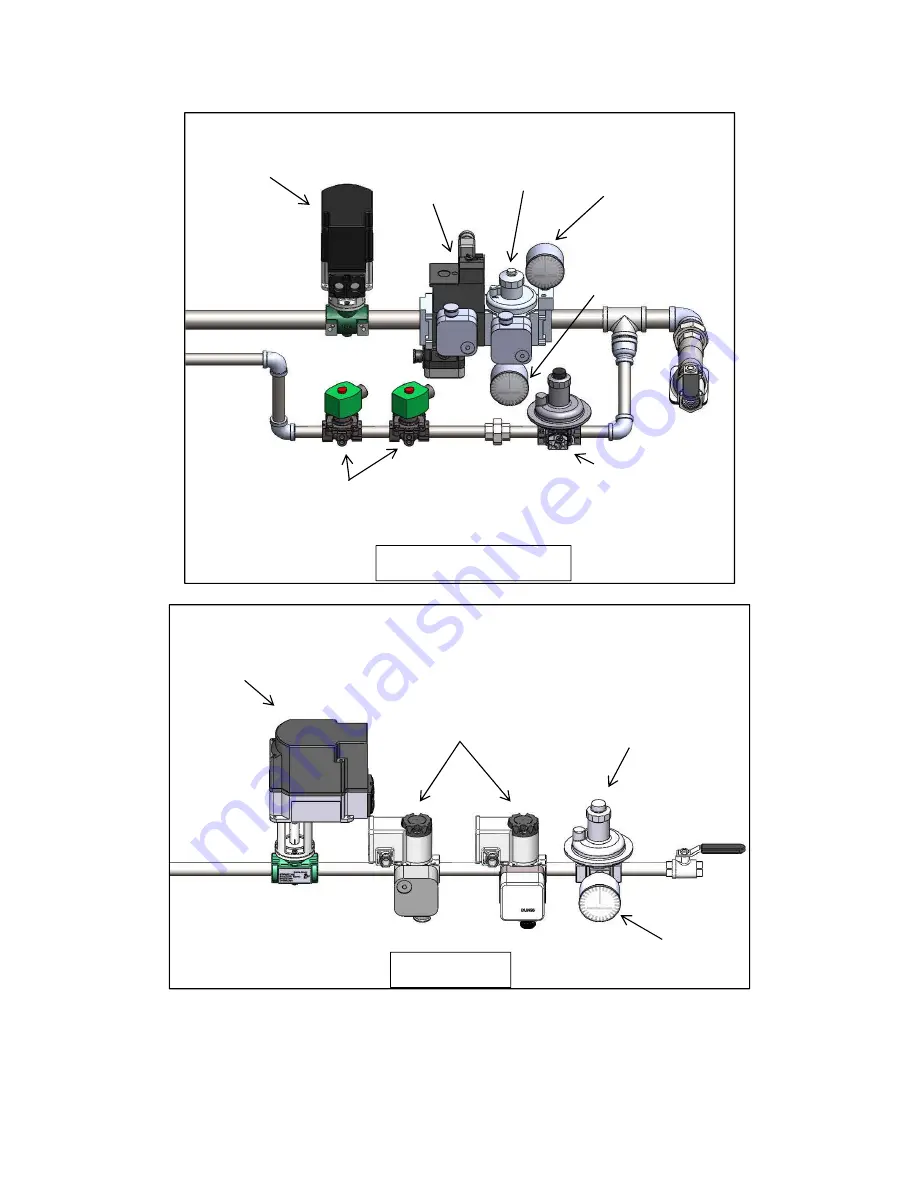
Manual#
I27028
6-13
Rev. 2 – 11/22/2017
Figure 6-4
GAS TRAIN ARRANGEMENTS
1.
Before beginning the test, close the manual gas valve that is located farthest
down-stream.
Modulating
Gas Valve
Safety Shut
Off Valves
Main Gas
Regulator
Supply Gas
Pressure
Gauge
Regulated Gas
Pressure
Gauge
Pilot Shut Off
Valves
Pilot Gas
Regulator
R10 & R15 Gas Trains
Modulating
Gas Valve
Safety Shut
Off Valves
Main Gas
Regulator
Regulated Gas
Pressure Gauge
R05 Gas Train
Summary of Contents for R Series
Page 5: ...Manual I27028 Rev 2 11 22 2017 ...
Page 64: ...Manual I27028 7 10 Rev 2 11 22 2017 7 11 TERMINAL BLOCK WIRING INSTRUCTIONS ...
Page 67: ......
Page 68: ......
Page 69: ......
Page 70: ......
Page 71: ......
Page 72: ...Munters ...
Page 73: ...Munters ...
Page 74: ...Munters ...
Page 75: ...Munters ...
Page 76: ...Munters ...
Page 77: ...Munters ...
Page 78: ...Munters ...
Page 79: ...Munters ...
Page 80: ...Munters 6ES7 232 4HA30 0XB0 ...
Page 81: ...Munters ...
Page 82: ...Munters ...
Page 83: ...Munters ...
Page 84: ...Munters ...
Page 85: ...Munters ...
Page 86: ...Munters 6ES7 232 4HA30 0XB0 ...
Page 88: ...Munters ...
Page 89: ...Munters ...
Page 90: ...Munters ...
Page 91: ...Munters ...
Page 92: ...Munters ...
Page 93: ...Munters ...
Page 94: ...Munters ...
Page 95: ...Munters ...
Page 96: ...Munters ...
Page 97: ...Munters 6ES7 232 4HA30 0XB0 ...
Page 98: ...Munters ...
Page 99: ...Munters ...
Page 100: ...Munters ...
Page 101: ...Munters ...
Page 102: ...Munters ...
Page 103: ...Munters ...
Page 105: ...Munters ...
Page 106: ...Munters ...
Page 107: ...Munters ...
Page 108: ...Munters ...
Page 109: ...Munters ...
Page 110: ...Munters ...
Page 111: ...Munters ...
Page 112: ...Munters ...
Page 113: ...Munters ...
Page 114: ...Munters 6ES7 232 4HA30 0XB0 ...
Page 115: ...Munters ...
Page 116: ...Munters ...
Page 117: ...Munters ...
Page 118: ...Munters ...
Page 119: ...Munters ...
Page 121: ...Munters ...
Page 122: ...Munters ...
Page 124: ...Munters ...