...