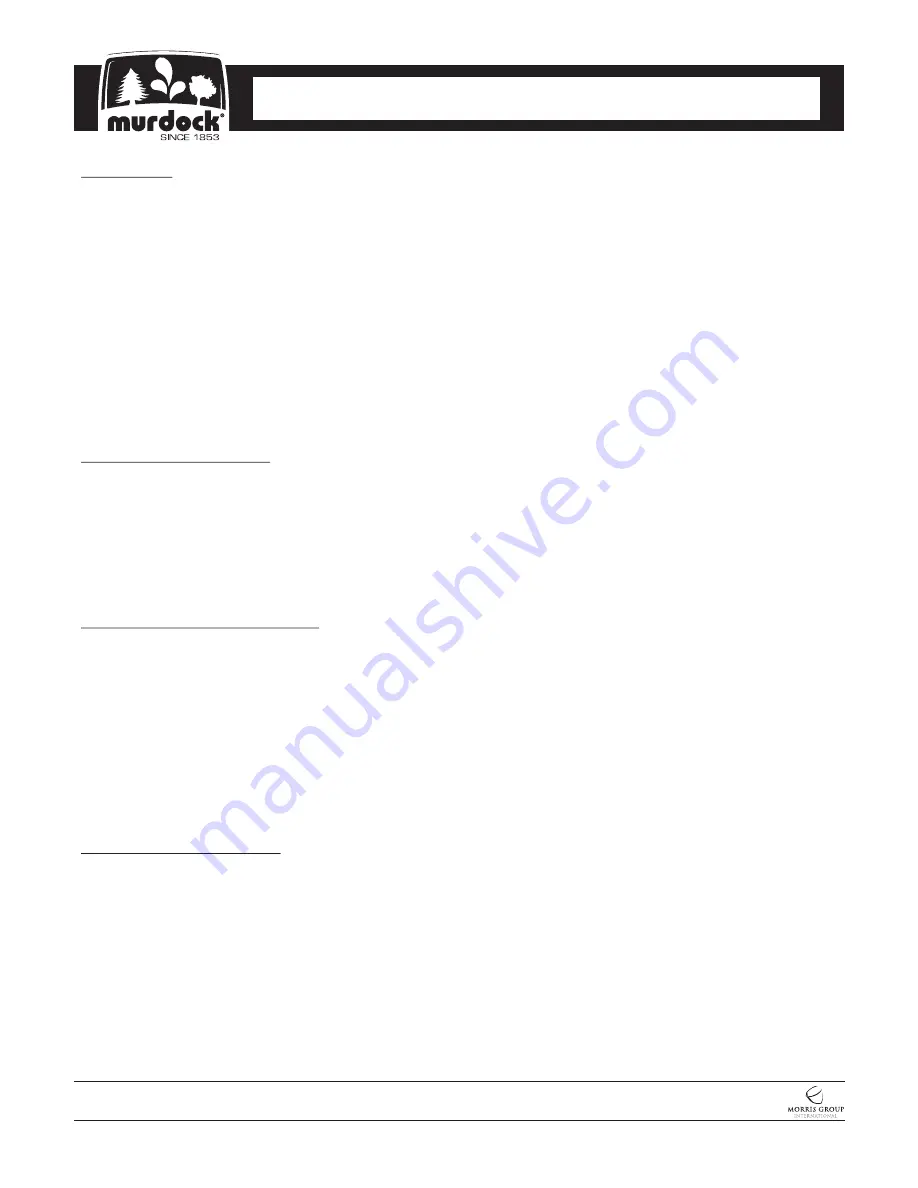
IMPORTANT:
1.
Water Supply Service Stop Valve, and Water Connections to be supplied by others in accordance with local
codes.
2.
Waste is 1-1/4” Outer Diameter. Drinking Fountain water inlet is 1/4” outer diameter Push-In Fitting. Bottle
Filler water inlet is 1/4” Outer Diameter Push-In Fitting. Water line by others.
3.
Completely flush Supply Lines of all foreign debris before connecting to fixture.
4.
Do NOT solder Tubes inserted into the Chiller, Bottle Filler or the Fountain Strainer as damage to the O-
Rings on the Push-In Fittings may result.
5.
All burrs must be removed from outside of cut Tubes before inserting into Strainer or other components.
6.
WARNING: Warranty is voided if installation is not made following current Murdock Mfg. installation
instructions and if components are assembled to the fixture that are not approved by Murdock Mfg.
7.
Fixture operates within water pressure range of 25 PSIG (174 kPa) to 105 PSIG (724 kPa).
8.
Per UPC 609.10
-All building Water Supply Systems in which quick acting Valves are installed shall be
provided with devices to absorb the hammer caused by high pressure resulting from the quick closing of the
Valve. These pressure-absorbing devices shall be approved mechanical devices. Water pressure-absorbing
devices shall be installed as close as possible to the quick closing Valve
PRIOR TO INSTALLATION:
1. Read all installation instructions carefully, before proceeding.
2. Carefully remove all fixture components from packaging, preventing scratching or damage. Inspect fixture and
all parts from damages and all parts that are bolted on.
3. Provide mounting surface, adequate to support the fixture and loads on the fixture.
4. Provide rough-ins as shown on the roughing-in and dimensional drawing, including Water Supply and Drain
Pipe (See rough-in details)
5. Completely flush water Supply Lines of all foreign debris, before connecting to the fixture.
DRINKING FOUNTAIN START UP:
1.
Before connecting Power Supply, but after thoroughly flushing the Supply Line and connecting it to the
Cooler, turn on the building Water Supply and check all connections for leaks.
2.
Air within the Drinking Fountain System or the Structure Supply Piping will cause an irregular Bubbler outlet
stream until purged out by incoming water. Covering the Bubbler with a clean cup (or similar object) is
recommended when first activating Drinking Fountain to prevent excessive splashing.
3.
Depress self-closing Pushbutton until steady water stream is achieved.
4.
If water flow requires adjustment, insert a slotted narrow blade Screwdriver in the hole centered on the
underside of the fixture in the knee clearance area up to the Flow Regulator. Turning clockwise will increase
flow and turning counterclockwise will decrease flow.
5.
Recheck all water connections with water flowing through system.
BOTTLE FILLER START UP:
1.
Pushbutton Operated:
Air within the bottle filler system or the structure supply piping will cause an irregular
spout outlet stream until purged out by incoming water. Press and hold pushbutton until steady water stream
is achieved
2.
Sensor Operated:
Hold container to be filled just below the sensor in the center of the filler spout and then
move the container upward and water flow will start automatically. When the container is almost filled, lower
the container below the sensor until the water stops flowing. (See label on the bottle filler.)
I N S TA L L AT I O N / M A I N T E N A N C E I N S T R U C T I O N S
CONTEMPORARY WATER COOLERS
I N S TA L L AT I O N / M A I N T E N A N C E I N S T R U C T I O N S
M-OBR4-GRC
Page 3 of 16
New: 12
/19/17
7020-963-001
MURDOCK MFG. •
15125 Proctor Avenue • City of Industry, CA 91746 USA
Phone 800-453-7465 or 626-333-2543 • Fax 626-855-4860 • www.murdockmfg.com
Member of
OUTDOOR BOTTLE FILLERS